Military Circuit Board is pcb board that is specifically used in military applications, with higher reliability and safety requirements. The thickness requirements of military PCBs are more stringent than those of general applications. This is because the military field of electronic equipment reliability and stability have very high requirements. The thickness of the PCB directly affects the performance and stability of the circuit board, so it must ensure its accuracy and consistency.
Military PCB, the choice of materials is indeed very important. This is mainly because of the need to meet some special performance requirements, such as high-temperature resistance, corrosion resistance, high reliability, and long life.
Such PCB must be able to withstand higher temperatures. In military applications, equipment may be exposed to high temperatures, so the PCB must be able to withstand such temperatures to ensure that the electronic components inside are not damaged.
Better corrosion resistance is required. In some cases, military equipment may operate in harsh environments, such as in corrosive environments like salt spray or acid fog. Therefore, it must be able to resist these corrosive environments.
It also needs to have high reliability and long life. Military equipment usually needs to work in harsh environments for a long time, so the PCB must be able to ensure the stability and reliability of its electronic components and to have a long service life.
It also needs to have some other characteristics, such as low noise, and low power consumption. These characteristics can ensure the normal operation of military equipment, and improve its performance!
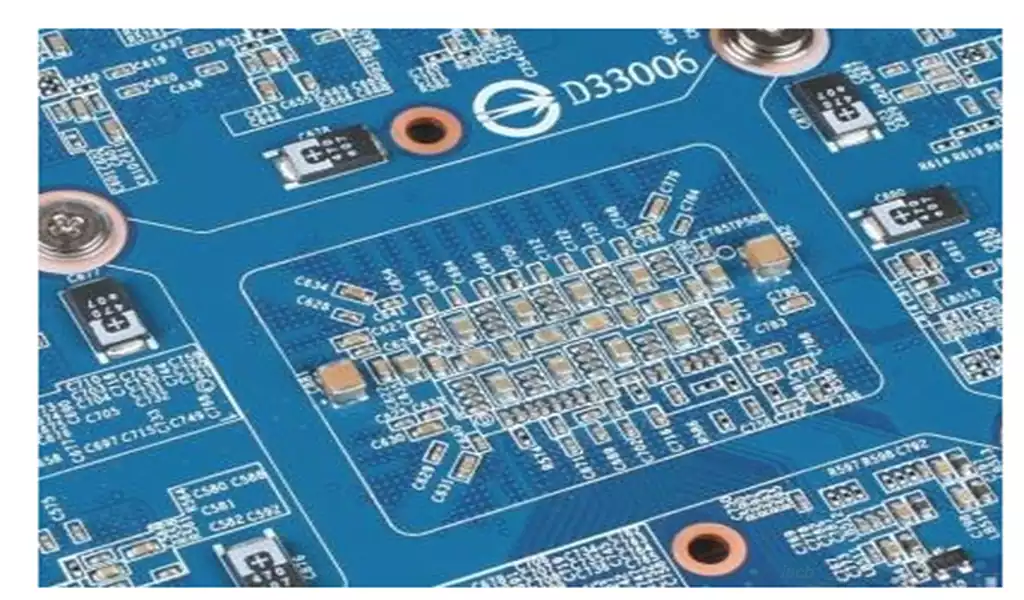
The manufacturing of military PCBs involves several complex steps:
Material preparation: Firstly, suitable substrates, copper foils, and other auxiliary materials need to be selected. These materials need to have excellent electrical properties, mechanical properties, and environmental resistance.
Cutting and drilling: According to the dimensions of the product and the design requirements, the large PCB substrate is cut to the appropriate size. At the same time, drilling operations are required to prepare for subsequent circuit production.
Pre-treatment: The PCB substrate is cleaned and pre-treated to remove surface dirt and contaminants to ensure smooth circuit production.
Circuit fabrication: Printing circuit graphics on the PCB substrate to form circuit conductors. This step can use a variety of methods, such as screen printing, laser direct imaging, etc.
Mounting Components: According to the design requirements, electronic components are mounted onto the PCB. This step requires the use of precision mounter and the corresponding components.
Soldering and curing: Connect the components to the conductive path on the PCB through soldering and ensure the reliable quality of the solder joints. For some special requirements of the components or solder joints, special treatment or a specific welding process is required.
Testing and maintenance: In the manufacturing process, the printed PCB board needs to carry out several tests to ensure that its electrical and mechanical properties meet the requirements. For unqualified PCBs, repair or rework is required.
Assembly and Integration: Multiple PCBs are assembled and integrated according to design requirements to form a complete military product. This may require the use of various connectors and interfaces.
Testing and Verification: After manufacturing, the military circuit board needs to be rigorously tested and verified to ensure stable and reliable performance. This step can include electrical performance testing, environmental adaptability testing, and reliability assessment.
Packaging and Transportation: Finally, appropriate packaging and labeling are performed according to the requirements of the product to ensure that it will not be damaged during transportation and storage.
Military circuit board, as critical electronic components in the military field, have rigorous thickness requirements and face technical challenges. It is only through precise material selection, manufacturing process, and rigorous testing and validation that military PCBs can be guaranteed to operate stably and reliably in complex and harsh environments.