Mini Drone PCB is a circuit board specifically designed for use in UAV equipment, featuring miniaturization, high integration, and high reliability. These boards are typically manufactured using High-Density Interconnect (HDI) technology, which allows for complex circuit designs and the mounting of tiny components to meet the stringent requirements of UAVs in terms of size, weight, and performance.
Drone PCB board manufacturing process requirements:
A high-precision manufacturing process is required to ensure precision requirements for the size, shape, and thickness of the circuit boards. At the same time, high-precision materials and equipment, such as high-precision cutting machines and laser drilling machines, need to be used to improve manufacturing accuracy and reduce errors.
Since the micro pcb board needs to realize complex circuit design and installation of tiny components, high-density interconnection technology is required to realize high-density integration of circuits and reliable connection of tiny components. This requires the use of fine circuit design and wiring techniques, as well as high-quality soldering and packaging techniques. The integration of multiple electronic components tends to generate a large amount of heat. Therefore, an efficient thermal design is required to ensure the board’s thermal performance and stable operation. This requires the use of advanced thermal designs and materials, such as heat sinks and thermally conductive adhesives.
Since the mini drone PCB is susceptible to electromagnetic interference during operation, it requires electromagnetic shielding and anti-interference capabilities. This requires the use of effective electromagnetic shielding technology and filtering technology to reduce the impact of electromagnetic interference on the circuit board. In addition, it needs to run stably for a long time, so it needs to have reliability and stability. This requires the use of high-quality materials and manufacturing processes, as well as adequate testing and verification to ensure the reliability and stability of the circuit board.
The application scenarios for micro UAV printed circuit boards are very wide:
It has a wide range of applications in the military field, including reconnaissance, intelligence gathering, target tracking, striking, and other tasks. Its small size, lightweight, and good concealment make micro drones ideal for military reconnaissance and strike operations.
They are also widely used in the civilian field, including aerial photography, terrain mapping, environmental monitoring, agricultural plant protection, express delivery, and disaster rescue. For example, in the field of aerial photography, micro UAVs can carry miniature cameras and sensors for high-definition shooting and monitoring of target areas, providing accurate data support for terrain mapping and environmental monitoring.
It can also be applied in various scientific research, such as meteorological observation and physical experiments. For example, in meteorological observation, micro UAVs can carry sensors such as temperature, humidity, air pressure, etc., to carry out high-precision measurement and monitoring of the atmospheric environment.
With the continuous development of mini drone PCB technology, more and more commercial fields are also beginning to apply micro drone printed circuit boards.
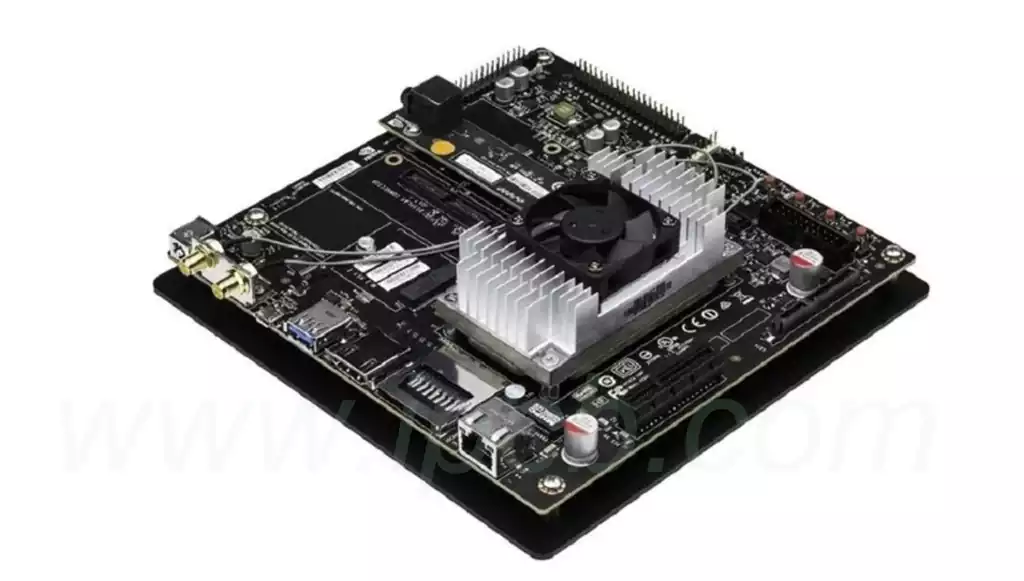
Advantages:
Manufactured with high-density interconnection technology, complex circuit designs can be realized in a smaller space, thus reducing the size and weight of the UAV, making it more portable and flexible.
With high reliability and stable electrical performance, it can ensure the normal operation of the UAV in various environments, improving the performance and stability of the UAV.
It can realize high integration of multiple functional modules, reducing the use of external connectors and cables and improving the simplicity and reliability of the UAV.
It can be customized according to the specific needs of different UAVs to meet the needs of various special application scenarios.
Disadvantages:
Higher cost: the production of mini PCB board requires the use of high-precision manufacturing processes, resulting in a relatively high cost and limiting their use in some low-cost application scenarios.
Difficulty in maintenance: as the micro UAV printed circuit board integrates multiple functional modules, once a fault occurs, it is difficult to repair and requires specialized personnel to handle it.
Sensitive to electromagnetic interference: Since the mini drone pcb adopts high-density interconnection technology, it is easily affected by electromagnetic interference and needs to take corresponding electromagnetic shielding and filtering measures during design.
As the core control system of the UAV, the mini Drone PCB bears the important task of realizing the basic control and auxiliary functions of the UAV. In the actual process of designing and manufacturing UAVs, we need to choose the right UAV pcb according to specific scenarios and needs, and ensure that their performance and quality meet the requirements, to ensure that UAVs can fly safely and stably.