OSP plating, as a printed circuit board copper foil surface treatment of a RoHS-compliant process, is an abbreviation of Organic Solderability Preservatives, which uses chemical methods to form a layer of organic skin film on the clean bare copper surface. This film not only prevents the copper surface from rusting in the normal environment, but is also easy to be removed by the flux in the subsequent soldering process, ensuring a strong solder joint. It is also known as Organic Tin Protective Layer.
Types of OSP
BTA (Benzotriazole): BENZOTRIAZOLE
BTA is white with yellowish odorless crystalline fine powder, in acid and alkali are very stable, and not easy to redox reaction, can form stable compounds with the metal. ENTHON will be dissolved in methanol and aqueous solution for sale, as copper surface antioxidant (TARNISH AND OXIDE RESIST), the trade name of the CU-55 and CU-56, CU-56 treatment of copper surface can be The copper surface treated with CU-56 can produce a protective film to prevent the rapid oxidation of bare copper.
AI (Alkyl Imidazole) ALKYLIMIDAZOLE PREFLUX is the beginning of the early ALKYLIMIDAZOLE as a protective agent for copper, developed by the Shikoku Chemical Company in Japan first commodity, applied for a patent in 1985, used for etch resist (ETCHING RESIST), but due to the color is transparent detection is not easy, not a large number of use. Subsequently, GLICOAT was introduced, which was derived from GLICOAT.
GLICOAT-SMD (E3) has the following characteristics:
-Compatible with flux and maintains good solderability.
-Resistant to high heat soldering process
-Prevents oxidization of copper surface
ABI (Alkylbenzimidazole) ALKYLBENZIMIDZOLE
Alkylbenzimidazole (ALKYLBENZIMIDZOLE), developed by Mitsuwa in Japan, is a moisture-resistant copper protectant called CUCOAT A. It can be used in the soldering process. CUCOAT A is a moisture-resistant copper protectant, which can produce COMPLEX COMPOUND with copper atoms to prevent oxidation of the copper surface, and is compatible with all kinds of solder pastes and has a positive effect on the solderability.
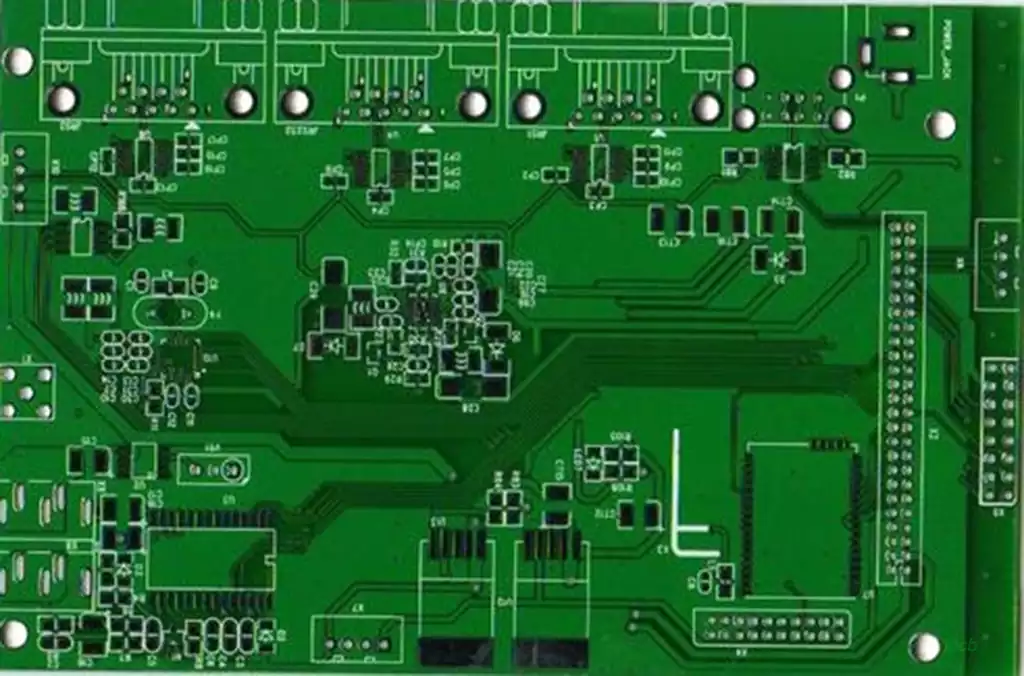
osp process flow:
Cleaning the PCB surface:
Before the OSP process begins, the PCB surface must be thoroughly cleaned to remove all dirt and grease and to ensure that the surface is dry and free of impurities.
Deposition of OSP plating:
After cleaning and drying the PCB surface, it is then necessary to evenly spray or dip-coat the OSP coating on it. This process requires precise control of the concentration and thickness of the coating to form a uniform organic protective film.
Drying the OSP coating:
After the OSP coating has uniformly covered the circuit board surface, it needs to be placed in an oven for drying. During the drying process, the temperature and time must be strictly controlled to ensure that the coating dries completely and forms a strong protective film.
Inspection and testing of PCBs:
After completing the OSP process, the PCB board must be strictly inspected and tested. Inspection requires attention to details such as the surface quality of the board, the quality of the solder joints and pins. At the same time, a series of tests must be conducted to ensure that the electrical performance and reliability meet the predetermined standards.
Since OSP coatings are made of organic materials, they may be less resistant to heat and corrosion than other processing technologies. Therefore, for specific applications, it may be necessary to seek alternative surface treatments that are more resistant to heat or corrosion.
In the electronics manufacturing industry, OSP plating is used on a wide variety of PCB board, but they are particularly frequently used on the following specific types of PCBs:
Multilayer PCBs: OSP coatings are widely used because multilayer PCB often have complex circuit layouts and high-density designs. Multi-layer PCB boards include an inner layer of copper wires and an outer layer of pads, OSP coating not only protects these exposed copper wires, but also ensures excellent soldering performance.
Ultra-thin PCB boards: Ultra-thin PCB boards are commonly found in mobile devices, tablets and other small electronic devices. The thickness of these boards is often less than 0.2 millimeters, and because of their unique size and performance requirements, OSP coatings are used to provide the necessary protection and solderability.
Flexible PCBs: Flexible PCBs are manufactured with flexible substrates for application scenarios that require bending or folding.OSP coating is suitable for flexible PCBs because it provides a light protective layer while maintaining good solderability.
Advantages of this surface treatment process on metal surfaces:
Extremely environmentally friendly. The use of organic compounds as a protective layer avoids the use of toxic and hazardous metals, which not only reduces environmental pollution, but also meets modern environmental standards. Compared to the traditional hot fly plating process, it significantly reduces the generation of harmful emissions and waste water.
Demonstrates good soldering performance. The protective film formed by this process has excellent flatness and finish, which contributes to the uniform spreading and wetting of solder, thus ensuring the reliability of the soldered connection. At the same time, its film properties make the PCB dimensions virtually unaffected.
Highly adaptable. This surface treatment process can be applied to many types of PCB substrates, such as glass fiber, organic fiber, aluminum substrate, etc. It is also suitable for a variety of soldering methods, such as wave soldering and reflow soldering. In addition, it can be used in combination with other surface treatment processes, such as electroplating, chemical tin plating, etc., to further enhance the reliability and corrosion resistance of the PCB.
Helps reduce costs. Compared to other surface treatment processes, the process does not require expensive metal materials or complex equipment and processes, thus reducing manufacturing costs. At the same time, its excellent solderability and stability reduce the need for repairs and rework, resulting in further cost savings.
This process of chemically forming an organic skin film on the surface of bare copper not only excels in environmental friendliness, soldering performance, and adaptability, but is also cost-effective, bringing significant advantages to the PCB manufacturing industry.
OSP plating process as PCB surface treatment of environmental protection and efficient technology, with its unique advantages in the electronics manufacturing industry occupies an important position. Both its excellent environmental protection, soldering performance, and wide range of adaptability and cost-effectiveness make it an ideal choice for many PCB boards. Especially in specific applications such as multilayer, ultra-thin and flexible PCBs, it plays an irreplaceable role.