With the rapid development of science and technology,printed circuit boards (PCBs) are more and more widely used in electronic equipment. PCB Board Soldering as a key link in the PCB manufacturing process,its quality directly affects the function and reliability of the entire circuit board.
Overview of welding technology
Welding technology is a method of connection through molten metal, widely used in the electronics industry. In the circuit board manufacturing process, welding is an important means of connecting components and PCB circuit boards together. The quality of welding is directly related to the functionality and reliability of the circuit board, therefore, it is crucial to choose the appropriate soldeing technology and method.
PCB board welding process
Pre-processing
Before welding, the PCB circuit board needs to be cleaned to remove surface dirt, oxides and other impurities to ensure the cleanliness of the welding surface. At the same time, you need to check whether the PCB circuit board pad is intact to ensure that there is no damage or pollution.
Coating flux
Flux is a substance that can facilitate the soldering process.Before soldering,an appropriate amount of flux needs to be applied to the pads of the PCB to enhance solderability. Choosing the right flux is one of the most important factors to ensure the quality of welding.
Component placement and fixation
Place the components to be soldered in the corresponding position on the PCB circuit board, and ensure the stability and correctness of the components. For some small components, you can use clamps or suction cups for fixing to ensure that the components will not move during the welding process.
Soldering
Select the appropriate welding equipment and tools, such as a soldering station, soldering nozzle and so on. Adjust the soldering temperature and time according to the size of the components and the size of the pads to ensure that the solder melts and connects well with the components and the PCB board. During the soldering process, you need to control the temperature, time and uniformity of the heat source to avoid overheating or localized overheating leading to damage.
Inspection and Repair
After completing the soldering, quality inspection is performed to ensure that each solder joint meets the requirements. Repair the unqualified solder joints, such as re-welding or using filler. At the same time, you need to check whether the components are damaged or shifted, if necessary, then adjust accordingly.
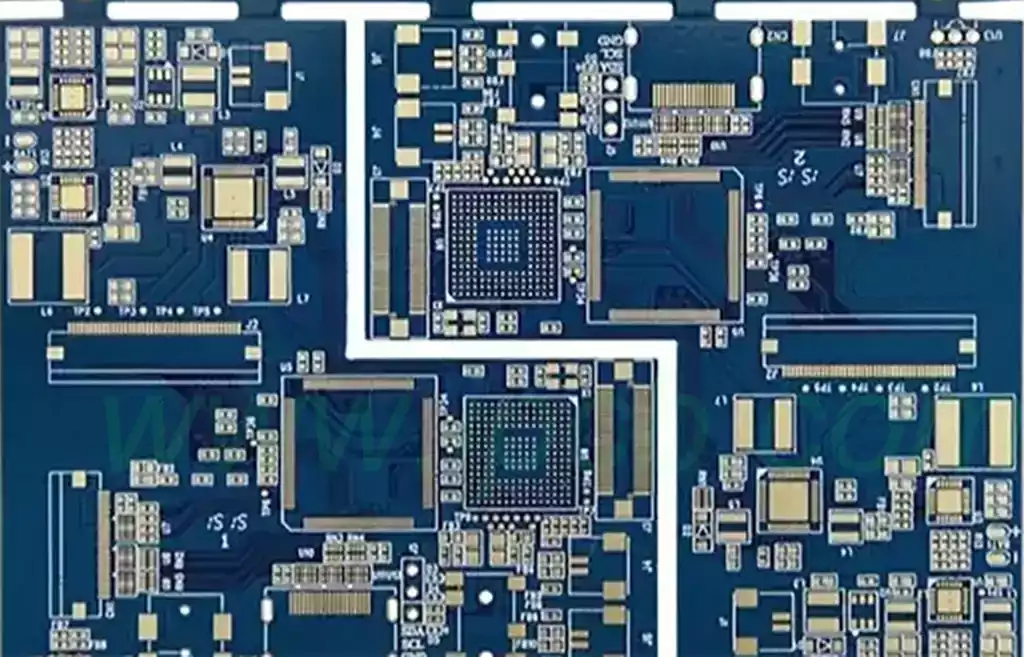
PCB board soldering process flow
1.Welding materials
(1) solder: usually used in accordance with U.S.general standards Sn60 or Sn63 solder,or HL-SnPb39-type tin-lead solder.
(2) flux: usually can be used rosin flux or water-soluble flux,the latter is generally used only for wave soldering.
(3) cleaning agent: should ensure that the printed circuit board corrosion-free,non-polluting,generally using anhydrous ethanol (industrial alcohol), trichlorotrifluoroethane, isopropyl alcohol (IPA), aviation detergent gasoline and deionized water and other cleaning agents for cleaning.Specifically what cleaning agent cleaning should be selected according to process requirements.
- Welding tools and equipment
(1) soldering iron reasonable choice of power and type of soldering iron, to improve the welding quality and efficiency has a direct relationship. It is recommended to use low-voltage temperature control of the soldering iron, soldering iron head can be used nickel-plated, iron or copper material, the shape should be based on the needs of welding.
(2) wave soldering machine and reflow soldering machine suitable for industrial mass production of one of the welding equipment.
- Welding preparation
(1) According to the list of components to check the component model, specifications and the number of components to meet the requirements.
(2) Welding personnel with anti-static wrist, to confirm the thermostatic iron grounding.
- Soldering order
Component welding order is resistors, capacitors, diodes, transistors, integrated circuits, high-power tubes, other components are first small and then large. - Welding process
Printed circuit board welding process mainly requires manual insertion, manual welding, repair and inspection. General operating steps are shown below:
(1) according to the production task to select the appropriate model of the BOM list, according to the BOM list to check the incoming printed circuit board type is correct, the circuit board has no damage.
(2) Check whether the printed circuit board surface is clean and dust-free, no oil, fingerprints, etc., if not thousands of clean Xu with alcohol to properly clean, clean and need to wait until the alcohol completely evaporated before welding.
(3) Select the appropriate device according to the BOM, and carefully check the device model, number, while checking the device surface, pins, etc. whether there is damage or rust marks and other factors affecting the performance of the device.
(4) To be devices and printed circuit board type and number of confirmation, according to the BOM device corresponding to the labeling and circuit board position, the device will be inserted into the circuit board.
(5) Weld the devices according to the welding requirements to ensure that the welding without leakage, false welding, etc..
(6) After welding, cut off the excess pins.
(7) Check the solder joints, there is no unqualified items, such as repair.
(8) After welding, the printed circuit board must be thoroughly cleaned in a timely manner in order to remove residual flux, oil and dust and other contaminants, the specific cleaning process according to process requirements.
The factors affecting the quality of PCB circuit board welding
Temperature: temperature is the key factor affecting quality. Too high a temperature may lead to components and PCB circuit board damage; too low a temperature may lead to welding or false welding.
Time: time is also an important factor affecting quality. Too long a time may lead to too large a solder joint or excessive melting; too short a time may make the solder is not fully melted, resulting in a weak connection.
Flux: flux in the welding process to promote the role of welding. Choose the right flux can improve the solderability and reliability of welding.
Solder: The composition and purity of the solder will also affect the quality of the solder. Low melting point of the solder is easier to melt, but too low a melting point may lead to a weak connection; high purity of the solder can improve the reliability of welding.
Handling skills: The skill and experience of the operator is also an important factor in the quality of the solder. Correct operating techniques and specifications can ensure the quality and stability of welding.
PCB board Soldering is an important part of the electronic equipment manufacturing process. By mastering the basic principles and technical requirements of welding, following a reasonable process flow, and paying attention to the accumulation of practical experience and skills, the quality and reliability of welding can be ensured. At the same time, continuous quality control is also one of the key measures to improve productivity and product quality.