PCB board testing is an extremely important step in the production process and is an essential production process. It is to check the rationality of PCB design, test its possible problems or defects in the production process, to ensure the functionality and appearance of the product, and improve the production yield of the final product.
Several testing methods for bare PCB boards
AOI Testing.
AOI automatic optical inspection equipment in various industries have been more widely used in the PCB processing process, as an important testing equipment, the key quality assurance tools are also widely used.
AOI in the electronic board production process,also known as the middle test, he is in the circuit board after the copper foil etched line graphics for testing. The equipment scans the graphics on the board for comparison with the design documents, distinguishing the circuit board graphic condition, and then with the AOI itself hosts the circuit board graphic data for comparison,there is a difference in the position of the defects reported, and finally through the inspector to confirm the processing in order to complete the entire testing process.
Flying probe test:
Flying probe testing is a highly recognized and effective form of testing to detect production quality problems, and flying probe testing has been proven by the industry to be a particularly cost-effective test method for raising board standards.
Flying probe testing uses two or more independent probes that operate without a fixed test point.These probes are electromechanically controlled and move according to specific software instructions. As a result, flying probe testing has a low initial cost and is not as efficient compared to fixture testing – after all, flying probe testing moves the probes one point at a time, making it practical for small orders.
Fixture test:
Fixture is a circuit board as a model and designed for electrical properties of a special fixture through the test, there is a single-sided fixture, double-sided fixture points.
Printed wiring board electrical test first need to make a set of test fixtures, through the fixture metal probe connected to the printed circuit board pads or test points, in the case of the electronic board is charged, to obtain the test circuit voltage value,current value and other typical values, so as to observe whether the test circuit is on normal. The advantage of using electrical testing is high test efficiency,the disadvantage is that the cost is also high, each type of pwb need to open a different test fixture, therefore, the fixture test is practical for high-volume orders.
Manual visual inspection:
Test visual inspection pcb is the most traditional inspection method, the advantage is the low initial cost and no test fixture.By using a magnifying glass or calibrated microscope visual inspection to determine whether the circuit board is qualified,and to determine when the need for calibration operations.
Visual inspection testing is only done on boards with simple circuits and has the disadvantages of subjective human error, high long term costs, discontinuous defect detection as well as difficult data collection. With the increase in electronic production and the reduction in wire spacing and component size, visual inspection testing methods are becoming less and less feasible.
Aging Test
Typically, printed circuit boards are subjected to extreme aging tests by applying power to the boards and subjecting it to the extreme harsh environments permitted by the design to see if it can meet the design requirements. Aging tests typically take 48 to 168 hours. However, this test is not suitable for all purpose PCB board and ageing tests can shorten the life of the PCB substrate.
X-ray Inspection Testing
X-rays are used to check the connectivity of the wiring,and the inner and outer layers of the wiring for bulges and scratches.2-D and 3-D AXI tests are available, with 3-D AXI being more efficient.
Functional Test (FCT)
Functionality testing (FCT) usually simulates the operating environment of the product under test and is done as a final step before final manufacturing.The test parameters are usually provided by the customer and may depend on the end use of the PWB.A computer is usually connected to the test point to determine if the PWB product meets its intended capacity.
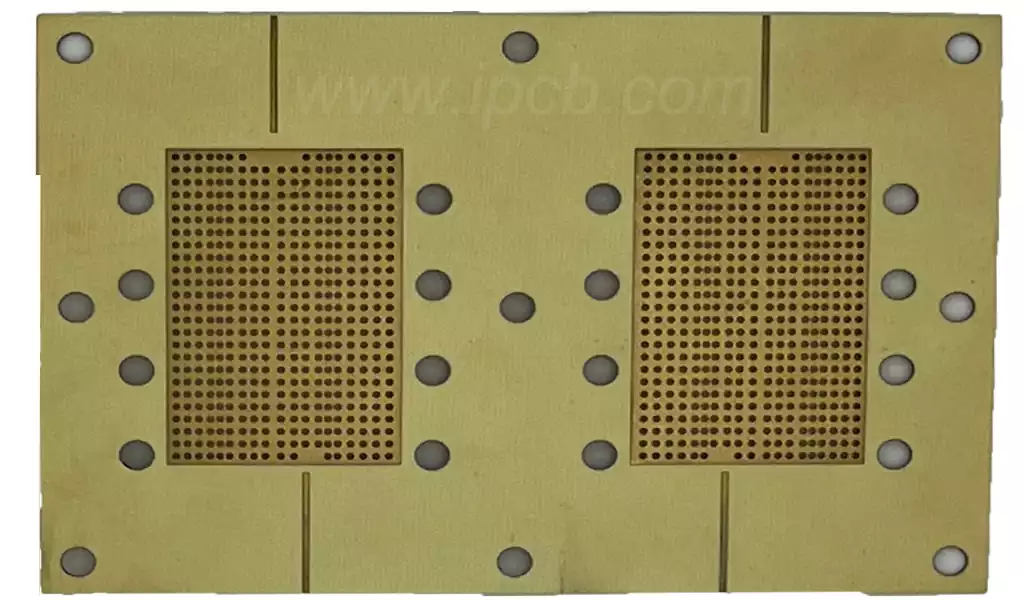
How to do a good test?
When conducting PCB testing, engineers should consider the following aspects:
① Test plan and strategy
Develop a detailed test plan and strategy, including test methods, test equipment and test procedures.This helps to organize and execute an effective testing process.
② Suitable test tools and equipment
Select suitable test tools and equipment to fulfill testing needs and detect problems accurately.Ensure the accuracy and reliability of test equipment.
③ Data Recording and Analysis
Record the test results and data and analyze them thoroughly, which helps to identify potential problems,verify the improvements involved and make accurate decisions.
④Compliance Requirements
According to relevant industry standards and regulations, ensure that the PCB design meets the appropriate compliance requirements and conduct the necessary compliance testing and certification.
PCB board testing is an important part of ensuring product quality and productivity.Through reasonable selection of testing methods, application of advanced equipment and attention to data recording and analysis, it can effectively improve the yield and quality of electronic production and contribute to the sustainable development of the electronics manufacturing industry.