PCB color is mainly determined by its substrate on the soldermask layer, the main role of the soldermask layer is to prevent welding solder flow freely, to avoid causing short circuits. The color of the soldermask can be achieved by adding different color materials, thus forming the colorful PCB boards we see.
The relationship between color and material
PCB color is closely related to the materials used. Common materials such as FR4, etc., the color selection is based on the manufacturer’s preference. Although color does not directly affect circuit performance, the uniformity of the color can be used as an indicator of the purity and quality of the material. If the color is uneven or defective, it may suggest that the material contains impurities or that there were problems during the manufacturing process.
The Relationship Between Color and Soldering
Soldering is a critical aspect in electronics manufacturing. A board with a dark background helps to better absorb the light generated during soldering, making the solder joints clearer and making it easier to control the quality of the soldering. At the same time, certain eye-catching colors such as red and yellow can enhance the recognition of soldering points and reduce soldering errors.
The relationship between color and heat dissipation
Heat dissipation is an integral part of electronic product design. Darker circuit boards can absorb more heat and help improve heat dissipation. However, too dark a color may also lead to excessive heat absorption in a high-temperature environment, affecting heat dissipation. Therefore, when choosing a color, you need to weigh the actual application scenarios.
The relationship between color and maintenance
When repairing electronic products, color has a certain impact on repair efficiency. Light-colored circuit boards make it easier for repairers to observe the circuit layout and components, reducing the difficulty of repair. At the same time, bright colors such as red and yellow help to quickly locate the fault point.
The relationship between color and cost
Different colors of pcb board affect manufacturing costs. Different pigments and manufacturing processes result in cost differences. For example, metallic colors such as gold and silver usually require higher manufacturing costs. Customizing circuit boards with special colors can also increase costs. Therefore, product positioning and budget need to be considered when choosing colors.
The relationship between color and electromagnetic compatibility
Electromagnetic compatibility is an important factor to consider in the design of electronic products. Dark-colored pcb substrate can help reduce electromagnetic radiation and improve the electromagnetic compatibility of the product. However, color is not the only means of solving electromagnetic compatibility problems, but also need to consider the circuit design and component selection.
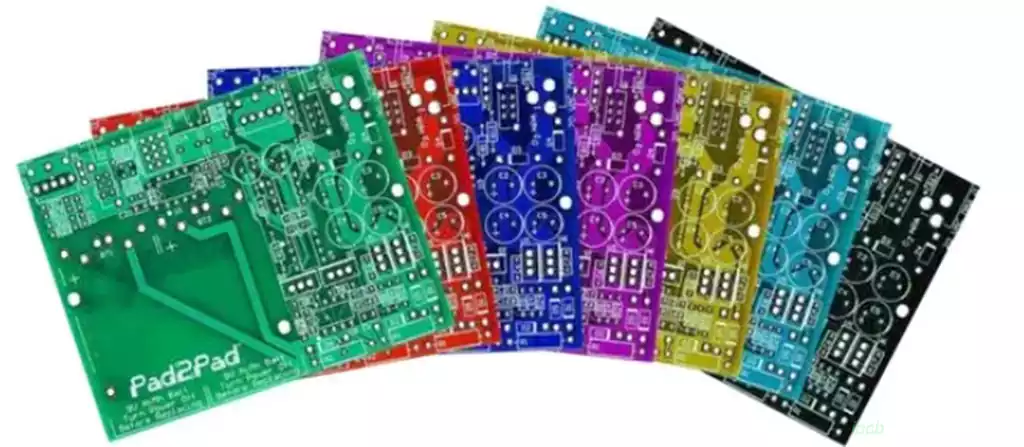
why pcb color is green
Low cost
Green PCB boards are widely used because of the cost advantage of mass production, which makes them relatively inexpensive, thus becoming the preferred color of many manufacturers.
Convenient development
During the PCB manufacturing process, green PCBs are easier to develop than other colors. This is because the color characteristics of green PCBs allow the developer to penetrate more effectively during chemical development, making it easier to remove unwanted parts.
Good visual effect
The high contrast of green PCBs makes metal pads and logos stand out more visually, thus improving board identification and ease of maintenance. In addition, green PCB boards are less fatiguing to the eyes and more visually comfortable for workers, especially when performing quality inspections in bright light environments.
At the same time, green PCB boards help to improve the precision and efficiency of soldering components during the SMT soldering process due to the better recognition of optical positioning calibration by the base color.
Good confidentiality
Green PCB board due to its universality, making the special design of the board more difficult to be guessed and imitated by outsiders, thus having better confidentiality. Some manufacturers in the market also choose to use black PCB boards for confidentiality considerations, because black PCB boards are more difficult to observe the wiring details, increasing the difficulty of copying the board.
Long history of use
Green PCB board has a long history of use, since the mid to late last century, the industry has gradually favored the use of green PCB board design. This is mainly because the high-end boards of the first-tier manufacturers use green design, making the green PCB board in the market has been widely recognized and applied.
Relatively safe and environmentally friendly
Compared with other colors of PCB, green PCBs perform better in terms of safety. For example, blue and black PCB boards use inks that may have conductive properties, there is a risk of short-circuit, while the green PCB boards are relatively reduced this risk. In addition, the green PCB board also has advantages in environmental protection, high temperature environment is not easy to release toxic gases, more in line with environmental requirements.
Behind the choice of PCB color lies a rich mystery. From the material, welding, heat dissipation, maintenance, cost to electromagnetic compatibility and other dimensions of consideration, green PCB boards have become the mainstream choice in the market because of its low cost, easy development, good visual effect, strong confidentiality, long history of use and relative safety and environmental protection.