Drilled holes are a critical part of the printed circuit board (PCB) manufacturing process, and the PCB drilled hole tolerance, i.e. the range of deviation between the drilled hole size and its design value, is directly related to the production accuracy and overall quality of the board. Therefore, the control of PCB drilling tolerances is not only the basis for ensuring stable circuit board performance, but also the key to enhancing product competitiveness.
PCB drilled hole tolerance requirements:
General circuit board holes are divided into two kinds of holes, one with copper holes and no copper holes, copper is mainly used for welding and conduction holes, no copper is mainly used for installation and positioning use.
If the metallization drilling, we need to first drill copper-free holes in the PCB board, and then plating a layer of copper foil in the hole wall, then if the tin spray process needs to make up 0.1-0.15mm, that is, the drill needs to be used 0.2-0.25mm, the specific size of each factory according to the production process and machinery and equipment; if it is the OSP, chemical gold and other processes need to make up 0.05-0.1 mm or so.
If it is non-metallized holes, that is, no copper holes, then make up the value of about 0.05mm, such as 0.1mm holes need to use 0.15mm drill, of course, generally no copper holes are larger holes, according to the actual size of the compensation correction.
Customers generally do not have to take into account our compensation size in the design process, general manufacturers in the production process will default to the customer’s hole information for the finished hole size, circuit board manufacturers will do the information, automatically designed to compensate for the tolerance. Produce the hole size that the customer wants.
Drilling tolerance: PTH: min +/-0.075mm
NPTH: min+/-0.05mm
CNC tolerance: min+/-0.1mm
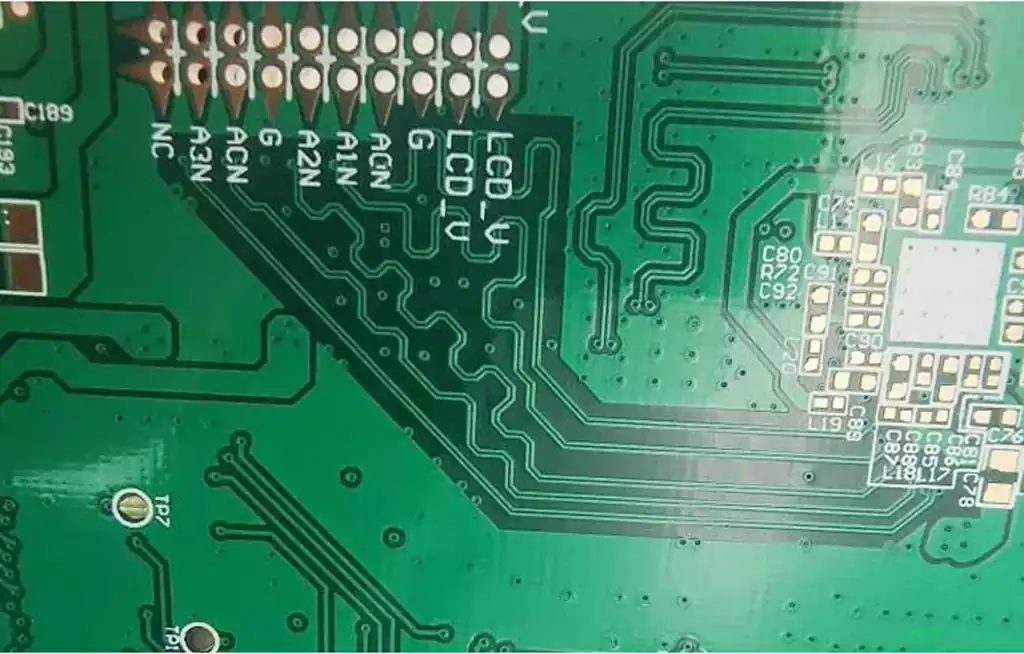
In order to realize the effective control of PCB drilling tolerance, we need to start from several aspects. Firstly, high-precision drilling equipment and tools should be selected to ensure the stability and accuracy of the drilling process. Secondly, the drilling process should be finely adjusted, including drilling speed, feed, use of coolant, etc., to reduce the tolerance range. In addition, it is also necessary to carry out strict quality inspection of the circuit board after drilling, so as to find and deal with possible tolerance problems in a timely manner.
In the actual production process, PCB drilling tolerance control is also affected by a variety of factors. For example, the hardness, thickness and thermal conductivity of the material and other factors will affect the accuracy of drilling. Therefore, when selecting PCB materials, it is necessary to fully consider its processing performance and drilling tolerance requirements. At the same time, the temperature, humidity and vibration of the production environment and other factors may also have an impact on the drilling tolerance, so it is necessary to effectively control these factors in the production process.
PCB drilled hole tolerance control is an important task in the manufacturing process of printed circuit boards. Through the selection of high-precision equipment, optimize process parameters and strengthen the quality of inspection and other means, you can achieve effective control of tolerances to ensure that the circuit board production accuracy and overall quality.