PCB reflow soldering refers to the heating and melting of pre-painted in the pad above the paste (paste is generally composed of tin powder and flux mixture), so that it returns to the liquid state of the flow (this process is reflow), so that the devices placed above the pad in advance and the full contact with the solder so as to achieve the purpose of the soldering.
Reflow soldering workflow is generally based on our PCB to open a good stencil, so that the stencil above the mesh and the board’s pads correspond, so that in the next process of brushing the solder paste to make each pad have enough solder paste, and then at this point you can place the components in the pads in the middle of the general order of placement of our order is from left to right, from top to bottom, from big to small placed, but also need to pay attention to the device identification of the Direction, after placing the good can enter the reflow soldering line above the processing, inside the machine will first go through the preheating zone, constant temperature zone, soldering zone, cooling zone, etc., after the previous steps out of the board processed after checking that there is no problem can be carried out in the next step of the production process, the nature of the reflow soldering is the control of the temperature to complete the welding (for example, leaded soldering and lead-free soldering compared to the melting point of the lead-free will be higher, and leaded will be lower) (e.g. leaded soldering compared to lead-free soldering, the melting point of lead-free will be higher, and leaded will be lower).
In the SMT reflow soldering process caused by uneven heating of the components are mainly due to: reflow components heat capacity or absorption of heat differences, conveyor belt or heater edge effects, reflow product load and so on three aspects.
- Usually PLCC, QFP and a discrete chip components compared to the heat capacity to be larger, soldering large-area components is more difficult than small components.
- In the reflow soldering furnace conveyor belt in the weeks to make the transfer of products for reflow soldering at the same time, but also become a heat dissipation system, in addition to the heating part of the edge and the center of the heat dissipation conditions are different, the edge of the general low temperature, the furnace in addition to the temperature requirements of the various temperature zones are different, the same temperature difference in the surface of the load.
- The impact of different product loading. Reflow soldering temperature curve adjustment should be considered in the no-load, load and different load factor can get good repeatability. Load factor is defined as: LF = L / (L + S); where L = the length of the assembled substrate, S = the spacing of the assembled substrate.
Reflow process to get good repeatability results, the larger the load factor the more difficult. Usually the maximum load factor of the reflow furnace range of 0.5 ~ 0.9, depending on the product (component soldering density, different substrates) and reflow furnace of different models to decide. Practical experience is important to get good soldering results and repeatability.
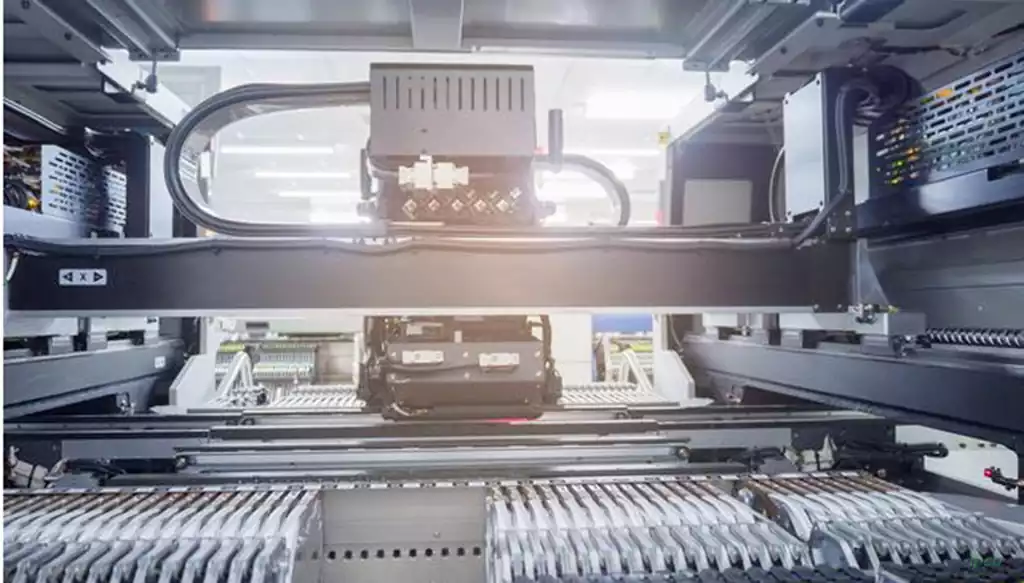
Advantages of reflow soldering:
(1) Suitable for SMD assembly
(2) Trusted by most manufacturers
(3) Does not require extensive monitoring
(4) Less thermal shock
(5)Limited soldering options
(6) Low-waste process that can be applied to specific portions of a printed circuit board
Reflow soldering also has some disadvantages:
- High equipment costs: reflow soldering machine is a high-tech welding equipment, its design and manufacture requires a high degree of technical input, so its equipment costs are relatively high.
- High requirements for operators: reflow soldering requires operators to have professional skills and knowledge, to be able to operate the equipment correctly to ensure the quality and efficiency of welding.
- High requirements for components: reflow soldering requires components with good placement accuracy and stability, for some components that are not adapted to this process need special treatment or replacement.
- High environmental requirements: reflow soldering needs to be carried out in a relatively clean environment to avoid dust and pollutants on the impact of welding quality. At the same time, the reflow soldering process will produce harmful gases and fumes, the need for appropriate environmental protection.
PCB Reflow soldering is a high-efficiency, high-precision soldering technology for mass production and high-quality requirements of the electronics manufacturing field. However, its limitations need to be noted in practical application, and appropriate measures need to be taken to ensure the quality and efficiency of welding.