Copper Through Hole Filling (THF) technology is a major technological breakthrough that addresses the challenges of high-frequency thermal management and signal integrity while improving wiring density and interconnect reliability.Comparing THF and Conductive Paste Fill Through-Hole process, Conductive Paste Fill Through-Hole process involves multiple steps that are difficult to control, high production cost, and the fill itself is unreliable and susceptible to thermal failures (e.g., outgassing) during operation; THF, as a simple, single-step plating process, is filled with copper, which has unrivaled thermal performance compared to other processes.
Plated Through Holes (PTH) are signal-carrying conductive vias that create interconnections between different layers of a circuit board and are used to hold components in place during PCB assembly. Component Mounting Holes Non-Plated Holes INPTH] are non-conductive as NPTH. these holes do not have a tolerance grade because if the hole size is large or too large, the component will not fit.
Through Hole Filling Procedure
Sometimes it is necessary to fill PCB vias,for example to reduce the risk of trapping air or to increase conductivity.Some common methods of filling through holes include:
- Through Tenting
Through-hole tenting creates a soldermask layer over the PCB board through-hole instead of filling the hole with material.This can be a quick, easy and cost-effective alternative to covering the vias, but tented vias may re-open over time. - Through Plugging
The through-hole plugging process fills the hole with a non-conductive material and seals it with a mask.Through-hole plugging also covers the ring and does not produce a smooth, glossy surface. - Through-Fill
Through-hole filling uses resin to create a permanently filled hole. Through-hole filling is a common type of through-hole filling in which the manufacturer fills the through-hole with a conductive material, plates the surface with copper, and then trims the surface. This process allows signals to be routed to other areas of the PCB.
Advantages of plated hole filling:
(1) conducive to the design of stacked holes (Stacked) and holes on the plate (Via.on.Pad), improving the density of the carrier board, more I / O feet of the package loaded board can be applied;
(2) Improve electrical performance, help high frequency design, improve connection reliability, increase operating frequency and avoid electromagnetic interference;
(3) Helps dissipate heat;
(4) Plugging holes and electrical interconnections are completed in one step, avoiding defects caused by using resin and conductive adhesive to fill holes, as well as avoiding CTE inconsistencies caused by filling holes with other materials;;
(5) Blind holes are filled with electroplated copper to avoid surface depression, which is conducive to the design and production of finer lines; the holes are filled with copper columns after electroplating and the conductivity is better than that of conductive resins/adhesives, which improves the heat dissipation performance of the board.
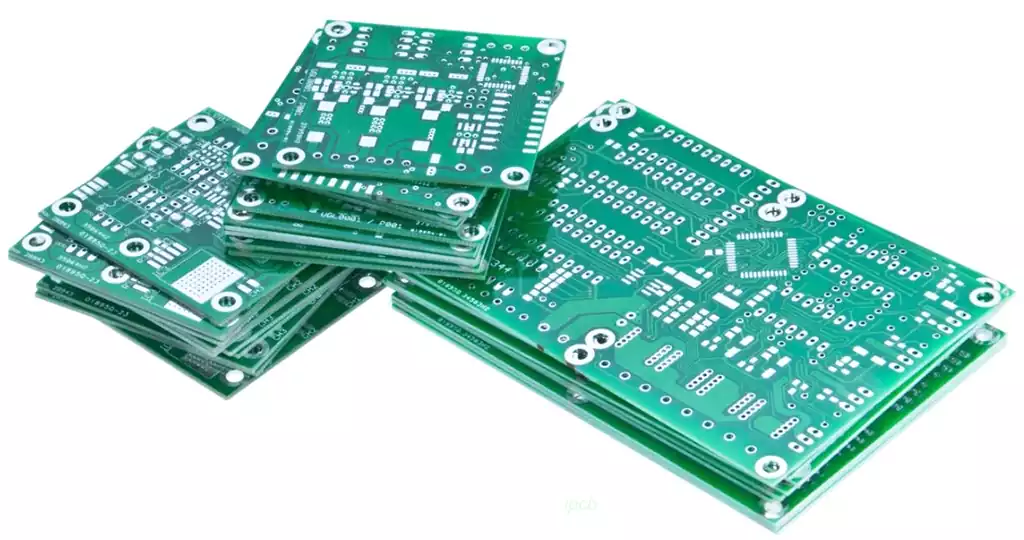
Chemical influences
- Inorganic chemicals
Inorganic chemical constituents include copper (Cu:) ions, sulfuric acid, and chlorides.
(1) Copper sulfate. Copper sulfate is the main source of copper ions in the plating solution. The concentration of copper ions in the plating solution is maintained constant by the Coulombic equilibrium between the cathode and anode. Usually the anode material and the plating material are the same, where copper is both the anode and the ion source. Of course, the anode can also be used as insoluble anode, Cu2+ by way of solubilization outside the tank, such as the use of pure copper horn, CuO powder, CuCO and so on. However, it should be noted that the use of outside the tank to add the way, it is very easy to mix into the air bubbles, in the low-current region so that the Cu2 is in the critical state of supersaturation, not easy to precipitate. It is worth noting that increasing the concentration of copper ions has a negative impact on the through-hole dispersion ability.
(2) Sulfuric acid. Sulfuric acid is used to enhance the conductivity of the plating solution, increasing the concentration of sulfuric acid can reduce the resistance of the bath and improve the efficiency of plating. However, if the concentration of sulfuric acid is increased during hole-filling plating, it will affect the replenishment of copper ions in the hole-filling process, which will result in poor hole-filling. Generally, low sulfuric acid concentration system is used in hole filling plating in order to obtain better hole filling effect.
(3) Acid-copper ratio. Conventional high acid low copper (C +: C: + = 8-13) system is suitable for through-hole plating, plating hole filling should use low acid high copper (C +: Cz = 3-10) plating liquid system. This is because in order to obtain a good hole filling effect, the plating rate in the micro-conductor through-hole should be greater than the plating rate on the surface of the substrate, in which case, compared with the traditional plating solution for plating through-holes, the solution formulation is changed from high acid low copper to low acid high copper to ensure that the supply of copper ions in the depression is worry-free.
(4) Chloride ion. The role of chloride ions is mainly to allow copper ions and copper metal to form a stable conversion of the electron transfer bridge between the double electric layer. In the electroplating process, chloride ions in the anode can help uniformly dissolve the corrosion of phosphorus copper balls, the anode surface to form a layer of uniform anodic film. At the cathode, the chloride ion works with the inhibitor to stabilize the deposition of copper ions, reduce polarization, and make the plating layer fine.
In addition, the conventional chlorine ion analysis is carried out in the UV-visible spectrophotometer, but due to the electroplating hole-filling plating solution on the more stringent requirements of the concentration of chlorine ions, while the copper sulfate plating solution is blue, the spectrophotometer has a very strong impact on the measurements, so we should consider the use of automatic potentiometric titration analysis.
- Organic additives
The use of organic additives can make the plating of copper grain refinement, improve the dispersion ability, so that the plating of bright, flat. Acid copper plating solution additives are mainly three types: carrier (Carrier), leveling agent (Leveler) and brightening agent (Brightener).
(1) Carrier. Carrier is a polymer polyalcohol compound. Carrier by the cathode surface adsorption, and chloride ions together to inhibit the rate of plating, so that the difference between the high and low current areas to reduce (that is, increase the polarization resistance), so that the electroplating of copper can be uniformly sustained deposition. Inhibitors also act as a wetting agent, reducing the surface tension at the interface (lowering the contact angle), making it easier for the plating solution to enter the holes and increasing the mass transfer effect. In hole-filling plating, the inhibitor also allows for uniform deposition of the copper layer.
(2) Leveling agent. Leveling agent is usually nitrogen-containing organic matter, the main function is adsorbed in the high current density area (raised area or corner), so that the plating speed there is slowed down, but does not affect the low current density area (recessed area) of the plating, thus leveling the surface, is the plating of the necessary additives. Generally, the plating of hole filling using high copper and low acid system will make the plating layer rough, studies have shown that the addition of leveling agent can effectively improve the problem of poor plating.
(3) Brightener. Brightening agent is usually sufficient sulfur-containing organic substances, the main role in electroplating is to help accelerate the reduction of copper ions in the cathode, while forming new copper plating nuclei (reduce the surface diffusion deposition energy), so that the structure of the copper layer becomes more detailed. Brightener in the hole filling plating another role is, if the hole has more brightener distribution ratio, can help the blind hole hole plating copper deposited quickly. For laser blind hole filling plating, all three additives, and the amount of leveling agent should also be appropriately increased, so that in the higher current area on the plate surface, the formation of the leveling agent and Cuz competition to prevent the surface of the copper long fast and thick. Relatively speaking, the depressions in the micro-conducting holes where the brightener is distributed more have a chance to be plated faster, and this concept and practice is quite similar to the Demascene CopperPlating for IC copper plating process.