PTFE plate, i.e. polytetrafluoroethylene plate, is a polymer material made of polymerized tetrafluoroethylene monomer. Its unique molecular structure makes it a material with excellent corrosion resistance, high and low temperature resistance, and non-adhesive properties, often referred to as the “king of plastics”.PTFE plate can be made through a variety of processing methods, including molding, extrusion and turning, etc. One of the most important features of PTFE plate is its excellent non-adhesive properties.
One of the best features of PTFE plate is its excellent non-stick properties. Almost any substance is difficult to bond to PTFE-coated films, and even thin films exhibit good non-adhesive properties. This makes PTFE sheet ideal for a variety of industrial applications, such as its widespread use in non-stick pans and other equipment requiring non-stick coatings.
Excellent heat and low temperature resistance. It can withstand temperatures up to 300°C for a short period of time and can be used continuously in the range of 240°C to 260°C. PTFE also performs well in very low ambient temperatures, retaining its physical properties at temperatures down to -196°C. It has a very good chemical stability and is suitable for a wide range of industrial applications.
PTFE plate is amazingly stable chemically and is virtually impervious to strong acids, oxidizing agents, and a variety of organic solvents. However, it is relatively resistant to certain fluorides and alkaline metallic fluids. This resistance makes PTFE an important material in the chemical, petroleum and food industries.
It has excellent mechanical properties,including a low coefficient of friction and good wear resistance.Under specific loading conditions,PTFE exhibits the dual advantages of non-adhesion and abrasion resistance,while its tensile strength can reach 21-28 MPa and its flexural strength is 11-14 MPa.This means that PTFE sheets are still able to work stably in high loading and friction environments.
It also excels in electrical insulation properties.It can withstand voltages of up to 1500 volts and its electrical properties are not affected by temperature or frequency.PTFE’s low dielectric constant and high dielectric strength make it the insulating material of choice in the electronics and electrical industries.
The self-lubricating properties of PTFE plate enables them to effectively reduce friction losses when in contact with sliding parts. This characteristic is particularly suitable for mechanical equipment parts applications, such as bearings, guide rails, etc., which can improve the working efficiency and extend the service life of the equipment.
Because of its unique characteristics, PTFE sheet is widely used in many industries.
In the chemical industry, due to the excellent corrosion resistance of PTFE sheet, able to resist the erosion of acids, alkalis and salts and other chemicals, so it is often used to make pipelines, valves and pumps lining to ensure the long-term stable operation of chemical equipment.
In the electronics industry, PTFE plate because of its excellent electrical insulation properties and high temperature resistance,widely used in high-frequency cable insulation, printed circuit boards and electronic components to support the base and so on.
In the food processing field, PTFE sheet’s excellent non-stick properties and chemical inertness make it an ideal material for food processing equipment, such as for the manufacture of conveyor belts, storage tanks and cooking surfaces to prevent food contamination.
In the medical device industry, PTFE sheets are often used for surgical instruments,vascular catheters and artificial organs due to their good biocompatibility and resistance to high temperature sterilization.
In addition, PTFE sheets are used in hydraulic and pneumatic systems, environmental protection facilities,and many other fields, showing its wide adaptability under many complex conditions.
The production process for PTFE sheets involves several key steps to ensure the quality and performance of the final product.
First, the raw material preparation stage, in which high-quality PTFE resins and appropriate fillers are selected,ensures the quality and stability of the raw materials through a strict quality management system.
Next, a mixing process is performed to thoroughly blend the PTFE resin with the fillers, which are then molded through a molding process.Usually the process is carried out under specific temperature and pressure conditions to achieve the best molding results.
After molding, the PTFE sheet undergoes a sintering process,where the material is heated to achieve higher density and purity,and subsequently cooled to maintain its shape. The production process also includes quality checks for appearance and performance.
Finally, post-processing steps may include surface treatments to improve the properties of the PTFE sheet,such as enhancing its abrasion resistance and adhesion. After this series of steps, the final product is packaged and distributed.
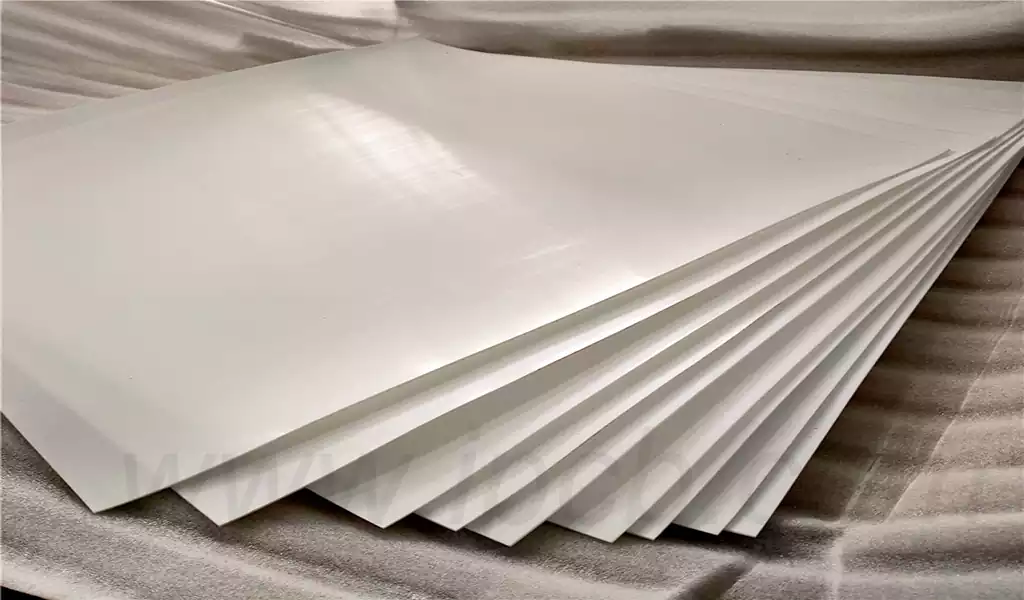
How to choose the right thickness of PTFE sheet for different applications
- Understanding the properties of PTFE sheet
The first step in choosing the right thickness of PTFE sheet is to understand the unique properties of PTFE material.PTFE sheet not only has high temperature resistance,corrosion resistance and excellent electrical insulation,but also shows extremely low coefficient of friction and self-lubricating properties,these properties make PTFE widely used in a variety of applications. - Consider the application environment
The application environment will largely determine the required PTFE sheet thickness.In high temperature and high pressure environments,thicker PTFE sheets provide better stability and reliability. Also, in certain specific chemical environments,thicker sheets can resist corrosion. - For the mechanical properties of the demand
In applications that require high mechanical loads,it is wise to choose thicker PTFE sheets. Thicker plates exhibit better wear and impact resistance in many dynamic applications. This is because their thickness is directly related to the overall strength and durability of the material. - Custom vs. Standard Thickness Options
For special needs, the thickness of PTFE sheet can be customized for specific applications. Standard thicknesses usually range from 1mm to 60mm, allowing users to choose the specification that suits their needs. If the needs are more complex, customized processing is also a viable option. - Cost and material utilization
Finally,the choice of thickness also needs to take into account the cost and efficiency of material utilization.
Thicker sheets tend to have higher costs, so a reasonable assessment of the cost-effectiveness of each thickness in a particular application will help save money.It should also be noted that different thicknesses of PTFE sheet may require different processes for machining and cutting, which also introduces variations in costing. - Examples of applications in practice
Different applications have specific requirements for the thickness of PTFE sheets.For example,a thinner PTFE sheet may be sufficient for food processing or medical applications,whereas a thicker PTFE sheet may be more appropriate for applications such as the chemical,electronic and mechanical industries. Understanding industry standards and specific applications is essential for professional advice and data analysis to ensure that the right thickness is selected for functionality and safety.
PTFE plate has become an important material for industry due to its excellent properties and wide range of applications.In the future,applications for this board will continue to expand as the demand for high performance materials increases. Proper selection of the thickness and specifications of PTFE boards will help to fully utilize their advantages to meet the needs of different fields.