Rogers PCB is a high performance circuit board material used in a wide range of high frequency and high speed electronic devices. Its unique physical and electrical properties have made Rogers PCBs popular in modern communications, automotive electronics, aerospace and other critical applications.
The Rogers PCB manufacturing process represents the best technology in the industry. They utilize advanced process technology to ensure high-precision line fabrication and layer-to-layer alignment, resulting in printed circuit boards with excellent performance and high precision. At the same time, a strict quality inspection and control system ensures the reliability and consistency of each board.
Rogers Printed Circuit Board Manufacturing Process:
Substrate Treatment:The substrate is the foundation of the printed circuit board and plays a vital role in its electrical properties and mechanical strength. Rogers PCBs are made from high-quality substrates such as polyimide (PI) and polyester (PET),which have excellent heat resistance, insulation, and stability. During the manufacturing process,the substrates are first surface treated to improve their adhesion to the conductive material.
Line design: According to the customer’s needs and design requirements,the line design is carried out using professional software. The design process needs to consider the electrical properties of the circuit board,wiring density,signal transmission requirements, and other factors to ensure the reliability and performance of the final product.
Line transfer:The designed circuit diagram is transferred to the substrate through photolithography.In this process,a photosensitive adhesive is applied to the substrate, and after exposure and development, the circuit diagram is transferred to the substrate.
Hole Processing:The desired holes are processed in the substrate.These holes are used to connect the conductive pathways between the line layers. There are various hole processing techniques, including drilling and EDM.Rogers Printed Circuit Boards utilize advanced drilling techniques to ensure the positional accuracy and consistency of the holes.
Metallization: Through processes such as chemical plating or electroplating, a conductive metal layer is formed inside the hole and on the surface of the circuit. This step is the key link to realize the circuit board conduction, which needs to ensure the adhesion between the metal layer and the substrate and conductive materials.
Soldermask treatment: To protect the circuit from environmental and external factors,a soldermask is applied to the non-conductive areas of the printed circuit board. Rogers printed circuit boards are made of high-quality solder mask material,which ensures good protection and reliable insulating properties.
Surface treatment:The surface of the printed circuit boards is treated according to customer needs and subsequent assembly requirements. Common surface treatments include gold plating, tin spraying, chemical nickel gold, etc.to improve its conductivity and corrosion resistance.
Quality Inspection: During the manufacturing process, strict quality inspection and control is carried out at each step to ensure product reliability and consistency. Quality inspection includes appearance inspection, size measurement, electrical performance test, and other aspects.
Packaging and Transportation: Finally, the finished products are properly packaged and protected to ensure that they are not damaged during transportation and storage. Special packaging measures such as moisture-proof and shock-proof can also be provided according to customer requirements.
The material requirements of Rogers printed circuit boards are mainly reflected in the following aspects:
Dielectric properties: Rogers printed circuit boards are made of special amide resin materials that require stable dielectric constants, loss factors, leakage currents, and other parameters to meet the demands of high-precision, high-speed circuit design.
Thermal Stability: Low Coefficient of Thermal Expansion (CTE) is an important characteristic of Rogers PCBs, which can maintain stability in high temperature and high humidity environments to avoid circuit failure problems caused by temperature changes.
Mechanical Strength: The material is tough and can withstand large mechanical loads to ensure reliable circuit operation.
Cleanliness and adhesion properties: To ensure the conductivity and reliability of the circuit, the surface treatment of Rogers printed circuit boards requires high cleanliness and good adhesion properties.
Environmentally friendly: When selecting materials, Rogers also focuses on environmental considerations, using environmentally friendly process technologies and materials to minimize waste emissions and negative impacts on the environment during the production process.
Rogers pcb is used in a wide range of applications:
Communication field: widely used in 5G communication base stations, RF module antennas, and other equipment, providing stable and reliable signal transmission performance.
Military field: In the military field, Rogers high-frequency circuit board materials are used in high-end equipment such as radar and satellite navigation.
Medical Equipment: In the medical equipment field, used to manufacture high-precision medical instruments and diagnostic equipment.
Automotive Electronics: In the field of automotive electronics, it is used to realize the intelligence and safety of automobiles.
Aerospace: In the aerospace industry, it is used to manufacture key components such as precision navigation systems.
Microwave Communications: widely used in microwave communications, military radar, and other high-frequency PCBs and high-reliability fields.
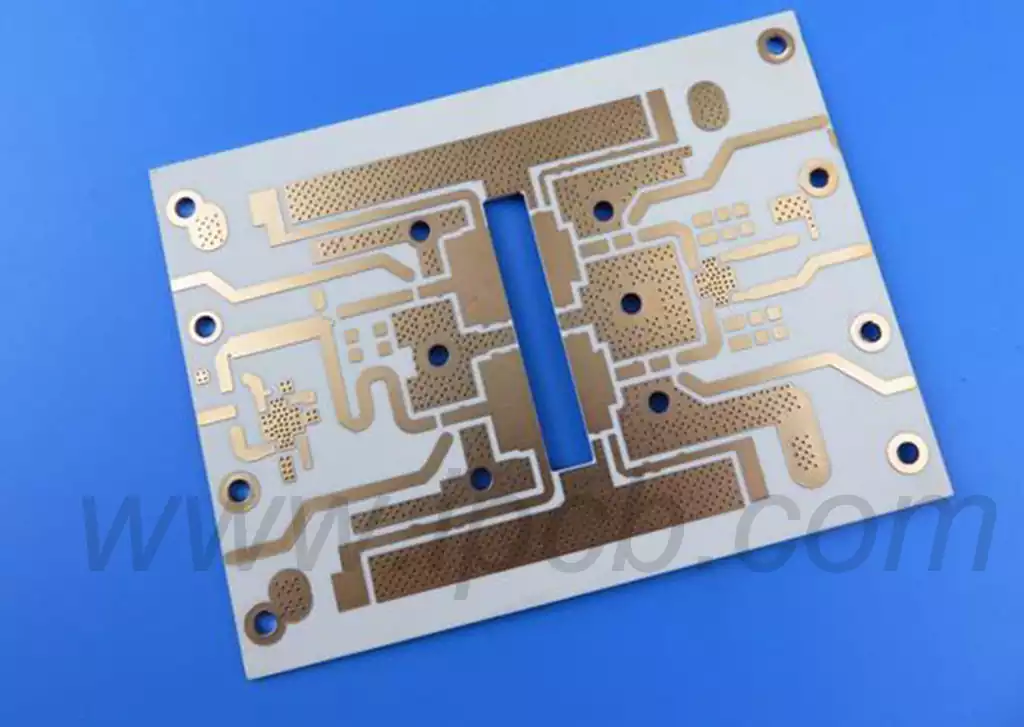
Factors to consider when choosing Rogers PCBs:
- Design Requirements
Selecting a Rogers PCB begins with finding a balance between design requirements, including electrical and structural reliability. This is because high frequency circuits place higher demands on PCBs than conventional circuits, and need to meet specific electrical performance criteria and mechanical strength requirements. - High Frequency Performance
Rogers PCBs are favored for their excellent high-frequency performance, especially critical in applications with frequencies over 500MHz. High-frequency PCBs have low dielectric constants and low dielectric losses, which allows for more efficient signal transmission and effectively reduces signal loss. - Material Characterization
Rogers material properties are very important, such as its corrosion resistance, thermal conductivity and thermal stability. These characteristics not only affect the performance of the board, but also directly related to its reliability in a variety of operating environments. - Manufacturing feasibility
In the design phase, you need to consider the manufacturability of the material to ensure that the selected material can be produced on schedule and meet the design requirements. Quality manufacturability can shorten the design cycle and reduce potential production risks. - Cost
Cost is a factor that should not be overlooked when selecting Rogers PCBs. Although Rogers PCBs are typically more expensive, the high frequency performance and special material properties they offer often make up for the cost in the long run. Therefore, the choice needs to be weighed against the specific application requirements and budget.
Rogers PCBs are significantly more costly compared to conventional PCBs such as FR-4 material:
1.Cost Comparison
Rogers PCBs typically cost more than FR-4 materials due to the superior performance and application quality of Rogers materials.Prices can range from $2 to $10 per square foot or more,while FR-4 is generally less expensive.Specific costs vary depending on the type of material and manufacturing requirements.
2.Cost Influencing Factors
The main factors affecting the cost of Rogers PCB include the type of material, the complexity of the circuit design, and the manufacturing process. Although Rogers PCBs have a higher initial investment,their advantages in high frequency, low loss, and excellent stability tend to make up for the cost in the long run. In areas with stringent requirements for high signal integrity and thermal management, the investment in Rogers PCBs is often considered the right choice.
3.Cost Optimization Recommendations
In order to reduce the manufacturing cost of Rogers PCBs, designers can consider various strategies,such as mixing Rogers materials with FR-4 materials, or choosing lower cost Rogers materials such as RO3003 or TC350 to meet certain performance requirements. In addition,optimizing the number of layers and layout design is also an effective way to control costs.
4.Selection of Industry Applications
Despite the higher cost of Rogers PCB, its superiority in high performance applications such as aerospace, automotive radar, satellite communications, etc. has resulted in more industries choosing to use Rogers materials. In these areas of high frequency and high reliability requirements, the performance of Rogers PCBs is often irreplaceable by other materials.
Rogers PCB Manufacturing leads the Printed Circuit Board industry with superior process technology, high-quality material selection, a wide range of applications, customized services, and environmentally friendly production methods.