Semiconductor test boards, or ATE (Automatic Test Equipment) as we often call them, are an essential part of the semiconductor industry. Semiconductor test boards are specialised circuit boards used to evaluate, verify and test the performance of semiconductor devices. These test boards are precision designed to accommodate different types of semiconductor devices and to accurately test various parameters of semiconductors through specific circuit connections.
The field of ATE (Automatic Test Equipment) is much more complex than we realise, with a variety of ‘morphological branches’, each with unique and powerful functions.
Probe card (Probe Card): It is like the ATE family in the ‘sleuth’, specialising in the uncut, packaged wafers on the ‘search for the truth’ task. With the help of a thin probe, it can be on the wafer of each chip to implement the electrical test, as if for the chip to carry out a comprehensive and detailed ‘health check’, from which to select those with excellent performance of the chip, sent to the subsequent packaging process, and ultimately become the model we see every day.
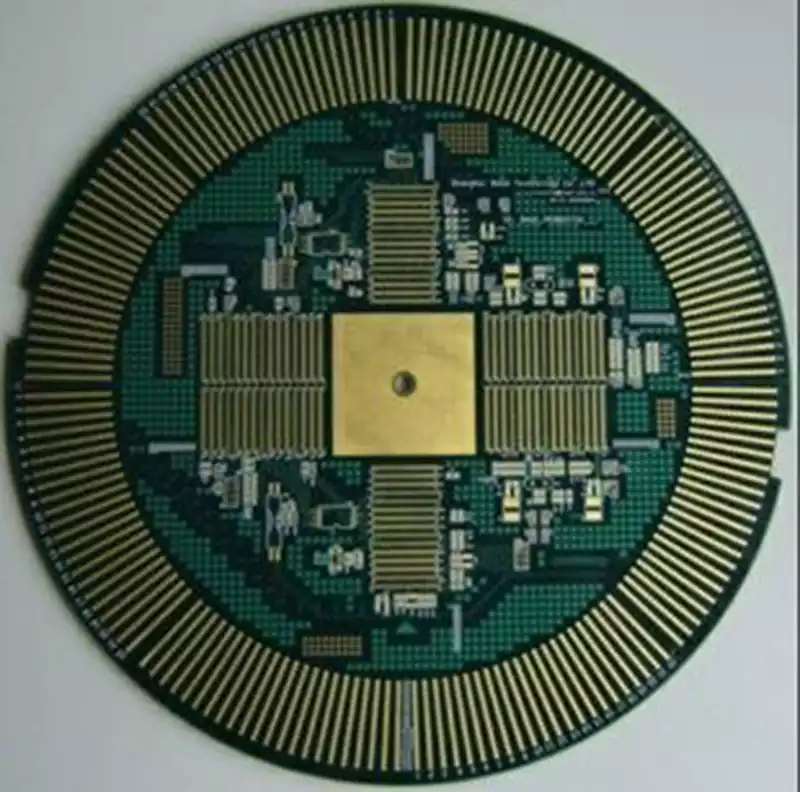
Load board (Load Board): Even if the chip has completed the package, it can not be directly put into use, but also need to accept the strict inspection of the load board. The load board is like a ‘senior coach’ in the ATE system, carrying out a full range of functional and performance tests on the packaged chips to ensure that they can show excellent performance in a variety of complex environments. Especially for those high-speed interface chips, the impedance matching requirements of the load board are extremely strict, and any slight deviation may affect the performance of the chip.
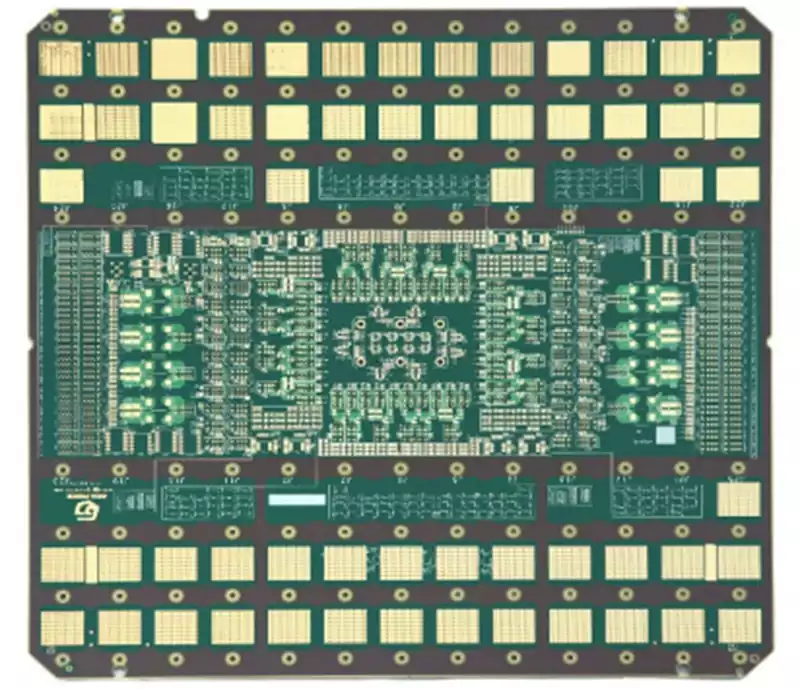
Aging test board (Burn-in Board, referred to as BIB): the name sounds like a ‘tough’, right? Aging test board is just like the ‘tough tutor’ in ATE, specially arranged for the chip a ‘limit training’ – including thermal cycling, accelerated switching cycle and other high-intensity test, the purpose of which is to find out those potential Is to find out those potential ‘weak links’, that is, those in the early use of the chip may fail. As a result, the products we buy will have greater durability.
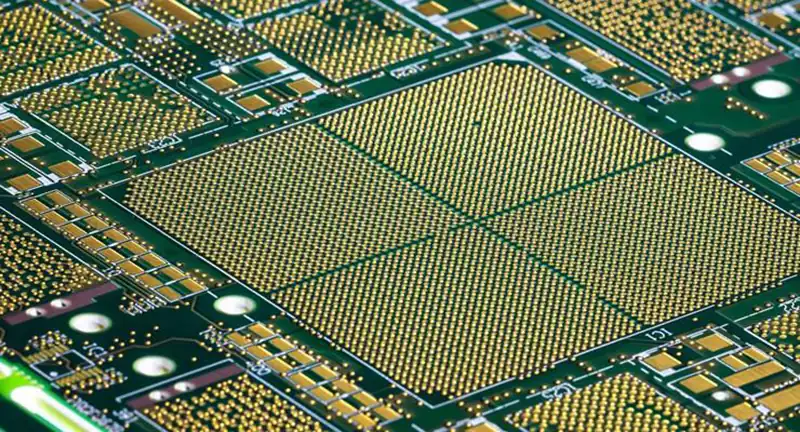
With integrated circuits (ICs) towards miniaturisation, complexity and direction, the technical content of the ATE test board has also shown a rapid increase in the trend. Load board, for example, the number of layers are usually more than 30 layers, BGA (Ball Grid Array) pitch is as small as a hair, drilling accuracy, copper plating process, resin plug hole technology, etc., each of which is known as a highly sophisticated technology. The pitch of BGA on the probe card is also shrinking, and the pitch of high-end products can even be as fine as 40 – 55 microns, which is undoubtedly a micron-level ‘precision embroidery’ process.
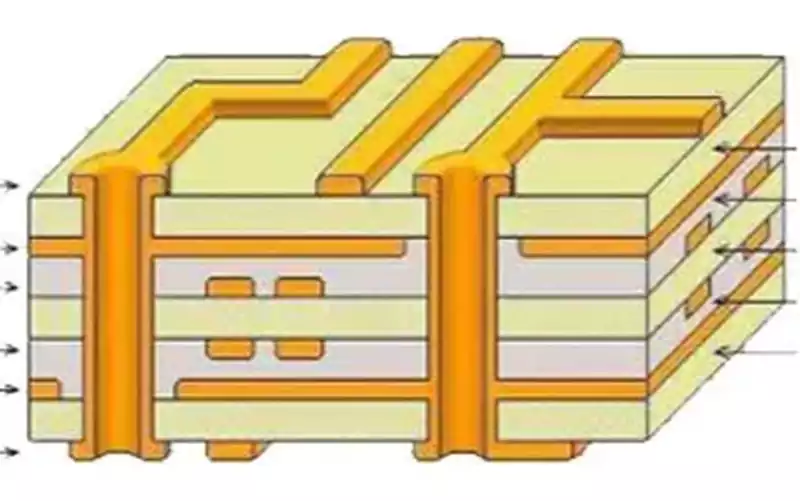
Manufacturing these high-precision ATE boards is no easy task. To flatness, for example, high-end ATE board on the flatness of the requirements are extremely stringent, the warpage must be strictly controlled in the range of 0.1% – 0.2%, pad height difference is more accurate to the micron level. It is important to know that the unit to be tested (DUT) is connected to the pad through the probe, even a tiny dent or scratch on the pad may interfere with the test results. Therefore, the manufacturing process of ATE boards is undoubtedly a fierce battle with errors, and every aspect must be perfected.
Role of Automatic Test Equipment
Ensuring Quality Control in the Production Process
Automatic Test Equipment is an important tool for verifying the performance and reliability of semiconductor devices. During the production process, the test boards can be used to test semiconductor chips for various indicators, such as current, voltage, power, etc., to ensure that the product meets the design requirements. This means of quality control helps to identify problems in production in a timely manner, improve product yields and reduce production costs.
Ensure stable performance of semiconductor equipment
In addition to its application in the production process, Automatic Test Equipment is also widely used in the R&D and maintenance process of semiconductor equipment. Through the test board, the actual working environment can be simulated to test and evaluate the various performance indicators of the equipment. This helps to identify potential problems before the equipment is put on the market, ensuring stable and reliable performance. At the same time, in the process of equipment maintenance, the test board can also help engineers accurately locate the problem and improve maintenance efficiency.
Driving innovation in semiconductor technology
Automatic Test Equipment is not only an essential tool for production and maintenance, but also a key factor in driving innovation in semiconductor technology. As semiconductor technology continues to advance, test boards need to be continually updated to meet new test requirements. This prompts test board manufacturers to continue to increase R & D investment, to promote the innovative development of test technology, so as to provide strong support for the progress of the entire semiconductor industry.