Alumina ceramic substrates consist mainly of a white amorphous powder commonly known as aluminium oxide, or simply Al2O3. It has a density of between 3.9 and 4.0 g/cm3, a melting point of up to 2,050°C, and a boiling point of up to 2,980°C. It is also used in the manufacture of alumina ceramic substrates. Aluminium oxide is insoluble in water and exhibits excellent properties in numerous applications.
Common alumina ceramic substrates are classified according to their Al2O3 content, which includes several types such as 99%, 95%, 90%, 96%, 85% and sometimes 80% or 75% alumina variants. When we say 99% alumina, we mean that it is 99.5% or even 99.8% pure. This aluminium oxide appears white or ivory in colour and is characterised by very high wear resistance, excellent resistance to acid and alkali corrosion, as well as excellent performance at temperatures between 1600 and 1700 degrees Celsius. In addition, it exhibits good chemical stability, high electrical insulation, strong adsorption capacity, and excellent wear resistance, and is therefore used in a wide range of applications such as lamps, electronics, sandblasting nozzles, automotive parts, and wear-resistant components.
In contrast, 96% alumina is slightly less pure than 99% alumina, but it still offers good thermal conductivity and insulating properties while maintaining a high level of economic efficiency.
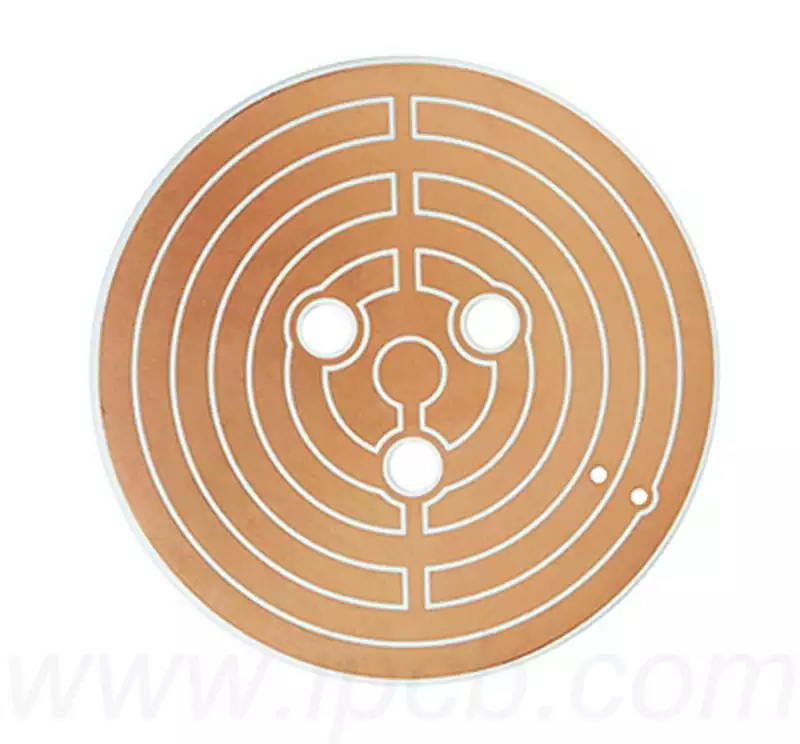
Alumina is chosen for the substrate because it offers good thermal conductivity, high electrical resistance, high hardness, high electrical insulation and high corrosion resistance, making it one of the most commonly used ceramic PCBs on the market. For 96% and 99% concentration, how to choose?
1.96% alumina concentration products
Cost Advantage: Compared to 99% alumina, 96% alumina is more economical in terms of cost, which is ideal for projects with stringent cost requirements.
Consistent performance: 96% alumina provides consistent and economical performance in most electronic components with low to medium power requirements.
Ease of processing: Its processing performance is better than that of 99% alumina, making it easier to cut, drill and fabricate substrates in a variety of shapes.
Applications: Widely used in low power electronic components, sensors, capacitors, micro relays, microwave components and other fields.
2.99% Alumina Concentration Products
High purity characteristics: purity of 99% or above, with higher chemical purity and density, to meet the occasions with extremely high performance requirements.
Excellent performance: with more excellent thermal conductivity, to ensure that the material is uniformly heated, and effectively promote heat dissipation. Suitable for high-power LEDs, high-voltage integrated circuits, high-temperature sensors, high-frequency electronic components and so on.
High mechanical strength: high hardness, high mechanical strength, can withstand large external forces and pressures, to ensure that the material remains stable in complex environments.
Strong corrosion resistance: Because of its high purity, it shows excellent resistance to acid and alkali corrosion, ensuring that the material has a long service life and durability in corrosive environments.
High Precision Characteristics: Demonstrates increased precision and stability in all electrical properties, making it ideal for high-precision electronic applications that require consistent and reliable performance.
99.6% alumina content of alumina ceramics compared to 96% alumina content of alumina ceramics, the preparation of the difficulty is mainly reflected in the following aspects:
Raw material selection: the preparation of high purity 99.6% alumina ceramics need to use high-quality raw materials, these raw materials are more difficult to obtain, the cost is relatively high. At the same time, the purity of raw materials and particle size need to implement more stringent control to ensure the purity of ceramic materials and stable performance.
Process management: the preparation process of high-purity alumina ceramics involves powder preparation, mixing, forming, sintering and other key steps, each step requires precise process control. This requires a higher level of process management to ensure that the quality and performance of the ceramic material meets expectations.
Sintering process challenges: 99.6% alumina ceramics are sintered at higher temperatures than 96% alumina ceramics, making the sintering process more complex. This can easily lead to problems such as uneven sintering and excessive sintering shrinkage, so the control of the sintering process is more stringent and requires a higher level of technology and experience.
Difficulty of forming technology: Due to the high hardness of 99.6% alumina material, the difficulty of its forming increases accordingly. More advanced moulding processes, such as plasma moulding and injection moulding, are required to ensure that the precision and quality of the finished products meet high standards.
96% and 99% alumina ceramic substrates each have their own unique advantages and areas of application. When choosing between them, comprehensive consideration needs to be made based on factors such as the cost budget, performance requirements and processing difficulty of a specific project. The preparation of 99.6% alumina ceramics, on the other hand, faces many challenges, but its excellent performance makes it irreplaceable in high-precision, high-demand electronic applications.