SMT, or Surface Mount Technology, is a technology for mounting electronic components directly onto the surface of a PCB (Printed Circuit Board). Compared with the traditional through-hole insertion technology, SMT has the advantages of high density, high reliability, low cost and so on, so it is widely used in modern electronic products.
SMT process flow
- Design and production of PCB: First, according to the circuit design requirements, the PCB layout is designed using computer-aided design (CAD) software. Then, the PCB board is produced through photolithography and etching and other steps.
- Printing Solder Paste: Solder paste is applied to the pad locations on the PCB. Solder paste is a paste-like substance with viscosity that is used in subsequent steps to connect components to the PCB.
- Automated Assembly: Using automated equipment, surface mount components are removed from the feeder and accurately placed on the pads. These devices include pick and place machines (Pick and Place Machine) and reflow ovens (Reflow Oven), among others.
a. Pick and Place: The Pick and Place Machine selects the component from the component feeder and uses a vacuum nozzle to accurately place it on the pad.
b.Soldering: After the placement is complete, the entire PCB is fed into the reflow oven. The high-temperature oven zone in the reflow oven heats up the solder paste and melts it to connect the components to the pads. The PCB is then cooled down through the cooling zone. - Inspection and Repair: After soldering, the PCB needs to be inspected for quality. These inspections can include visual inspection, X-ray inspection, automated optical inspection etc. If any defects are found, they need to be repaired or reassembled.
- Testing: After assembly, the electronic components on the PCB need to be functionally tested to ensure that they work properly. This can be done by connecting test equipment or using specialized test fixtures.
- Cleaning: After testing is complete, the circuit board may need to be cleaned to remove solder paste residue and other dirt. Cleaning can be done using chemical solvents, ultrasonic cleaners or spray cleaners.
- Final Inspection and Packaging: Finally, the completed PCB is subjected to a final inspection to ensure that it meets quality standards. It is then packaged and labeled for subsequent transportation and use.
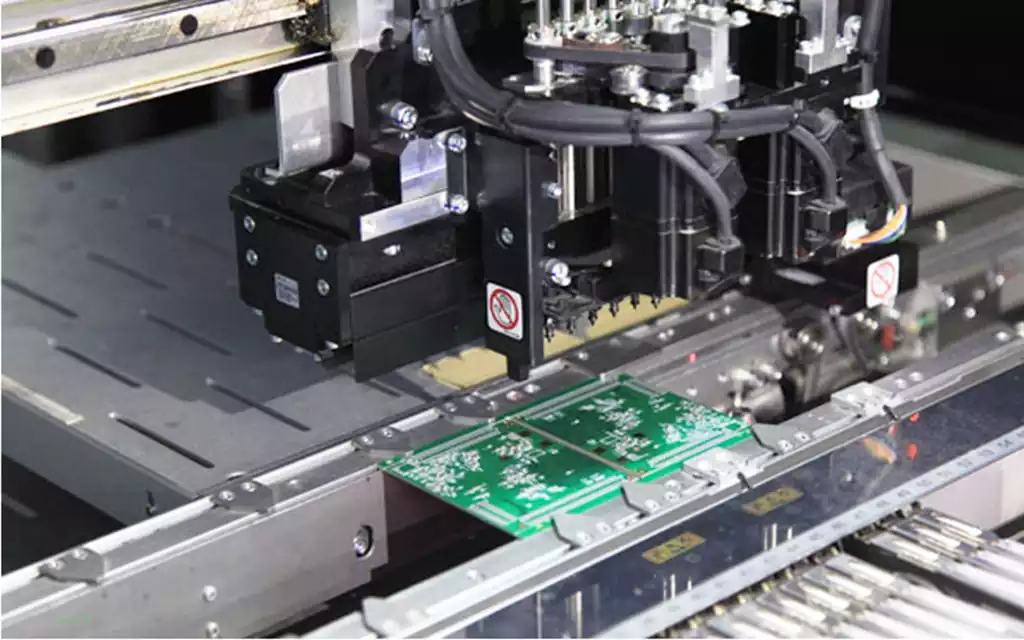
SMT process advantages
(1) high density due to the surface assembly components using no leads or short leads, I/O end face array layout and other packaging technology, the size of the components is greatly reduced, I / O lead-outs greatly increased, so that the assembly density of the PCB substrate has been substantially increased.
(2) High-performance surface assembly components without leads or short-lead characteristics, reducing the parasitic inductance and capacitance of the leads, improving the high-frequency and high-speed performance of the circuit as well as the device’s thermal efficiency.
(3) low cost due to the standardization of surface assembly components package and no-hole mounting characteristics, especially suitable for automated assembly, significantly reducing manufacturing costs.
(4)High reliabilityAutomated production technology ensures reliable connection of each solder joint, thus improving the reliability of electronic products.
SMT technology is applied in different fields:
Communication equipment: SMT technology is widely used in the manufacturing of communication equipment such as base stations, communication modules, routers and switches. Through SMT technology, these devices can achieve higher integration and smaller size, while improving the stability and reliability of the products.
Computer Hardware: SMT technology is also widely used in the manufacturing of computer hardware products such as desktops, laptops and servers. Through precise welding and assembly, the performance and stability of computer hardware has been significantly improved.
Automotive electronics: SMT technology is increasingly widely used in the field of automotive electronics, including automotive control units (ECU), entertainment systems, navigation systems, sensors, and other automotive electronic components manufacturing. SMT technology makes the design of automotive electronics more compact, reliable, and improve the performance and stability of the product.
Medical electronics: SMT technology is also very important in the application of medical electronics, such as medical imaging equipment, pacemakers, blood glucose monitors, respiratory machines and other medical equipment manufacturing. the high precision and reliability of SMT technology ensures the accuracy and stability of medical equipment, contributing to the development of the medical industry.
Industrial automation: SMT technology is also used in the field of industrial automation, including the manufacture of PLCs (programmable logic controllers), industrial controllers, sensors and other industrial automation equipment. These devices require high-precision and high-reliability assembly, and SMT technology can fulfill these requirements.
Aerospace: SMT technology is also widely used in the aerospace industry because aerospace equipment requires high performance and reliability of electronic components, and the high density and high reliability of SMT technology makes it ideal for aerospace equipment manufacturing.