Soldering wetting is the process by which molten solder forms a uniform, smooth, continuous and firmly attached alloy on the surface of the metal to be welded during the welding process.
Surface wetting is the phenomenon whereby the molten solder spreads out and covers the surface of the metal to be welded during the welding process.
Wetting indicates the dissolution and diffusion between the liquid solder and the surface to be soldered, the formation of intermetallic compounds (IMC), which is a sign of a good soft brazing joint.
Principle of surface wetting
- Surface tension of liquid solderLiquid solder has a surface tension that allows it to spontaneously fill tiny gaps on the surface of a substrate or electronic assembly.
When the solder comes into contact with the metal surface, the surface tension encourages the solder to spread out on the metal surface, forming a tight contact interface. - Solderability of metal surfaces
Solderability of the metal surface refers to its ability to be wetted by liquid solder. Oxide, oil and other contaminants on the metal surface will reduce its solderability, resulting in poor soldering. Therefore, before SMT placement processing, the substrate needs to be strictly cleaned and treated to ensure that it has good solderability. - Chemical reaction and diffusion
When liquid solder is in contact with the metal surface, chemical reaction and diffusion process will occur. The metal elements in the solder (e.g. tin, lead) and the atoms on the metal surface undergo intercalation to form an alloy layer. This process requires sufficient heating time and temperature to ensure that the chemical reaction takes place adequately. - Soldering angle and time
Welding angle and time are also important factors affecting surface wetting. Appropriate soldering angle helps liquid solder in the metal surface spread, and enough soldering time to ensure that the chemical reaction and diffusion process is fully carried out.
The principle of SMT SMD surface wetting
The principle of SMT SMD surface wetting is that, in the case of close contact between the liquid solder and the surface of the metal being soldered, there is only enough attraction when in close contact to ensure sufficient adsorption, so that the solder spreads and covers the surface of the metal being soldered to form a good wettability. If the surface to be soldered on any firmly attached contaminants, such as oxide film, will become a metal connection blocking layer, thus preventing wetting.
SMT patch surface wetting phenomenon
No wetting: the surface becomes uncovered again, without any visible interaction with the solder, the soldered surface maintains its original color;
Wetting: the molten solder excluded, the soldered surface still retains a thin layer of solder, proving that intermetallic interaction has occurred;
Partial wetting: some parts of the surface to be welded to show wetting, some parts of the surface to show no wetting;
Weak wetting: the surface was initially wet, but after the solder from part of the surface will be reduced to droplets, and in the weak wetting over the place to leave a thin layer of solder.
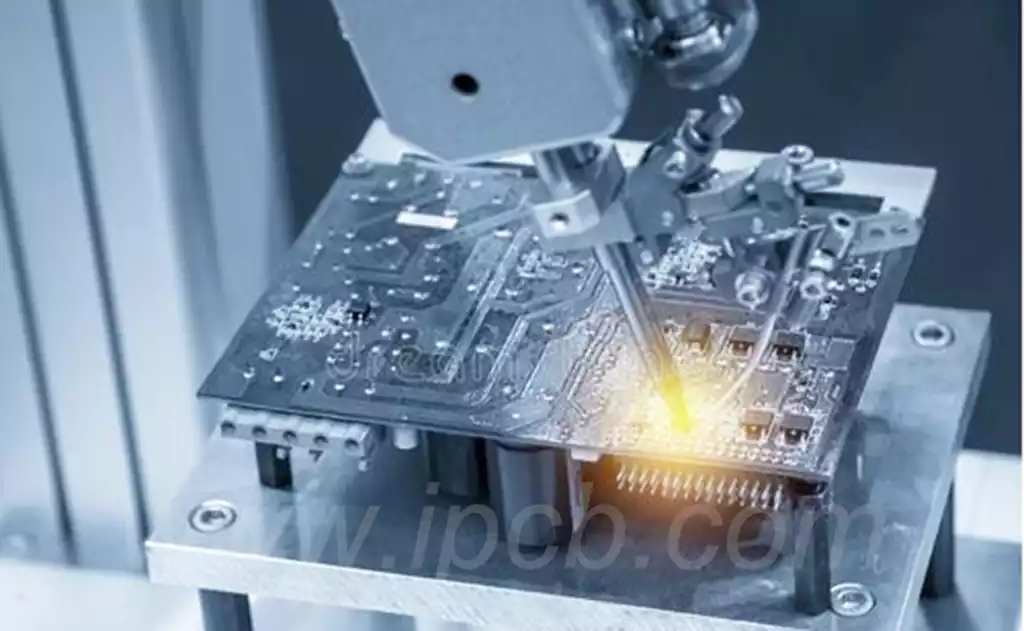
Soldering wetting conditions
① Liquid solder and the base material have a good affinity for each other, can dissolve each other. Liquid solder and the degree of mutual solubility between the base material depends on the type of lattice and atomic radius, so the wetting is inherent in the nature of substances
② liquid solder and the surface of the base material is clean, no oxide layer and pollutants. Clean surface so that the solder and the base material atoms close to, and
Generate gravitational force (wetting force). When there is an oxide layer and other contaminants between the solder and the metal being soldered, it will prevent the metal atoms from approaching freely and cannot produce wetting effect. This is one of the reasons for the formation of false soldering in SMD processing.
Factors affecting surface wetting
Although surface wetting is a spontaneous process, a variety of factors may affect the effectiveness of surface wetting in SMT SMD processing. The following are some of the major influencing factors:
Surface Energy: The energy of a solid surface has a significant impact on the ability of a liquid to wet on it. Solid surfaces with high surface energy are more likely to be wetted by liquids.
Temperature: Temperature affects the viscosity and surface tension of a liquid, which in turn affects the ability of the liquid to wet on a solid surface. Appropriate increase in temperature helps to improve the surface wetting effect.
Pressure: In SMT SMD processing, applying the appropriate pressure can push the solder paste or solder spread on the soldering part to promote surface wetting.
Liquid properties: the nature of the solder paste or solder (such as viscosity, surface tension, etc.) will also affect the surface wetting effect. Selecting the right paste or solder is critical to achieving good surface wetting.
In order to achieve good surface wetting, SMT SMD process need to pay attention to the following points:
Select the appropriate solder paste or solder to ensure that its properties match the PCB board and the soldered parts of the electronic components to achieve good wetting.
Control the appropriate temperature so that the solder paste or solder can be fully spread on the soldered parts, while avoiding too high a temperature resulting in poor soldering.
Apply appropriate pressure to push the solder paste or solder to spread evenly on the soldered parts to ensure good surface wetting effect.
Through the above measures, you can effectively improve the surface wetting effect of SMT SMD processing, thereby ensuring the quality of welding and product reliability. In the actual production process, processors need to flexibly adjust the various parameters according to the specific circumstances to achieve the best surface wetting effect.
Soldering wetting is a key link in the SMT chip processing, and its effect directly affects the quality of soldering and product reliability. Through reasonable process control and material selection, can significantly improve the wetting effect, to ensure the firmness and stability of welding.