Solder balls are small spheres made of pure tin or tin alloy. It has good corrosion resistance and electrical conductivity, so they have a wide range of applications in electronic component manufacturing, soldering and energy storage.
Classification of tin balls
1.SnPb C4 Bump (SnPb C4 tin ball)
Traditional solder balls made of tin-lead (SnPb) alloy with a diameter of 75 – 200 µm. SnPb alloys offer good reliability, but are gradually being replaced by lead-free materials due to the harmful properties of lead.
- Pb-Free C4 Bump (Lead-Free C4 Tin Balls)
Pb-Free C4 Bump, usually made of tin-silver (SnAg) alloys with a diameter of 75 – 150 µm, meets environmental requirements and replaces leaded alloys. The mechanical and electrical properties of lead-free solder balls are close to those of leaded alloys. - Cu Pillar + Pb-free Cap
Cu Pillar + Pb-free Cap (Cu Pillar) with a 50 – 100 µm diameter SnAg cap at the bottom. The Cu Pillar reduces the size of the solder ball and improves the heat dissipation. Suitable for higher density IC packages. - Cu μ-Pillar + Pb-free Cap (Micro Copper Pillar + Pb-free Cap)
Cu μ-Pillar + Pb-free Cap (SnAg) with a diameter of 10 – 30 µm further reduces the interconnect size and is suitable for very high density packages such as 3D IC packaging technology.
The material properties of solder balling include the following:
- Corrosion resistance: Tin balls have good corrosion resistance and are not susceptible to rust or oxidation in humid environments.
- conductivity: tin ball has good conductivity, can be used as electronic components of the contact material.
- plasticity: tin balls have good plasticity, can be made into different shapes and sizes of products, such as tin wire, solder paste, etc..
- Stability: Tin balls are chemically very stable and can maintain their material properties at high or low temperatures.
Preparation methods
There are two main methods for the preparation of solder balls: one is through the melting method and the other is through the powder metallurgy method.
- Melting method: In this method, tin or tin alloy is heated to the melting point, and then small spheres are formed by electrolysis, spinning or ejection.
- Powder metallurgy method: This method is to process tin powder or tin alloy powder into small spheres, the specific method includes powder pressing, spheronization, sintering and other processes.
The role of the tin ball: the main three functions: electrical connection, mechanical support, thermal conduction.
The significance of solder balling for chip packaging?
With the development of chip packaging forms, chip packaging tends to small size, but also in the direction of 2.5D, 3D packaging and other three-dimensional system-level SIP packaging development, as a chip package to assume the role of the electrical signal connection of the core components and direct materials, tin ball not only for high-end chip manufacturing and packaging to provide a better solution, and its quality also determines the quality of the chip package.
The process flow of solder ball soldering usually includes the following steps:
Material preparation: select suitable tin balls and parts to be soldered, and ensure that the quality and specifications of the materials meet the requirements. Cleaning and pre-treatment of the parts to be soldered to remove oil and oxides from the surface;
Tin ball soldering operation: place the tin ball in the predetermined position of the part to be soldered, and use heat sources such as laser or resistance heat to heat the tin ball. During the heating process, the power and heating time of the heat source should be precisely controlled to ensure that the solder balls can completely melt and fully wet the parts to be connected;
Subsequent processing: After the welding is completed, the welded joints are cooled and cured. If necessary, subsequent processing such as grinding and cleaning is carried out to improve the quality and appearance of the welded joints.
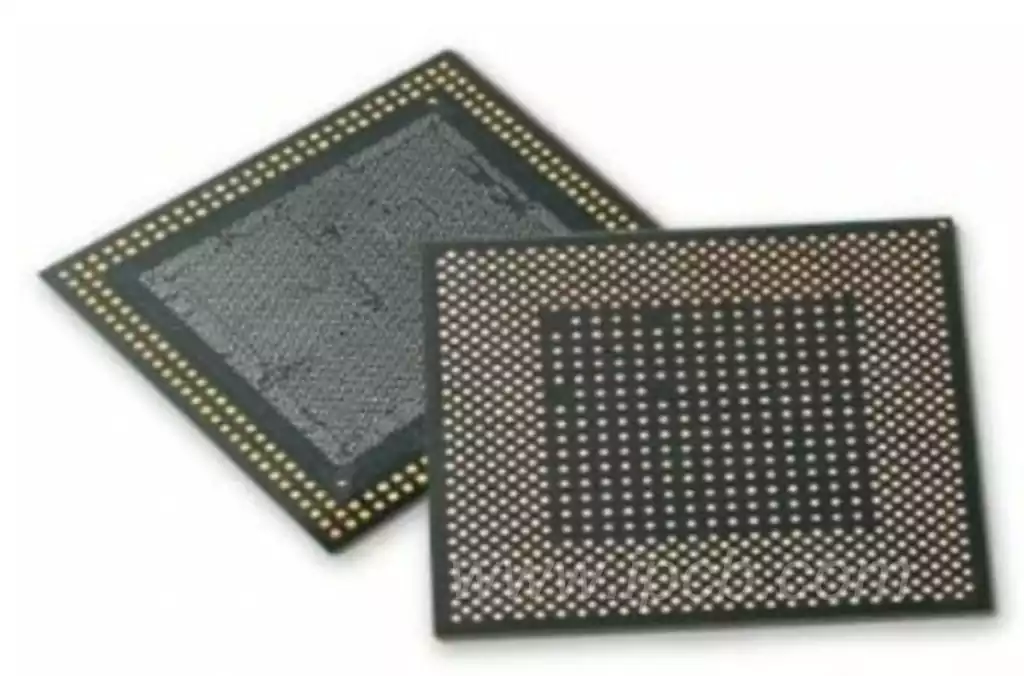
Advantages:
High welding quality:Tin ball welding uses a heat source such as laser or resistance heat,which allows precise control of the welding temperature and time, so that the tin ball completely melts and fully wets the parts to be connected,forming a solid welded joint.This type of welding ensures the quality and reliability of the welded joint;
Fast welding speed: The heating process of tin ball welding is rapid and can be completed in a short period of time, improving productivity;
Strong adaptability: tin ball welding is suitable for a wide range of materials and shapes of parts, including tiny and complex shapes of parts, with wide applicability;
High connection strength: the welded joint formed by tin ball welding has high connection strength and can withstand large mechanical and thermal stresses.
Disadvantages:
High operating technology requirements: tin ball welding requires operators to have a high level of technology and operating experience to ensure welding quality and efficiency. Training and management of operators is also a challenge;
Possible thermal damage during the soldering process: The high temperatures during the solder ball soldering process may cause thermal damage to the components, affecting their performance and lifespan. Therefore, soldering temperature and time need to be strictly controlled to avoid thermal damage;
Not applicable to all materials: Although tin ball soldering is applicable to a wide range of materials, not all materials are suitable for using tin ball soldering. Some special materials may not be able to form a good welded joint with the tin ball, limiting the scope of application of tin ball welding.
As an indispensable and important material in the fields of electronic component manufacturing, soldering and energy storage, solder balls, with their diverse types and excellent material properties, provide solid support for the development of the modern electronics industry. As the core of encapsulation technology, its quality and performance are crucial to the stability and reliability of electronic products.