The solder melting temp and selection method of tin solder is different for different ratios of tin and lead, but it is always lower than the melting temperature of any of the pure metals that make up the alloy.
For different soldering parts and soldering environments, it is necessary to choose solder with different melting temperatures and use suitable soldering methods.
The melting temperature of different materials of welding wire
- Carbon steel wire
Carbon steel wire is a commonly used welding material, its melting temperature is generally between 1300 ℃ and 1400 ℃. Therefore, in the carbon steel welding, welding process parameters and welding equipment selection should be based on the melting temperature of the wire. - Stainless steel wire
Stainless steel wire is a high-quality welding materials, its melting temperature is generally between 1350 ℃ and 1450 ℃. Due to the high melting temperature of stainless steel, so when welding stainless steel, you need to use a higher welding temperature and the corresponding welding process parameters. - Aluminum alloy wire
Aluminum alloy wire is also a commonly used welding material, its melting temperature is generally between 580 ℃ and 660 ℃. In the aluminum alloy welding, you need to pay attention to control the welding temperature to ensure that the wire melts and fuses with the workpiece.
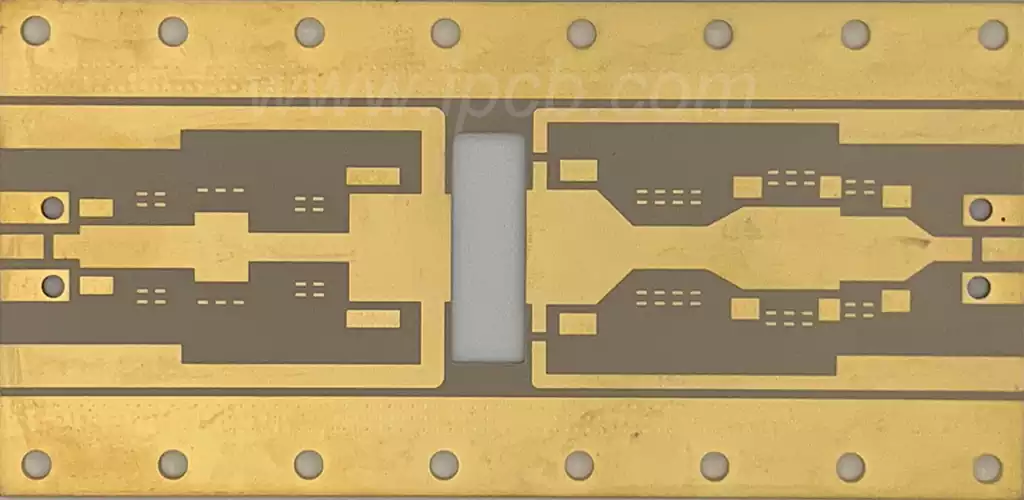
The choice of solder needs to take into account the physical and chemical properties of the circuit board, how to choose the right solder based on the characteristics of the pcb board.
- Understand the circuit board substrate
The heat resistance of the pcb substrate is a primary consideration when selecting a solder. For example, traditional FR-4 materials can withstand high soldering temperatures, while some high-frequency materials or flexible substrates may require lower temperature solder alloys. Therefore, understanding the base material’s ability to withstand the temperature will help to select the appropriate melting point of the solder. - Determine the soldering method
The method of soldering (e.g., wave soldering, manual soldering, or reflow soldering) affects the type of solder required. Manual soldering usually requires a wire that is easier to handle and flow, while automated processes such as reflow soldering may require a solder paste with specific melting point and flow characteristics. - Consider soldering temperature
The type of pcb components (such as high-temperature sensitive SMT components) and the substrate determine the maximum soldering temperature. The selection of solder should be based on these temperature limits. Selecting a solder alloy with a suitable melting point will avoid overheating and reduce thermal damage to components and substrates. - Consider the composition of the solder
The alloy composition of the solder determines its mechanical and electrical properties. For applications requiring high mechanical strength, silver-containing solders may be required.For high current applications, copper-containing solders provide better electrical conductivity.Lead-free solders,on the other hand,are widely used due to environmental needs. - Pay attention to the fluidity and wettability of the solder.
The fluidity and wettability of the solder directly affects the quality of the solder.Circuit boards on the pad plating (such as gold, tin, silver or nickel) and solder wettability should be compatible to ensure that the solder in the pad can be a good spread, the formation of uniform and non-void solder joints. - Consider environmental regulations and standards
The end use of the circuit board may be subject to specific environmental regulations, such as RoHS or REACH, so the choice of solder to ensure that it meets the relevant environmental standards. For example, electronic products sold into the EU market often require the use of lead-free solder wire.
In the soldering process, the selection of the right solder is not only about the effectiveness and efficiency of the soldering process, but also about the physical and chemical properties of the circuit boards, environmental regulations and other factors. From the melting temperature of the solder to the melting temperature of the different wire materials, every step of the selection process needs to be precisely matched to the needs of the board. Understanding the heat resistance of the board’s substrate, determining the soldering method, considering the soldering temperature, considering the composition of the solder, paying attention to the solder’s fluidity and wettability, as well as complying with environmental regulations and standards are all indispensable considerations when selecting a solder.