Lead solder is a traditional soldering material used in the production of electronic components, and its main component is lead. Lead-free solder is a new type of solder that is widely used without the addition of lead.
lead vs lead free solder
Leaded solder: This type of solder alloy contains lead. Common leaded solder alloys are expressed as a percentage, such as the “63/37” alloy, where 63% is tin and 37% is lead. This alloy usually becomes liquid at a low melting point (about 183°C or 361°F) and is easily used in soldering operations.
Lead-Free Solder: Lead-free solder alloys were developed to minimize potential hazards to the environment and health. These alloys typically use a combination of elements such as tin, silver, and copper with no or very small amounts of lead. Lead-free solder has a higher melting point (usually above 220°C or 428°F) and requires higher soldering temperatures.
Soldering Performance:
Leaded Solder: The lower melting point of leaded solder allows for relatively low soldering temperatures, helping to minimize thermal stress on electronic components. They also generally form better solder joints during the soldering process, but may have some corrosive effects on some electronic components.
Lead-Free Solder: Lead-free solder has a higher melting point and may cause some thermal stress on some temperature-sensitive components. Also, the solder joints formed by lead-free solder during the soldering process may require more attention and skill to ensure good solder quality.
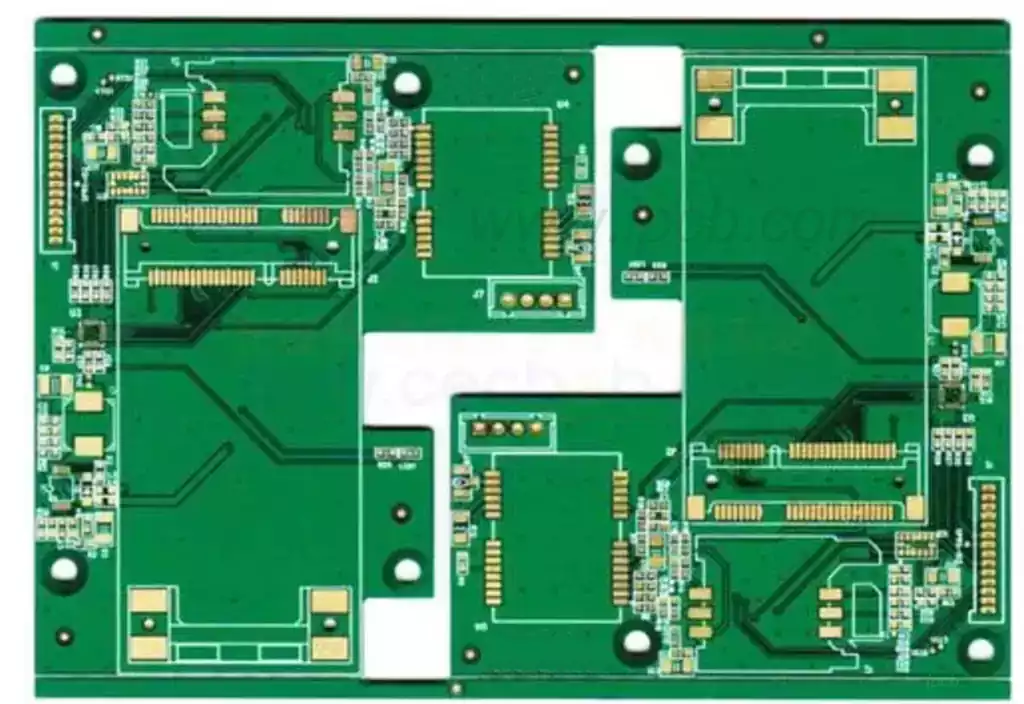
Why lead-free soldering
Improved solder quality
Compared to conventional lead soldering, lead-free soldering reduces soldering defects, such as porosity and cracks, that occur during the soldering process. This is because lead-free solder has a high melting point and is relatively difficult to oxidize, which effectively reduces the probability of gases and foreign matter being encapsulated in the solder joints that occurs during the soldering process, thus improving the quality and reliability of soldering.
Compliance with environmental requirements and health standards
Lead is a heavy metal that is harmful to the environment and human body, and its use carries certain environmental pollution and health risks. Lead-free solder, on the other hand, does not contain harmful substances and avoids lead pollution and related health problems. In today’s increasingly aware of environmental protection, the use of lead-free solder not only meets the requirements of international environmental regulations, but also enhances the corporate image and meets customer demand for healthy and environmentally friendly products.
Improve the stability and efficiency of the manufacturing process
Because lead-free solder has better wettability and wetting extensibility, it can spread better and form a more uniform and solid connection with the soldering surface. At the same time, lead-free solder has a higher melting point and maintains a solid solder connection at high temperatures, reducing the risk of solder loosening due to temperature changes during manufacturing and use of the product.
Improved Reliability and Longevity of Electronic Products
Due to the excellent physical properties of lead-free solder, the mechanical strength and heat resistance of solder joints can be improved, reducing the probability of failure and breakage. This is important for the reliability and life of electronic products. Especially for some of the high load and complex environmental use of electronic equipment, the use of lead-free soldering can better resist the temperature, vibration and humidity and other external environmental influences, to ensure product stability and reliability.
Lead-free soldering technology with its unique advantages, is gradually replacing the traditional lead soldering, become the mainstream choice in the field of electronic components production. From improving soldering quality and complying with environmental and health standards, to improving manufacturing stability and efficiency, to enhancing product reliability and longevity, it has injected new vitality into the development of the electronics industry.