Surface mount technology is an electronic assembly technology that mounts components directly onto the top surface of a printed circuit board. In contrast, through-hole assembly technology, the traditional method, requires components to be inserted into pre-drilled holes in the PCB and then connected via bottom wave soldering. While the differences between the two methods may seem subtle, they have a profound impact on board design, material selection, process requirements, and thermal performance, as well as associated labor and equipment cost considerations.
Surface mount devices (SMDs) have flat coplanar tails or leads, which allow them to be smoothly placed on specific tracks on the PCB. During the soldering process, no holes are punched in the PCB; instead, a stencil is used to apply solder paste to cover the area to be soldered. Subsequently, the components are precisely placed on the solder paste by the machine and the PCB is heated to return the solder paste and complete the soldering process.
Advantages
- SMT technology enables high-density assembly, resulting in smaller and lighter electronic products. Compared to traditional cartridge components, the size and weight of SMD components is only about one-tenth of the former. Therefore, with the adoption of SMT technology, the volume of electronic products can be reduced by 40% to 60%, and the weight can be reduced by 60% to 80%.
- SMT technology has high reliability and strong shock resistance, solder joint defect rate is low.
- SMT technology has excellent high-frequency characteristics and can effectively reduce electromagnetic and radio frequency interference.
- SMT technology is easy to realize automated production, improve production efficiency, reduce production costs by about 30%~50%, and help save resources such as materials, energy, equipment, manpower, time and space.
Disadvantages: The SMT manufacturing process has high environmental requirements, requiring strict control of temperature, humidity and other factors. At the same time, because SMT components are soldered directly to the PCB board surface, it is more difficult to replace components during maintenance and may require the use of specialized equipment and techniques.
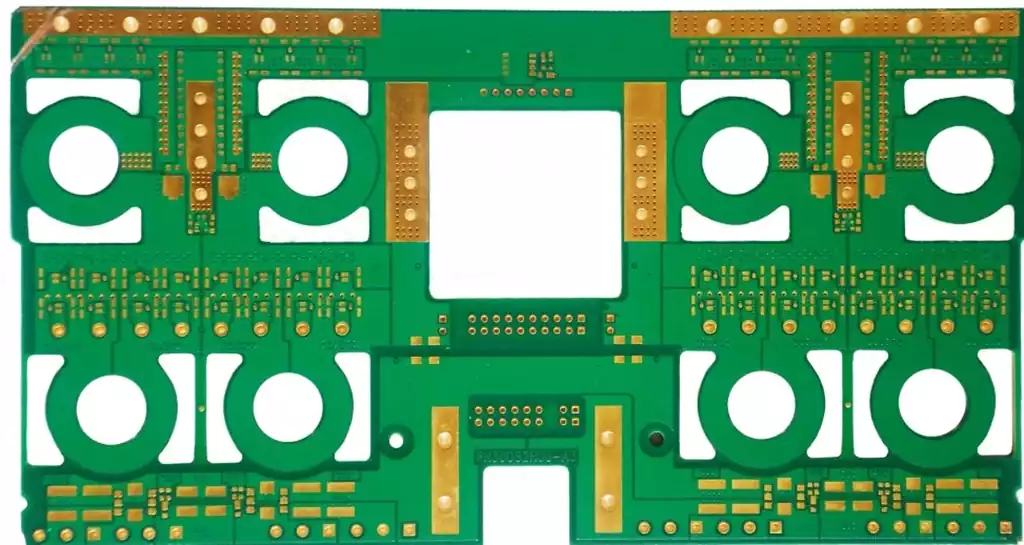
Through-hole insertion technology is an assembly method in which components with tails or leads are inserted into pre-drilled through-holes in the PCB. These components are known as through-hole assemblies. The leads can then be soldered to the pads or to pads on the bottom of the board by a wave soldering process or, of course, by hand.
A new advancement in this technology is the improvement of the traditional drilling of holes to plated through holes. After the holes are coated with solder paste, the leads are passed through the paste and subsequently the entire PCB is heated so that the solder paste reflows to complete the soldering process, a method known as through-hole reflow soldering. This technological innovation allows through-hole and surface mount technologies to be used together on the same board, as both types of components can be soldered in the same process.
Through-hole insertion technology is a well-established process trusted for the strong mechanical bond it produces. Through-hole insertion technology has fewer variables that can occur during the soldering process than surface mount technology, and these variables are usually well researched and understood. However, this technology can drive up the cost of the bare board due to the additional drilling and possible machining requirements on both sides of the PCB. It can also be relatively difficult to automate the placement of components on the PCB, as many through-board components are packaged loosely or in other bulk packages.
Advantages:
- Durable: Through-Hole solder connections are strong and have good resistance to high temperatures and vibration.
- Easy maintenance: As components are inserted into PCB holes, it is easier to replace components during repair, making it easy to maintain and repair.
- Wide applicability: Through-Hole technology is suitable for a wide range of application scenarios, especially for occasions with high reliability requirements.
Disadvantages:
- Large space occupation: Through-Hole components require additional holes, which will take up more PCB board area and limit the compactness of product design.
- Low production efficiency: Due to the low level of automation in the production line of Through-Hole technology, its production efficiency is relatively low.
Surface mount technology vs through hole
SMT technology is particularly suitable for products that require miniaturized designs, such as smartphones and tablets. For example, smart bracelets can be made thinner and lighter through the use of SMT technology, thus improving wearing comfort. Through-Hole technology is more suitable for products with high reliability requirements, such as industrial control equipment and aerospace. For example, the use of Through-Hole technology in avionics equipment ensures stability and reliability in harsh environments.
Although SMT technology has many advantages as a new assembly method, it is not a complete replacement for THT. For users, both methods have their own unique characteristics – in general, SMT technology offers higher space utilization and cost-effectiveness, while THT is superior in terms of resistance to mechanical, electrical and thermal stresses. excels in resistance to mechanical, electrical and thermal stresses. For example, components such as connectors and transformers may need to withstand large mechanical shocks. In practice, it is often necessary to use both types of assembly on the same board to meet different needs. For example, components that need to be connected to other components can be assembled using THT; other components on the board can be assembled using SMT technology.