What is annealing in semiconductor?Annealing semiconductor is a process that changes the electrical properties of a semiconductor material by heating it.
During the annealing process, the material is heated to a high enough temperature to change its internal structure, which in turn changes the conductivity of the semiconductor.
The principle of the annealing semiconductor process is an important process in semiconductor manufacturing, which improves the electrical and structural properties of semiconductor materials and increases the performance and reliability of semiconductor devices. The role of annealing is to change the position of semiconductor atoms, rearrangement and loosening inside the crystal, so that the atoms at the defects move to the inside of the defects or crystal boundaries, and the defects are eliminated or reduced to a minimum. At the same time, annealing can also help to adjust the material forbidden band width, improve the crystal quality and degree of crystallization, thus improving the electrical properties of the material.
Annealing semiconductor generally consists of three stages: heating, holding and cooling. The heating stage is mainly to raise the temperature, the length of time depends on the type and thickness of the semiconductor material; the heat preservation stage is mainly to maintain a constant temperature, the length of time is generally 30-60 minutes; the cooling stage consists of natural cooling and forced cooling in two ways, of which the natural cooling generally takes a few hours.
In semiconductor manufacturing, the main annealing semiconductor processes include furnace tube annealing, rapid thermal annealing (Rapid Thermal Annealing, RTA), laser annealing and ion beam annealing.
Furnace tube annealing, one of the oldest and still widely used annealing techniques in semiconductor manufacturing, centers on heating wafers in a long, well-designed, tubular furnace chamber. The chamber is usually protected by an inert gas, such as nitrogen,to prevent the wafers from reacting with oxygen or water vapor in the air at high temperatures. The advantage of furnace tube annealing is that it provides a relatively stable and uniform temperature environment, resulting in smaller temperature gradients on the wafers,which is conducive to achieving uniform crystal structure improvement and impurity activation. In addition, furnace tube annealing is particularly popular in mass production environments due to the relative simplicity of the equipment and low maintenance costs. However, its relatively slow heating and cooling rates may limit its application in some processes that require rapid thermal cycling.
Rapid Thermal Annealing (RTA) technology has emerged as an important complement and innovation to conventional furnace tube annealing. It utilizes a high-intensity light source (e.g., halogen or xenon lamp) to directly irradiate the wafer surface to achieve extremely fast heating rates and precise temperature control. A significant advantage of RTA over Furnace Tube Annealing is its ability to dramatically reduce heating and cooling cycles, which is critical for processes that require rapid changes in material properties or optimized dopant distribution. In addition, RTA can effectively reduce material thermal stress issues caused by prolonged high-temperature exposure, improving wafer yield and performance stability. However, the rapid temperature rise and fall process may also cause some thermal shock to the wafer surface, so it is necessary to accurately control the heating profile and cooling rate.
Laser annealing semiconductor technology further pushes the precision of the annealing process to a new height. It utilizes a high energy density laser beam, in a non-contact manner on the wafer in a specific area for accurate heating, instantly reach a very high temperature and rapid cooling. This localized heating capability allows laser annealing to show great potential for ultra-shallow junction formation, impurity activation, and micro-area repair. Laser annealing not only improves process flexibility and precision, but also significantly reduces the thermal impact on the surrounding area, facilitating the realization of more complex device structures and higher levels of integration. However, laser annealing is extremely demanding and costly in terms of equipment and operating techniques, and is typically used in the manufacture of high-end semiconductor products.
Ion beam annealing, as a cutting-edge application of annealing semiconductor technology, is unique in that it utilizes a high-energy ion beam to directly bombard the surface of the wafer, and achieves the heating effect through the interaction between the ions and the material surface. This method not only has very high heating precision and control, but also can introduce additional doping effects or improve surface roughness during the annealing process, which is important for enhancing device performance. Ion beam annealing is particularly suitable for advanced semiconductor fabrication processes that require precise control of the microstructure and surface properties of materials,such as 3D integration and nanowire transistors. However, due to the complexity of the equipment, high energy consumption and expensive maintenance costs,ion beam annealing technology is currently limited to high-end R&D and small batch production.
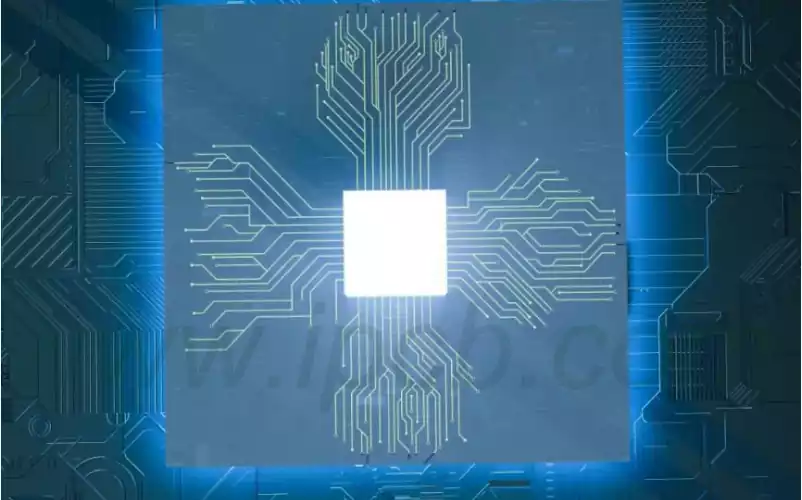
Annealing semiconductor considerations
- Different types of semiconductor materials and devices may require different annealing conditions, including temperature, time, and atmosphere.
- Excessively high annealing temperatures may cause semiconductor device burn-in or performance degradation.
- The annealing process should be carried out in a vacuum or inert atmosphere to avoid oxidation and contamination.
- The annealing process should be strictly controlled to avoid inhomogeneities caused by temperature gradients, cooling rates, etc.
Role
Improve the electrical properties of semiconductors
During the annealing process, defects in the material are repaired, impurity atoms and tethering errors within the material are aligned, fewer carriers are located in the dynamics of the energy bands, and the energy levels are relatively more dense. As a result, after annealing, the concentration of electrons and holes in the semiconductor material increases, the mobility of carriers increases, and the electrical conductivity is significantly improved.
Adjustment of material structure
Annealing can make the internal arrangement of the material more orderly, the structure has been improved. For example, molten silicon is slowly cooled at room temperature, the structural surface within the sheet produces cliffs that increase the local density until there is a certain number of covalent bonds, hydrogen atoms, or defective atoms, forming a tetrad, which creates a certain crystalline morphology. After annealing, these local cliffs flatten out, the structural surface within the sheet is greatly reduced, and the crystalline morphology is improved.
Stress Relief
In the semiconductor device manufacturing process, due to processing, process and temperature and other factors, the crystal material will produce a certain degree of stress, if not eliminated in a timely manner, will affect the electrical properties of semiconductor devices. Annealing can make the stress elimination, the material to form an equilibrium state, ease the lattice strain, reduce the number and size of lattice defects and impurities, and improve the reliability of semiconductor devices.
Annealing semiconductor process, as a key step in semiconductor manufacturing, not only optimizes the electrical properties and structure of the material, but also ensures the high performance and reliability of the device through precise control. With the continuous progress of technology, the annealing process will continue to innovate and inject new vitality into the development of the semiconductor industry.