FR4 CTE (Coefficient of Thermal Expansion) is the degree to which FR-4 material expands in response to changes in temperature.FR4 is a substrate widely used in printed circuit boards (PCBs) and consists of glass fibers and epoxy resins that are commonly used in the manufacture of high-performance circuit boards.The CTE value is usually expressed in parts per million per degree Celsius (ppm/°C),and the range of CTE values for FR4 generally ranges from 14 to 19 ppm/°C. CTE values for FR4 typically range from 14 to 19 ppm/°C.
CTE plays an important role in PCB design and performance.Mismatched CTE values between materials can lead to the development of thermal stresses, which in turn can lead to solder joint damage or mechanical problems with the board.Mismatched CTEs can also lead to component failure, such as in high-temperature environments,where temperature variations may cause FR4 to expand at a rate that is inconsistent with that of other materials, such as metal solder balls, thereby triggering solder defects.
Factors affecting FR4 CTE properties:
1.Material Composition
The composition of FR-4 material is an important factor affecting its CTE.It is mainly composed of epoxy resin and glass fiber,the type and proportion of epoxy resin,the use of fillers and the addition of inorganic fillers can significantly affect the CTE.When selecting FR-4 materials, lower epoxy resin content and appropriate fillers can reduce the CTE of the material.
2.Environmental temperature
CTE will show different characteristics at different temperatures of the material, especially when the temperature exceeds the glass transition temperature (Tg) of the material,CTE will increase significantly.This means that FR-4 expands more significantly when exposed to high temperatures, which may lead to a decrease in mechanical properties.
3.Laminated structure
The laminate structure of FR-4 material is also an important factor affecting FR4 CTE.When designing a multilayer PCB,the relative position of the layers, the number of layers, and the type of material in each layer will all affect its overall thermal expansion properties.Especially when designing high-density circuit boards, precise control during the manufacturing process is especially important to avoid problems caused by CTE mismatches between different materials.
4.Electrical Characteristics
The electrical properties of FR-4 materials also affect FR4 CTE; for example, differences in the CTE of a board’s conductive material (e.g., copper) versus its substrate can lead to stresses during the heating process, which can cause mechanical failures. This interaction is particularly significant in high-frequency applications, where high-frequency signals can exacerbate thermal effects.
5.Design and Manufacturing Process
Finally, the design and manufacturing process of the PCB is also a consideration.A number of design strategies can optimize the FR4 CTE characteristics of the material, such as the design of thermal vias, the density of copper layup, and the layout of components. These design optimizations can help control thermal management and reduce potential failures due to thermal expansion.
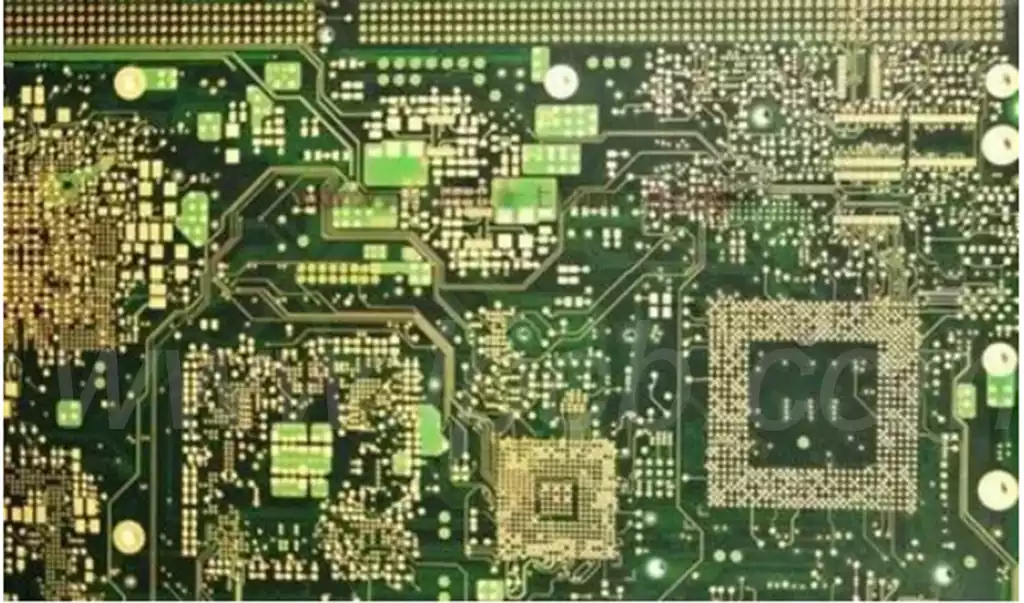
FR4 CTE has a significant impact on its application and performance. Differences in CTE can lead to stresses in electronic components during temperature changes, which in turn can affect the reliability of solder joints and the overall performance of the board. Therefore, in the design and manufacture of electronic products, special attention needs to be paid to the CTE characteristics of FR-4 materials to ensure their stability and reliability in a variety of application environments.
1.CTE and thermal stress
FR4 CTE may differ significantly in different directions.For example,the CTE of FR-4 in the z-axis direction perpendicular to the plate plane may be different from that in the x-y direction. When the temperature rises,the material expands in the z-direction,which can lead to a concentration of thermal stresses on the board, which can affect the integrity of the solder joints and the quality of the solder.Thermal stresses in high temperature environments can accelerate the aging of solder joints, which in turn affects the reliability of the overall circuit.
2.The effect of CTE on soldering performance
In the soldering process, the difference in CTE between different materials may lead to uneven stress on the solder joints, resulting in cracks or peeling problems. In the use of surface mount technology (SMT), due to the lack of lead buffer stress, this difference is particularly obvious, the component body will be directly affected by thermal stress. Therefore, the CTE of FR-4 material needs to be matched with other electronic components to reduce the stresses caused by temperature changes and thus improve the reliability of the solder joints.
3.CTE and circuit board design
When designing circuit boards, it is critical to understand the CTE characteristics of FR-4 materials. Designers need to consider the impact of the coefficient of thermal expansion (CTE) on board size, layout and material selection. In order to reduce the risk of thermal deformation due to temperature changes, the design can optimize thermal management by adding heat sinks, reasonably allocating component spacing, and adding vias. Such a design strategy can effectively improve the thermal performance and overall stability of the circuit board.
4.CTE and material selection
Choosing the right material is the key to ensuring the performance of electronic products. FR-4 has a relatively high CTE, which may not be suitable for all high-frequency or high-power density applications, so in this case, it is necessary to consider the use of materials with a lower CTE, such as ceramic or metal substrates, which can provide higher thermal stability and reliability. As shown in the comparison between aluminum and FR-4, the coefficient of thermal expansion of aluminum substrates is closer to that of copper foil, which is more conducive to the quality and reliability of the board.
5.Application of CTE in debugging and troubleshooting
Understanding the CTE characteristics of FR-4 materials helps to make more effective judgment in the debugging and troubleshooting process. Failures caused by temperature changes are often closely related to the characteristics of the CTE,so keeping an eye on the CTE can help engineers quickly identify and solve problems caused by thermal expansion, improve product maintenance efficiency and user experience.
Methods of measuring the coefficient of thermal expansion of FR-4 materials in specific applications:
- Experimental Measurement Method
The coefficient of thermal expansion (CTE) of FR-4 materials is usually measured directly by thermo-mechanical analysis (TMA) or differential scanning calorimetry (DSC). These experimental techniques are able to observe the mechanical behavior of the material under temperature changes, thus providing specific values for the CTE. For example,using TMA it is possible to obtain the thermal expansion curve of a material over a range of temperatures, from which the CTE value can be calculated. - Theoretical calculation method
In addition to experimental measurements,CTE can also be obtained by theoretical calculations.This usually involves taking known material property data and deriving the CTE from thermodynamic models and formulas, which can be applied after taking into account information such as the ratio of glass fibers to epoxy resin, laminate structure, etc. However, theoretical calculations are often inaccurate.However,the accuracy of the theoretical calculations often depends on the accuracy of the input parameters. - Material Characterization Test
FR4 heat can also be obtained indirectly by testing the thermophysical properties of the material.For example,the glass transition temperature (Tg) and structural properties of the material are measured and then compared in conjunction with known CTE values to assess current material performance. Appropriate material selection can effectively reduce the CTE and improve the stability of the board in use. - Analysis of influencing factors
In practice, the CTE of FR-4 materials may be affected by a variety of factors, including temperature, humidity, structural design and thermal stress in the soldering process. Therefore, when measuring CTE, not only the characteristics of the material itself should be considered,but also its performance in the actual working environment should be paid attention to. For example, the CTE of FR-4 may increase under high temperature conditions,so it is necessary to select a suitable operating temperature range to ensure the reliability of the material. - Application Scenarios
In high-frequency and high-temperature applications, the selection of FR-4 variants or modified materials with lower CTE is essential. Such a choice not only ensures the stability of the board under thermal cycling, but also effectively avoids mechanical stresses caused by temperature changes, thus extending the service life of the equipment.
FR4 CTE is an important indicator of the reliability of PCB design and electronic products. changes in CTE can lead to thermal stress, which affects the integrity of the solder joints and circuit performance, so in the design and material selection need to take into account the CTE characteristics of FR-4.