PCB thermal relief refers to the process of heat management and control for printed circuit boards (PCBs). As the PCB is integrated with a large number of electronic components, these components in the work will produce heat, if not timely and efficiently emitted, will lead to PCB temperature rise, which in turn affects the performance and stability of the components, and may even lead to failure.
The main purpose of PCB heat dissipation is to ensure that the electronic components on the PCB in the appropriate operating temperature range, to prevent damage or performance degradation due to overheating. Thermal design usually includes optimizing the PCB layout, selecting the appropriate thermal materials, the use of thermal components (such as heat sinks, heat sinks, cooling holes, cooling fans, etc.), as well as controlling the ambient temperature and other methods.
Basic Principles of Thermal Design
During the operation of an electronic device, electronic components consume electrical energy, some of which is converted into heat. This heat energy is then transferred to the external environment through conductors (e.g., foil) and insulators (e.g., circuit board substrates). If heat is not effectively dissipated from the board, the temperature of the component will rise, which may adversely affect its performance and lifetime.
Key Elements of Thermal Design
PCB Layout Design: A good PCB layout design can significantly improve its thermal performance. First, high power consumption components should be placed as far away as possible from poor heat dissipation areas, such as enclosed spaces or other heat sources. Second, the spacing between components should be set reasonably to ensure unimpeded airflow. In addition, overly dense wiring should be avoided to prevent heat conduction and dissipation.
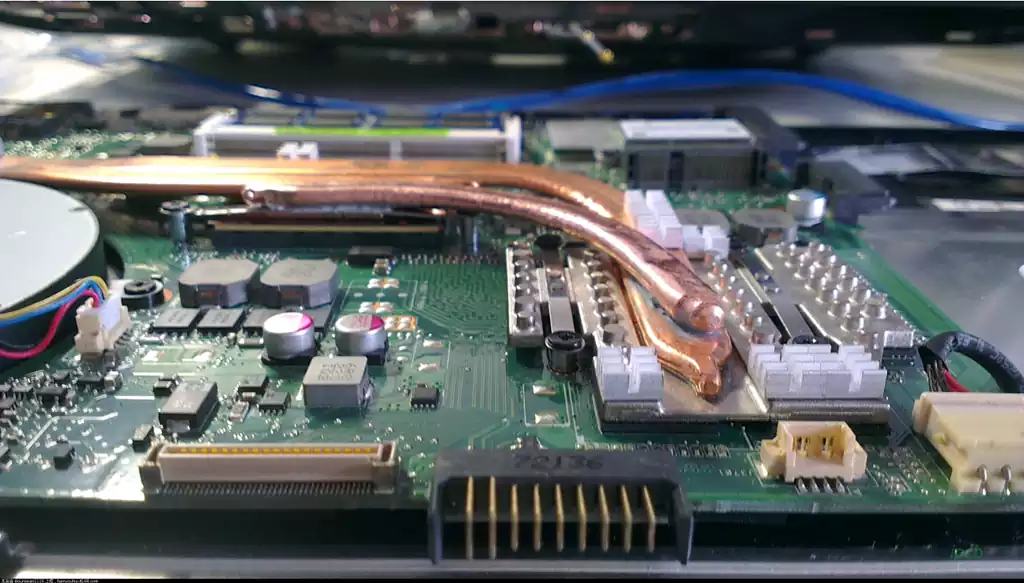
Heat conduction: In PCB thermal design, heat conduction is crucial. To enhance heat conduction, the following measures can be implemented:
- Utilize metal foil as a heat dissipation material to connect high power consumption components to heat sinks or metal substrates to enhance heat conduction efficiency.
- Optimize the selection of PCB substrate materials and use materials with high thermal conductivity, such as aluminum or copper substrates, to enhance heat conduction.
- Apply thermal conductive materials such as thermal spacers or thermal adhesive to realize direct contact between components and heat sinks to promote heat conduction.
Heat sink design: Heat sink is a key component commonly used in PCB thermal design. Its main function is to conduct heat from the circuit board to the surrounding environment. When selecting and designing a heat sink, the following elements need to be considered:
- Size and shape of the heat sink: The size and shape of the heat sink should be reasonably selected according to the power consumption and heat dissipation requirements of the circuit board. Large heat sinks can provide a larger surface area for heat dissipation, which in turn improves the heat dissipation effect.
- Heat sink materials: common heat sink materials include aluminum and copper. Aluminum radiators have excellent thermal performance and lightweight characteristics, while copper radiators have higher thermal conductivity. The appropriate material should be selected according to the actual needs.
- Installation location of the heat sink: The heat sink should be installed near the components in the board that generate a lot of heat to ensure that the heat can be quickly transferred to the heat sink. The space limitations of the heat sink and the interaction with other components should also be considered.
Air flow and cooling fans: For high power circuit board design, relying on heat sinks alone may not be sufficient to meet the heat dissipation requirements. In this case, the introduction of a cooling fan can be considered to enhance air flow and further improve heat dissipation. Cooling fans promote heat transfer and dissipation by generating airflow. When selecting a cooling fan, the appropriate size, airflow and speed should be determined based on power consumption and cooling requirements.
In electronic equipment, heat dissipation design is crucial, and the thermal relief pcb, as the carrier of electronic components, is especially critical. By optimizing the layout, selecting appropriate thermal materials, applying heat sinks, and controlling air flow, we can effectively manage the heat on the PCB and prevent components from being damaged or degraded in performance due to overheating. As technology continues to advance, thermal design will continue to be a key component in the development of electronic devices, providing solid support for improving device performance and reliability.