A PCB hot plate is a heating device that is used to heat PCBs by controlling the temperature and heating time.The process usually involves placing the PCB on a heated plate so that it quickly reaches the desired temperature, thus facilitating processes such as soldering and curing.The hot plate utilizes uniform heat distribution, which effectively avoids localized overheating or unheated areas and ensures that all parts of the entire PCB are treated evenly.
Features of pcb hot plate processing
1.High efficiency
Hot plate processing can quickly heat the PCB board,so that it reaches the required temperature in a short period of time, thus speeding up production. This rapid heating characteristics in mass production is particularly important, can effectively improve the overall work efficiency.
2.Uniformity
Hot plate can provide uniform heat distribution,to ensure that all parts of the PCB board is heated evenly, to avoid localized overheating or unheated areas. This uniform heating helps to reduce quality problems caused by temperature differences and improve the reliability of the final product.
3.Flexibility
By adjusting the temperature and time of the heating plate, it is possible to realize flexible control of different processing needs of the PCB substrate.This flexibility allows hot plate processing to adapt to the requirements of a variety of production processes to meet the needs of different types of PCB production.
In addition to the above features,hot plate processing can also improve the physical properties of the PCB, improve the electrical properties, and provide a better basis for subsequent production processes. In addition, the relatively simple operation and low maintenance costs of hot plate technology also make it a widely used heat treatment method.
In the hot plate treatment process, the control of temperature and time has a significant impact on the quality of printed circuit board:
1.The effect of temperature
Temperature is one of the most critical parameters in the hot plate processing. In the manufacture of PCB multilayer boards,the precision and stability of temperature control during the hot press curing process directly affects the yield and quality of the product. Too high or too low a temperature will lead to a decline in the performance of the material, which in turn affects the strength and conductivity of the board, increasing the risk of producing defective products.
2.The impact of time
In addition to temperature, processing time is equally important.Too long a heating time may lead to thermal damage to the PCB material,affecting its mechanical and electrical properties. In contrast, too short a processing time may lead to incomplete curing, can not achieve the expected strength and stability. Therefore, reasonable time control can help ensure that the material reaches the best physical state, thereby improving the overall quality of the PCB.
3.Temperature and time coordination
The role of temperature and time coordination can not be ignored.In the hot plate operation, the need for specific material types and design requirements, balancing these two parameters to achieve the best results.For example,for some high-performance PCB materials,may require higher temperatures and shorter processing time, and vice versa, to ensure that its indicators can meet industry standards. This reasonable parameter settings can guarantee the stability and durability of the circuit board in the high-temperature operating environment.
4.Affect the yield and reliability
Reasonable control of temperature and time not only affects the immediate quality of the PCB, but also related to the long-term reliability of the product. Effective heat treatment can effectively reduce the defect rate of PCB, improve its performance stability in long-term use, which is particularly important for high-reliability applications such as military, medical equipment. Therefore, in the design of the heat treatment process, need to pay attention to the optimization and adjustment of these two parameters.
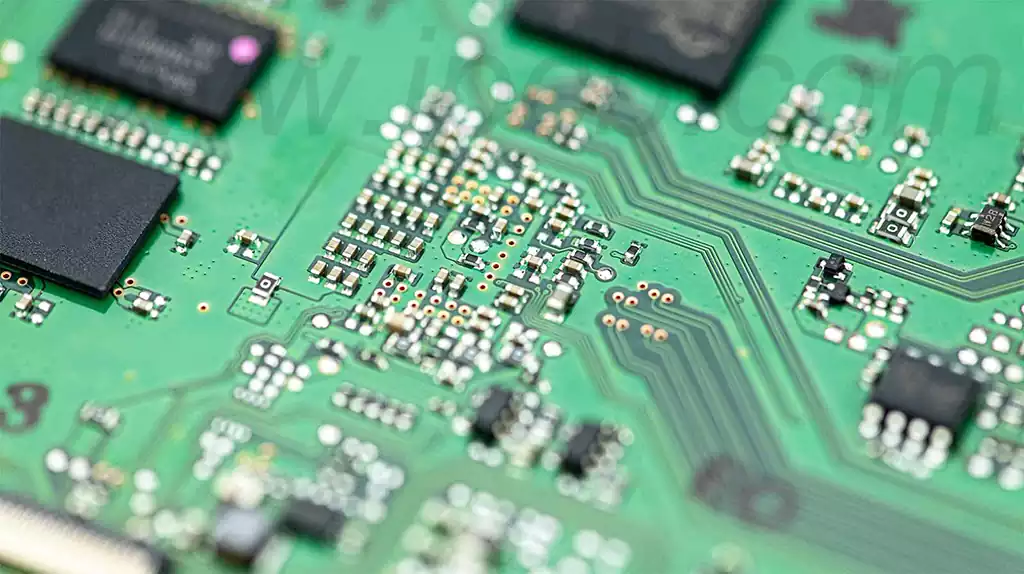
Hot plate processing has a wide range of application examples in PCB manufacturing:
1.Application in the soldering process
One of the most common applications of hot plate processing is in the PCB soldering process. In Surface Mount Technology (SMT), hotplates provide uniform heating to ensure a good connection of solder joints and reduce soldering defects. At the same time, the hot plate effectively removes air bubbles and other soldering defects, thereby improving solder quality and reliability.
2.Interlayer Curing
In multilayer PCB manufacturing, hot plate processing is used in the interlayer curing process to promote the hardening of adhesives and resins. This not only improves the bond strength between each layer, but also effectively reduces stress and optimizes the overall structural stability of the multilayer circuit board. This technique is critical to improving the reliability of PCBs in a variety of operating environments.
3.Thermal management program
Hotplates also play a key role in the PCB’s thermal management program. Through hot plate processing, more sophisticated heat dissipation systems can be designed to ensure that electronic components maintain proper temperatures under high workloads. For example, hotplates can be used to arrange thermally conductive materials or embed heatpipes to enhance the thermal efficiency of a device. This optimization scheme is particularly important for high-performance computing or intensive electronic devices.
4.Efficiency Improvement
Hot plate technology can significantly improve production efficiency.In the production process, fast and uniform heating PCB,can shorten the processing time, enhance the overall production line efficiency. This rapid response capability for the increasing demand for modern electronic equipment and the speed of modernization has played a positive role in promoting.
5.Strong adaptability
The adaptability of hot plate processing makes it advantageous in processing PCBs of different materials and specifications.Adjusting the heating temperature and time, you can design the corresponding heat treatment parameters for different types of circuit board, and this flexibility helps manufacturers to cope with changing market demand and product specifications.
As an indispensable technology in PCB manufacturing, the efficiency, uniformity and flexibility of hot plate processing bring significant advantages to the production process. By reasonably controlling temperature and time, manufacturers can not only improve the overall quality and reliability of PCBs, but also effectively reduce production defects and improve work efficiency. With the trend of miniaturization and complexity of electronic products, the application of hot plate processing technology will be more extensive, and its importance will be more and more prominent. Therefore, the continuous optimization of the hot plate treatment process will provide more powerful support for the future of PCB manufacturing, and promote the continuous progress and innovation of industry technology.