Soldering cold joint is due to circuit board SMT processing in the reflow soldering process, the solder at the solder does not reach its melting point temperature or welding heat is not enough, so that in the wetting or flow before the solidification, not to form any metal alloy layer, so that all or part of the solder in the non-crystallization of the strong state and simply build up in the soldered metal surface.
Circuit board soldering is prone to cold soldering causes
Insufficient temperature
In circuit board welding, if the welding temperature is insufficient, the electrode on the solder can not reach the full wetting, the solder joint and pad contact area is small, the welding strength is poor. This situation is prone to cold soldering.
Insufficient soldering time
If the welding time is not enough, the wetting ability of the solder will also decrease, which will lead to a smaller contact area between the solder joint and the pad, and a decrease in the strength of the weld. Cold soldering is also easily caused.
Oxidized metal surface
If there is an oxidized layer on the metal surface before soldering, the solder cannot fully contact with the metal during soldering, which will also lead to a small contact area between the solder joints and the pads, and easily cause cold soldering.
Problems with the structural design of the pcb board
The structural design of the pcb board may also affect the contact area of the solder joints and pads, which in turn affects the quality of soldering. For example, the pad area is too small, the pad distance is too close, etc., will lead to the emergence of cold welding phenomenon.
Equipment aging or improper use
Equipment aging or improper use may also lead to the emergence of cold soldering. For example, the failure of the temperature control system of the soldering equipment, the soldering process parameters are set incorrectly, etc., will have an adverse effect on the quality of soldering, which is worth noting.
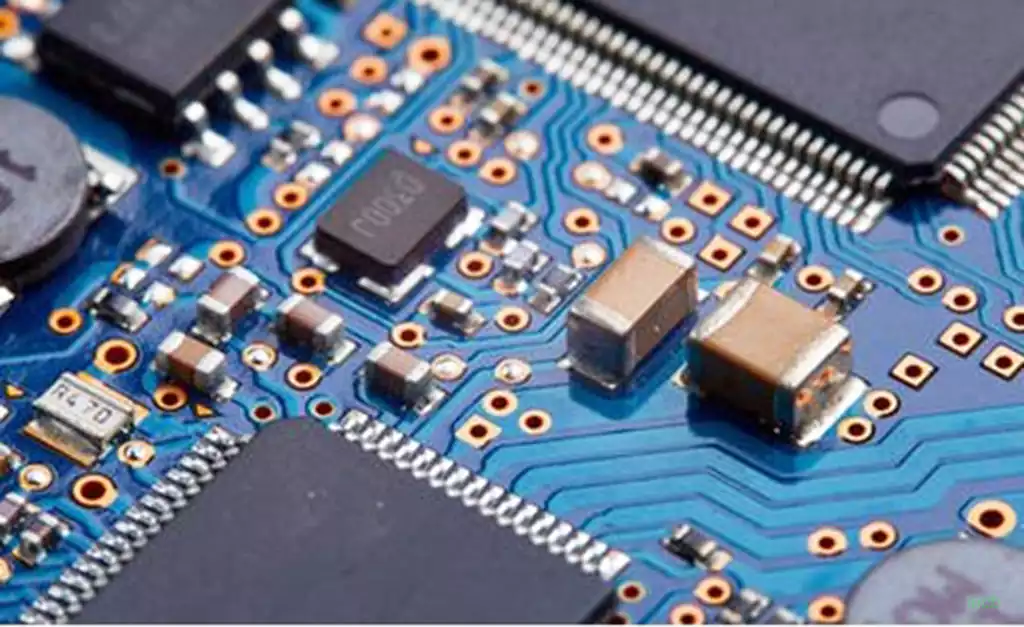
Cold soldering spots easily lead to circuit board failure, which is manifested in the following cases:
- Poor contact. The solder joints on the circuit board are the connection points between different devices, if the quality of the solder joints is not good, it will lead to poor contact between the devices, which will lead to the overall failure of the circuit board.
- Signal interference. If the cold solder joints are connected to the signal line or ground line, etc., due to poor contact, it will produce interference signals, affecting the signal transmission of the entire circuit board.
- Short circuit or broken circuit. Cold solder joints with unstable contact are prone to short circuit or broken circuit in vibration or operation, resulting in the failure of the entire circuit board.
The hazards of cold soldering
Cold soldering can have a serious impact on the performance and reliability of the circuit board, and serious cold soldering can even lead to circuit board failure. Common hazards are:
- increase line resistance, inductance and capacitance values, affecting the stability of circuit performance.
- Decrease the contact area between the device pins and the solder joints, reducing the quality of welding, resulting in component dislodgement, disconnection or short-circuit and other problems. 3.
- affect the life of the circuit board, in a long time under high load working condition, easy to trigger the circuit board temperature rise caused by the failure of the problem.
Cold welding solutions
- Requirements for welding process specifications, control the welding temperature, time and amount of solder and other parameters. 2.
- Provide a good welding environment, to ensure that the surface is clean, no oil, chemical residues and other material pollution.
- Reasonable arrangement of the welding process, reduce the thermal shock and thermal stress of the welding process on the circuit board, control the welding temperature of the rise and fall of the speed, to avoid generating too much welding heat.
- Strengthen the quality control of the solder, the use of qualified solder wire or solder paste and other materials to ensure its wettability and reliability.
In the circuit board SMT process, the soldering cold joint problem can not be ignored. It not only affects the performance and reliability of the board, but also may lead to the failure of the entire board. In order to effectively solve the cold welding problem, we must start from the welding process, welding environment, welding process and solder quality and other aspects of the implementation of strict control and management. By improving the level of soldering technology, optimize the soldering environment, reasonable arrangement of the soldering process and strengthen the quality control of the solder, we can effectively reduce the occurrence of this phenomenon, to ensure the stability and reliability of the circuit board soldering quality.