What is industry standard PCB thickness?The standard PCB thickness for 2 layers is 1.6mm.Depending on the specific requirements of the design, measurements other than the standard measurements are used in the PCB design. Typically PCB thicknesses range from 0.2mm to 3.2mm. 0.2mm PCB standard thickness is used for thin and flexible PCBs, but on the other hand 3.2mm thickness is suitable for heavier boards that require high current carrying capacity.
Common PCB thickness types
0.8mm: This is typically used for small devices or in applications where weight reduction is important.
1.0mm: This standard printed circuit board thickness is used for handheld devices or electronics that require moderate thickness.
2.0mm: This is used for PCBs that require good mechanical strength and durability.
3.2mm: The common use of standard PCB thicknesses can be seen in boards that carry and handle huge amounts of power. They are also used for boards that provide extra durability.
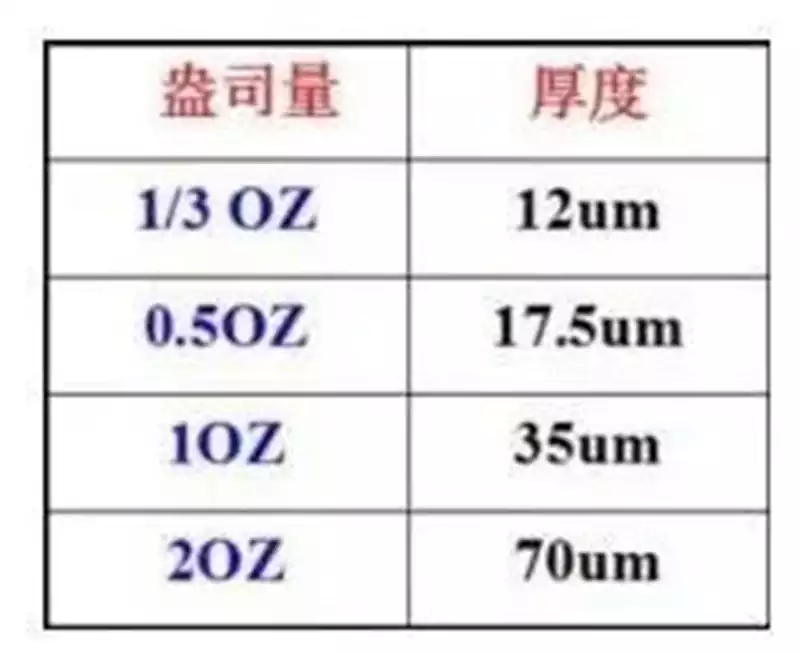
There are many design and manufacturing factors to consider when determining PCB board thickness, such as:
Copper thickness
Plate material
Number of PCB layers
Signal type
Type of vias
Operating environment
Manufacturing factors that affect PCB thickness include:
Process capability of the drilling equipment
Copper thickness
Number of layers
Depaneling method
Standard circuit board thickness plays a vital role in the achievement of electrical, mechanical and thermal performance of the circuit board.The following are the main purposes for which standard PCB thickness is critical to PCB performance:
Mechanical robustness and durability:One of the main purposes of standard PCB thickness is to give the board the necessary rigidity and mechanical strength. With thicker PCBs,resistance to bending, twisting and other mechanical stresses is significantly increased. For applications that operate in harsh environments, thicker PCBs are often required to withstand physical stress and vibration.
Current Carrying Capacity:The thickness of the copper directly affects the current carrying capacity of the PCB.Therefore,using thicker copper alignments ensures that large currents flow smoothly without causing excessive heating or voltage drops. In power electronics, such as power supplies or motor control boards, thicker PCBs are used to handle higher currents and maintain thermal stability, which is a key factor affecting the thickness of standard FR4 PCBs.
Thermal Management Effectiveness:PCB thickness is also critical for effective heat dissipation. In this regard, thicker PCBs and heavier copper layers are able to spread heat more efficiently across the board surface, which is especially important for high-power applications or devices that operate in high-temperature environments. In addition, thicker PCBs provide more layers to optimize grounding and power distribution to manage thermal issues more effectively.
Impedance Control Precision:In PCBs used in communication devices or computing systems, operating speeds are often high, making it difficult to control the impedance of signal alignments. Standard PCB thickness affects the width of the alignment and the spacing required to achieve the desired impedance level. Thicker PCBs allow for better separation between layers, helping to reduce signal interference and improve overall signal integrity.
Increased Design Flexibility: Thinner PCBs, such as flexible or rigid-flex PCBs, are commonly used in applications that need to bend or fit into tight spaces compared to the common standard 2 layer PCB thickness.This is particularly common in smartphones, wearables or avionics. In these cases, reducing PCB thickness provides the necessary flexibility while maintaining circuit functionality.
Component Mounting and Assembly Ease: Standard PCB thickness also affects how components are mounted and soldered to the board. Thicker PCBs provide more support for heavy components such as transformers, connectors, or large capacitors, ensuring that solder joints can withstand the weight without cracking or peeling. In addition, thicker PCBs typically have more solid plated through holes, which is critical for mounting components that require mechanical stability, such as connectors.
Signal Integrity and Crosstalk Reduction: For multi-layer PCBs, the overall thickness helps maintain the necessary separation between the signal, power and ground layers. This separation is critical to prevent signal crosstalk in high-speed designs. For more effective shielding against EMI, it is relevant to use thicker boards with additional layers, which also helps reduce the potential for signal degradation in the board.
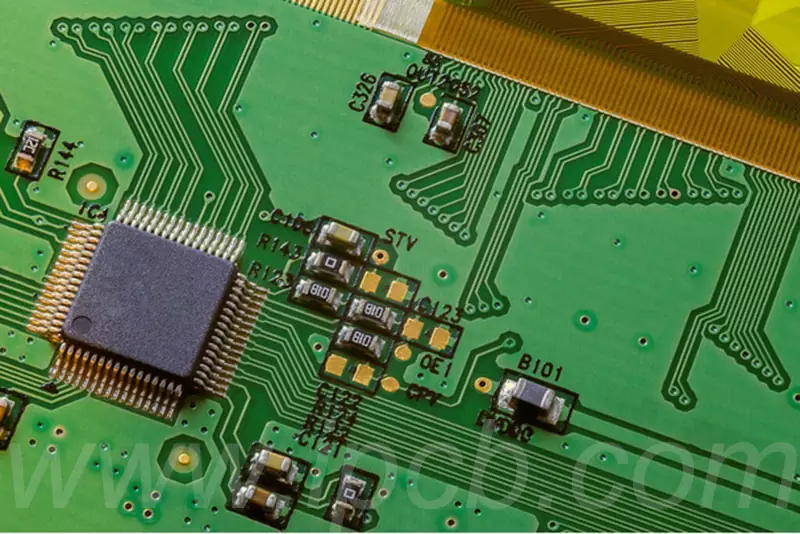
Key elements to keep in mind when it comes to non standard thickness PCB designs:
Manufacturer’s process level
The primary consideration is whether the board manufacturer you choose has the capability to produce the boards in the thickness you require. This decision should be made early in the design process and should take into account other DFM (design for manufacturing) requirements. Otherwise, you may need to adjust the design or even re-plan the PCB stacking structure.
Extended Production Cycles
If the selected materials are not always available from the manufacturer, this often leads to a lengthening of the PCB’s production cycle. Therefore, for boards with non-standard thicknesses, the production cycle is a factor that needs to be taken seriously.
Increase in cost
This is probably the most critical point. You need to evaluate the cost of purchasing special boards, the additional manufacturing costs, and the costs incurred due to extended production lead times to determine if these additional costs are within acceptable limits.
Using standard PCB thicknesses usually ensures faster production and lower costs. However, if you decide to use a non-standard thickness, you should talk to the manufacturer immediately before starting the PCB design to confirm that their process can meet the requirements and to clarify the production lead time and additional manufacturing costs.
The choice of PCB thickness is a decision-making process that takes into account design requirements, manufacturing processes and cost-effectiveness.