Prepreg, short for “pre-impregnated,” is a composite material where fibers such as carbon, glass, or aramid are pre-impregnated with a resin matrix. This combination of fiber and resin is partially cured, providing a flexible but tacky sheet that can be easily handled and shaped into complex forms. Prepregs are widely used in high-performance applications where precision, strength, and lightweight properties are critical, such as in aerospace, automotive, sporting goods, and renewable energy industries. This article will delve into the composition, manufacturing processes, advantages, applications, and future trends of prepreg materials.
Composition of Prepreg
The primary components of prepreg materials are the reinforcement fibers and the resin matrix.
- Reinforcement Fibers:
Carbon Fibers: Known for their high strength-to-weight ratio and stiffness, carbon fibers are commonly used in aerospace and high-performance automotive applications.
Glass Fibers: These fibers are less expensive than carbon fibers and offer good strength and electrical insulating properties, making them suitable for a wide range of applications.
Aramid Fibers: Known for their exceptional toughness and resistance to impact and abrasion, aramid fibers are often used in ballistic protection and sporting goods. - Resin Matrix:
Epoxy Resins: These are the most commonly used resins due to their excellent mechanical properties, chemical resistance, and ability to cure at relatively low temperatures.
Phenolic Resins: Known for their fire-resistant properties, phenolic resins are used in applications requiring high thermal and flame resistance.
Polyester and Vinyl Ester Resins: These resins offer good mechanical properties and are more cost-effective than epoxy resins, making them suitable for large-scale applications.
Manufacturing Processes
The manufacturing process of prepreg involves several steps to ensure that the fibers are uniformly coated with the resin and partially cured to achieve the desired properties. The primary steps include:
- Fiber Spreading:
The fibers are spread into a thin, uniform layer to ensure even resin impregnation. This can be achieved using various techniques such as mechanical spreading or air-jet spreading. - Resin Application:
The resin is applied to the fibers using methods like hot melt or solvent coating. In the hot melt process, the resin is heated to a liquid state and applied to the fibers, while in the solvent coating process, the resin is dissolved in a solvent and then applied. - Partial Curing:
After the resin is applied, the prepreg is partially cured or “B-staged” to achieve a tacky but solid state. This partial curing allows the prepreg to be easily handled and laid up into molds without excessive resin flow. - Storage:
Prepregs must be stored under controlled conditions, typically at low temperatures, to prevent further curing before they are used in the final part fabrication.
Advantages of Prepreg
Prepreg materials offer several advantages over traditional composite manufacturing methods, including:
- Consistent Quality:
Prepregs are manufactured under controlled conditions, ensuring consistent fiber distribution and resin content, leading to high-quality, uniform parts. - High Performance:
The precise control over the fiber-resin ratio and the ability to use advanced fibers and resins result in parts with superior mechanical properties and performance. - Reduced Waste:
The pre-impregnated fibers can be cut and laid up with minimal waste compared to wet layup processes, where excess resin and fibers often need to be trimmed away. - Improved Workability:
The tacky nature of partially cured prepreg allows for easy handling and placement, especially in complex molds, reducing the labor and time required for layup. - Enhanced Surface Finish:
The uniform resin distribution and reduced air entrapment in prepreg parts lead to a smoother surface finish, often requiring less post-processing.
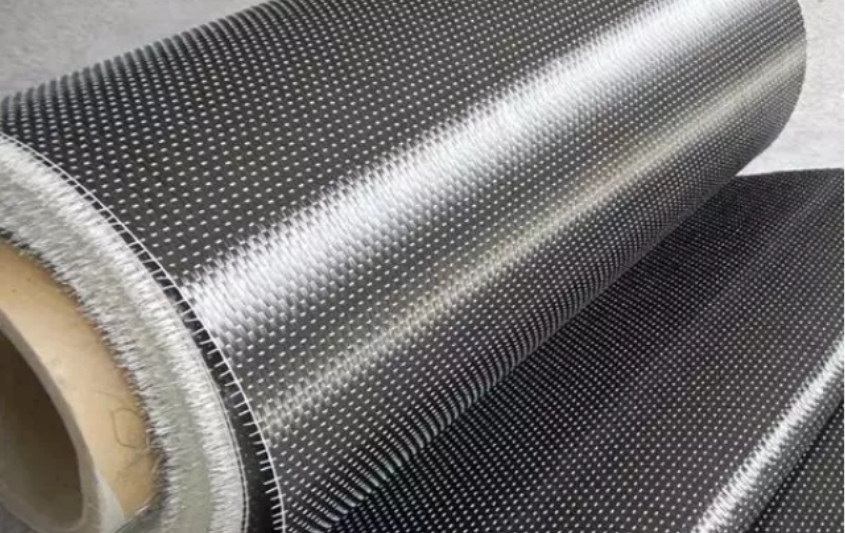
Applications of Prepreg
Prepregs are used in a wide range of industries and applications where high performance, precision, and lightweight properties are essential.
- Aerospace:
Prepregs are extensively used in the aerospace industry for manufacturing aircraft structural components, such as wings, fuselages, and tail sections. The high strength-to-weight ratio of prepreg materials helps reduce the overall weight of the aircraft, improving fuel efficiency and performance. - Automotive:
In the automotive industry, prepregs are used for producing high-performance components such as body panels, chassis parts, and interior trim. The use of prepreg materials contributes to weight reduction and enhanced performance in sports cars and racing vehicles. - Sporting Goods:
Prepregs are popular in the sporting goods industry for manufacturing equipment like tennis rackets, golf clubs, bicycles, and skis. The lightweight and high-strength properties of prepregs improve the performance and durability of these products. - Renewable Energy:
In the renewable energy sector, prepregs are used in the production of wind turbine blades. The high stiffness and strength of prepreg materials allow for longer and more efficient blades, increasing the energy output of wind turbines. - Marine:
The marine industry uses prepregs for constructing boat hulls, masts, and other components. The corrosion resistance and lightweight properties of prepregs enhance the performance and longevity of marine vessels.
Future Trends
The use of prepreg materials is expected to grow as advancements in materials science and manufacturing technologies continue to evolve. Some key trends include:
- Sustainable Prepregs:
The development of bio-based resins and recyclable fibers is gaining traction, driven by the increasing focus on sustainability. These eco-friendly prepregs aim to reduce the environmental impact of composite materials. - Advanced Manufacturing Techniques:
Innovations in automated fiber placement (AFP) and automated tape laying (ATL) technologies are enhancing the efficiency and precision of prepreg manufacturing. These techniques enable the production of complex, high-performance parts with reduced labor and material costs. - Enhanced Performance Materials:
Ongoing research is focused on developing new fibers and resins with improved mechanical properties, thermal resistance, and electrical conductivity. These advancements will further expand the applications and performance of prepreg materials. - Customization and Hybrid Composites:
The ability to tailor the fiber orientation and resin composition in prepregs allows for customized solutions to meet specific application requirements. Additionally, hybrid composites combining different types of fibers and resins are being explored to achieve unique property combinations.
Prepreg materials represent a significant advancement in composite manufacturing, offering unmatched performance, precision, and versatility. Their applications span across various industries, from aerospace and automotive to sporting goods and renewable energy. As technology and materials science continue to advance, the use of prepregs is expected to expand further, driving innovation and sustainability in high-performance composite applications. Understanding the composition, manufacturing processes, advantages, and future trends of prepregs provides valuable insights into the potential of these remarkable materials in shaping the future of lightweight, high-strength structures.