Why FPC SMT must use the fixture, FPC flexible board has a unique physical characteristics, so it can not be directly applied to the standardised SMT (surface mount technology) production process. The special carrier with its deformation suppression, thermal conduction optimisation, precise positioning, electrostatic protection and process compatibility and other five core functions, can effectively solve the FPC soft board in the soldering process faced by a variety of problems, to ensure that the soldering quality. Therefore, FPC flexible board welding must use a special fixture, which is to protect product quality and production efficiency of the inevitable choice.
The unique physical properties of the flexible circuit board
Ultra-thin form: FPC flexible board thickness is usually in the range of 0.1 – 0.3mm, compared to rigid PCB, only 1/5 – 1/10 of the latter, this ultra-thin structure makes the FPC in the production operation is very prone to deformation, it is difficult to maintain a stable form.
Low modulus of elasticity: The modulus of elasticity of the polyimide substrate used is only 3 – 5GPa, while the modulus of elasticity of FR4 is 10 times higher. The lower modulus of elasticity means that FPCs are more susceptible to elastic deformation when subjected to force, making it difficult to maintain precise dimensions and shapes.
High CTE (Coefficient of Thermal Expansion) performance: In the X/Y direction, FPC has a CTE value of 12 – 20 ppm/°C, and as high as 50 ppm/°C in the Z direction. This means that FPCs undergo large dimensional changes when the temperature changes, posing a serious challenge to precision control during the soldering process.
Surface unevenness: In the free state, the warpage of FPC may reach ±1.5mm/m. This surface unevenness makes it difficult for FPC to achieve precise fit with soldering equipment and other components, affecting the quality of soldering.
Five core functions of the fixture
Precise deformation control: The special fixture can strictly control the warpage of FPC within ±0.1mm. Through reasonable structural design and clamping method, the elastic deformation of FPC is effectively suppressed to ensure that it maintains a flat and stable shape during the welding process, providing the basis for high-quality welding.
Highly efficient and optimised heat transfer: During the soldering process, the carrier ensures that the temperature difference between the FPC board surfaces is less than 3°C (in the peak temperature zone). Uniform heat transfer helps to avoid soldering defects caused by locally too high or too low temperatures, such as false soldering and cold soldering, and improves the consistency and reliability of soldering.
Precise and error-free positioning: The fixture provides ±0.05mm mechanical positioning reference to ensure the positional accuracy of the FPC during the soldering process. Accurate positioning can make the soldering point and component pins accurately aligned to ensure the quality of welding, improve the electrical performance and stability of the product.
Comprehensive protection against static electricity: The surface resistance of the fixture is controlled at 10⁶ – 10⁹Ω, which realises ESD (electrostatic discharge) safety protection. In the electronic manufacturing process, static electricity may cause damage to sensitive electronic components, the special carrier’s electrostatic protection function can effectively avoid this situation, to protect the quality of components and products.
Highly compatible with the process: the special fixture can adapt to the cleaning, printing, SMD, reflow and other full-flow process. In the production process, FPC needs to go through a number of processes, the fixture design can ensure that the FPC in each process can be stable support and positioning, improve production efficiency and product quality.
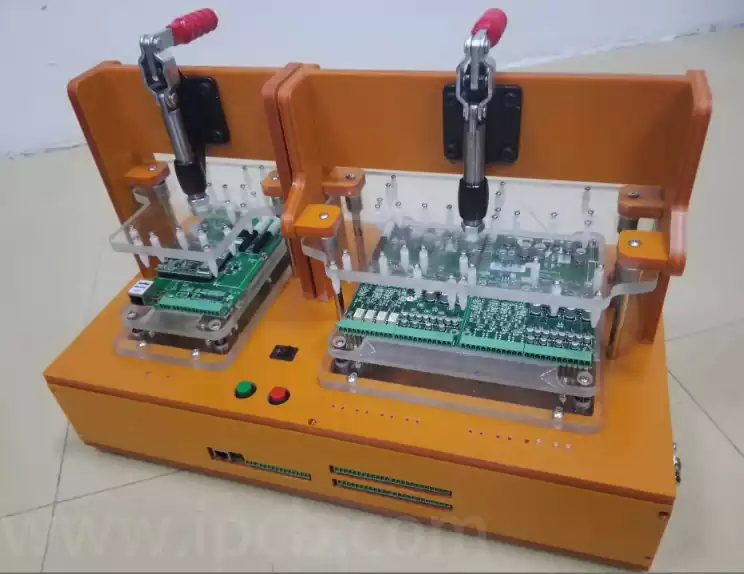
In the manufacturing process of FPC (Flexible Printed Circuit), the production of special fixtures is crucial. The basis for its production for the circuit board CAD files, through the reading of FPC positioning holes in the file data, and then create high-precision FPC positioning templates and over-furnace fixtures. In the production process, we need to ensure that the positioning template positioning column diameter and the positioning holes on the furnace fixture, as well as the positioning holes of the FPC itself to accurately match.
Consideration of FPC characteristics and the adaptation of the overfurnace fixture
The thickness of many FPCs is not uniform for the purpose of protecting circuits and meeting design requirements. Moreover, in order to enhance the hardness and facilitate assembly and fixation, FR4, aluminium reinforcement and even steel reinforcement will be added. In more specific cases, multiple reinforcements may be used at the same time, and the thickness of each reinforcement varies. In view of this, the furnace fixture needs to be based on the actual situation of grinding groove processing, the main purpose is in the printing and patch link, to ensure that the FPC can be in the same plane, so as to protect the accuracy and quality of production.
Furnace fixture should have a light, thin, high strength, less heat absorption, heat dissipation and other characteristics, and in the experience of many thermal shock, the deformation should be small, the degree of distortion should be low. At present, the commonly used carrier materials cover synthetic stone plate, aluminium plate, alloy plate, silicone plate and so on.
Characteristics of various carrier materials:
Synthetic stone plate fixture (commonly used)
Advantage: Easy design process, fast proofing and very easy to operate. Its service life is about 4000 – 7000 times between, good stability, not easy to absorb heat, the use of the process will not be hot, the price is also more affordable.
Shortcomings: fixture and FPC in the heat absorption there is a certain degree of asynchrony phenomenon (but the difference is not very significant).
Aluminium sheet fixture (not recommended)
Advantage: fast heat absorption, small temperature difference between inside and outside, can achieve synchronous heat absorption with FPC, and deformation can be repaired by simple methods. In addition, it is cheap and has a long service life.
Shortcomings: in the process of use will be hot, the operator needs to wear heat-insulating gloves or double-layer labour gloves to pick up, and relatively easy to deformation.
Alloy material jig (recommended)
Advantage: As an emerging over-furnace jig in recent years, it has been widely recognised by the industry. It has the advantages of fast heat absorption, small temperature difference between inside and outside, synchronous heat absorption with FPC, not easy to deform, etc. The price is comparable with synthetic stone, and the service life can reach more than 15,000 times (except for special circumstances).
Shortcomings: the same problem of hot hands, operators need to wear heat-insulating gloves or double-layer labour gloves for operation.
Silicone sheet fixture (not recommended)
Advantage: Self-adhesive, FPC can be directly pasted on it without the use of adhesive tape, it is also very convenient to remove, and will not leave residual adhesive, and can withstand high temperatures.
Shortcomings: with the use of time, its viscosity will gradually decline, the service life is shorter, probably between 1000 – 2000 times, and the price is relatively high.
Dedicated fixture for FPC SMT production to build a solid foundation of quality. With the evolution of technology, the carrier will be in the optimisation of performance, enhance the adaptability of breakthroughs, a powerful impetus to the FPC industry to a higher level.