In the context of the rapid development of 5G communication technology, the performance of high-frequency PCB board has become the key to ensure the quality of signal transmission and system stability. Traditional FR4 materials are widely used in all kinds of electronic products for their excellent cost performance, while Rogers and other high-frequency specialised materials show irreplaceable advantages for high-frequency signal transmission. Through the rational design of the six-layer hybrid platen structure, combined with the characteristics of different materials, can effectively improve the efficiency of high-frequency signal transmission, to meet the diversified needs of applications from the base station to the terminal equipment.
FR4: A cost-effective general-purpose material
FR4 is the most common PCB board and is widely used in consumer electronics, communications, and computers. It is a composite of glass fibre and epoxy resin with good electrical insulation properties and mechanical strength, and FR4’s temperature resistance and chemical stability also make it suitable for most low and medium frequency applications. Jadobond’s selection of FR4 materials is strictly controlled to ensure high thermal stability and tensile strength, as well as compliance with RoHS environmental requirements. However, the poor thermal conductivity of FR4 limits its performance in high frequency and high power applications.
Rogers: The Material of Choice for High Frequency Applications
In high frequency and high speed applications, Rogers materials have become the material of choice for many high-end products due to their excellent electrical properties and low loss characteristics. Rogers substrates have a low dielectric constant (Dk) and a low loss factor (Df), which allows them to excel in high speed circuits and RF circuits, and can effectively reduce signal attenuation and distortion.
Dk/Df matching design strategy for six-layer pcb boards
- Material selection and layering planning
Signal layer assignment:
High-frequency signal layer: use Rogers RO4350B (Dk=3.48) with Df≤0.0037 to suppress high-frequency loss.
Power/ground layer: use high Tg FR4 (Tg≥170°C) to balance cost and thermal stability.
- Inter-layer coupling optimisation:
The spacing between the signal layer and the reference plane is controlled at 5-10mil to reduce the risk of planar resonance.
The power supply layer and ground layer are tightly coupled (spacing ≤5mil) to reduce EMI radiation.
- process parameters control
Etching accuracy:
Rogers sheet using laser direct forming (LDS) technology, line width tolerance ± 5μm; FR4 need to compensate for side-etching effect (etching factor 1.2-1.5).
Lamination process:
Vacuum lamination pressure ≤ 200psi, resin flow 25%-35%, to avoid media delamination resulting in Dk/Df drift.
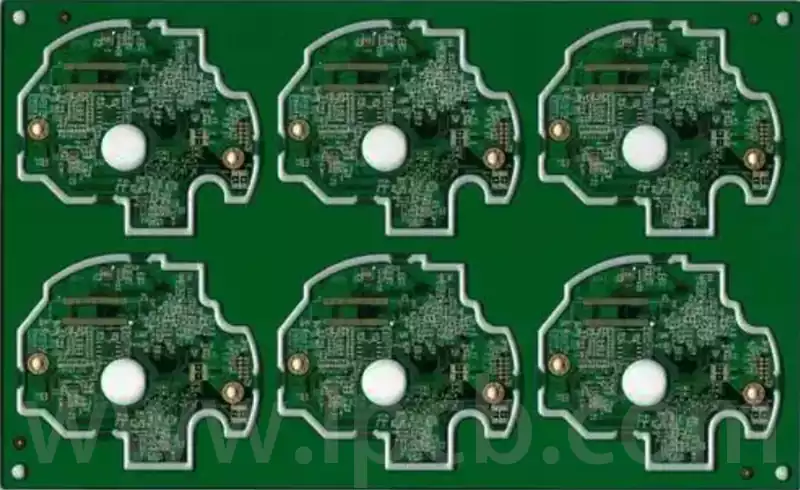
Performance Advantages of HF/Hybrid PCBs: Paving the Way for 5G Signals
The core difference between HF/Hybrid PCBs and traditional PCB boards lies in the precise control of the transmission characteristics of high-frequency signals. The dielectric constant (Dk) of high-frequency boards is usually controlled between 3.0 and 3.8, and the change rate with frequency (1GHz to 100GHz) should be less than 0.2, which means that the speed deviation of the signal propagating through the pcb board can be controlled within 5 per cent, thus avoiding the signal delay due to fluctuation of the dielectric constant. By combining high-frequency materials with ordinary FR-4 materials in a layered fashion, the mixed-pressure sheet meets the low-loss requirements of critical signal links while reducing overall costs, balancing performance and economy.
In terms of signal loss, the dielectric loss angle tangent (Df) of high-frequency sheet can be as low as 0.002 or less at 10GHz, which is 1/10th of that of traditional FR-4 sheet (Df ≈ 0.02), which means that the signal attenuation per metre can be reduced by 80% in the signal transmission link of a 5G base station to ensure that millimetre-wave signals can be transmitted over longer distances. A test data shows that in the 28GHz frequency band, the signal strength of PCBs with high-frequency plates after 10 metres of transmission is 25dB higher than that of ordinary plates, which is equivalent to a 300-fold increase in signal power.
In addition, the coefficient of thermal expansion (CTE) of the high-frequency/mixed-pressure sheet matches that of the copper foil more closely, and the CTE in the Z-axis direction can be controlled to be less than 50ppm/°C in the temperature range from -55°C to 125°C, which effectively reduces the risk of line breakage due to temperature changes, which is crucial for scenarios with a large difference in temperature, such as outdoor 5G base stations.
Typical application scenarios in 5G communications: full link protection from base station to terminal
The RF unit (RRU) of a 5G macro base station is the core of signal processing, and needs to handle multi-channel, high-frequency-band signals. high-frequency/mixed-pressure sheet PCBs produced by six-layer PCB board factories are layered with RF links and digital control links, and high-frequency sheets are used in the RF portion (Dk=3.4, Df=0.0018), while ordinary FR-type PCBs are used in the digital portion. The RF part uses high-frequency PCB (Dk=3.4, Df=0.0018) and the digital part uses ordinary FR-4, which not only ensures the low-loss transmission of RF signals, but also reduces the material cost by 30%. In the actual test, the PCB of this mixed-voltage structure improves the signal spurious rejection ratio of RRU by 15dB, which ensures the purity of the signal of the base station.
As the key equipment for 5G indoor coverage, small base stations are small in size but require high signal transmission efficiency. The low-loss characteristics of high-frequency boards make them indispensable for small BTSs. For example, in small BTSs in the 3.5GHz band, PCBs with high-frequency boards can increase signal transmission efficiency by 20% and extend the coverage area by 15%, thus solving the problem of indoor signal dead corners. Six-layer PCB board factories optimize the stacking structure of boards and tightly couple the signal layer with the grounding layer, so as to increase the anti-jamming ability of small BTSS. In an office building environment where multiple devices work simultaneously, the communication interruption rate is reduced to less than 0.1%.
5G terminal devices such as smartphones and industrial modules require high-speed signal transmission in a limited space. Mixed-pressure boards play an important role here. Taking the motherboard of a 5G mobile phone as an example, the six-layer PCB board factory uses high-frequency boards (Dk=3.2) for the millimeter-wave antenna link and conventional materials for the other links, which reduces the thickness of the motherboard by 0.2mm while ensuring that the millimeter-wave signal transmission loss is less than 0.5dB/cm and contributes to the thinness and lightness of the mobile phone. Tests show that the download rate of 5G mobile phones using this solution in the millimetre-wave band is 12% higher than that of using ordinary boards, and the latency is reduced by 8ms.
High-frequency and mixed-voltage PCB boards play a crucial role in the whole link of 5G communication. Reasonable material selection and stacking design not only significantly reduce signal loss and electromagnetic interference, but also improve the thermal stability and reliability of the system. As technology continues to advance, PCB solutions combining high-performance materials and precision processes will provide a solid guarantee for future high-speed and stable 5G networks, driving the communications industry to a higher level.