PCB cleaning is an important processing procedure in SMT SMD processing, strictly in accordance with the requirements of the implementation can be removed in the electronic processing of some of the pollutants generated, such as flux, solder paste, adhesives, etc., a good cleaning process can protect the board in the use of the stability and reduce the failure rate and so on.
Importance of printed circuit board assembly cleaning
Remove flux residues, tape paper or solder resist film residue, dust, grease, particles and sweat and other pollutants, to prevent corrosion of components, printed wires and solder joints and other defects, to improve the performance and reliability of components;
Remove the hazards of corrosive substances to ensure the smooth progress of component electrical performance testing, solder joints too much flux residue will make the test probe can not be good contact with the solder joints, thus affecting the correctness of the test results;
Contaminants on the surface of the component can hinder the bonding of the coating layer;
To make the component appearance clear, thermal damage and layer cracks and other defects leak out, in order to detect and troubleshooting.
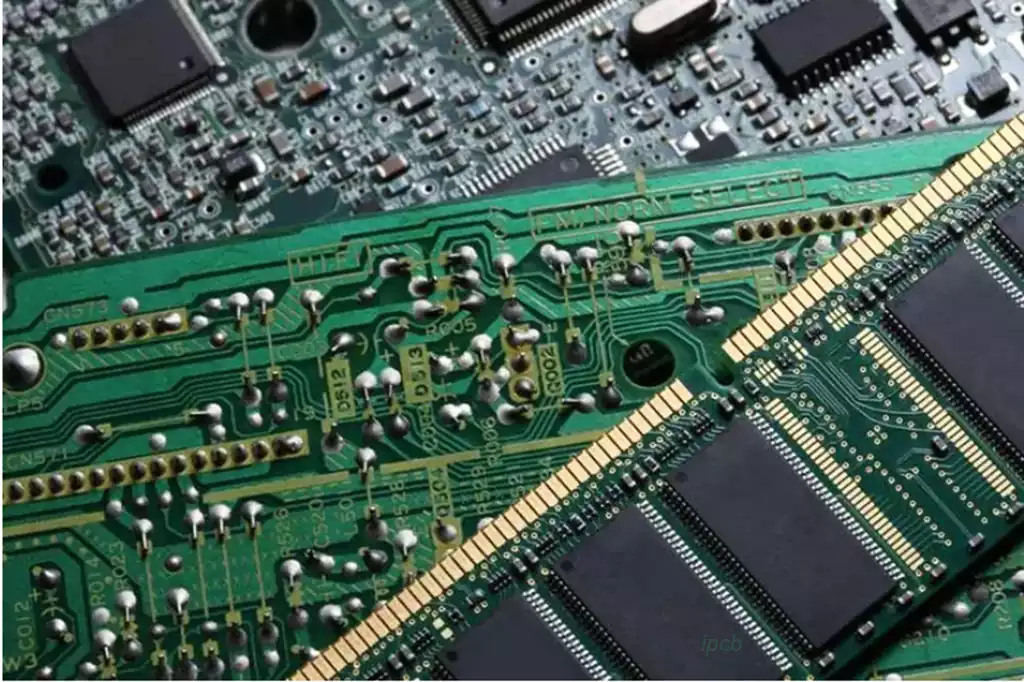
how to clean a pcb
The current pcb cleaning, mainly through ultrasonic waves, but some components on the pcb board, such as crystal and so on, have a metal shell, after cleaning, it is difficult to component inside the moisture drying. The principle of using ultrasonic cleaning is: the flux residue cleaning, mainly through the dissolving effect is completed. Whether it is rosin or organic acids and their tin or lead salts, in the cleaning agent have a certain solubility, through the transfer of the process from the board to the cleaning agent to complete the removal of residues.
Particulate contaminants: Dust, lint and solder balls. Solder balls are a soldering defect that can cause electrical shorts if the vibration of the equipment causes a large number of small solder balls to collect on one part. Solder balls can be removed by cleaning. Non-polar contaminants: rosin resins, paraffin wax, and antioxidant oils used in wave soldering, as well as cosmetics or hand sanitizers left behind by the operator. Polar contaminants: halides, acids and salts.
Hazards of circuit board contamination: Particulate contaminants – electrical short circuits. Polarized contaminants – dielectric breakdown, leakage, component/circuit corrosion. Non-polar contaminants – cosmetic effects, white powder spots, dust adhesion, poor electrical contact.
Circuit board cleaning methods: ordinary cleaning mainly use a single cleaning tank, need to clean the PCB substrate in the cleaning agent liquid immersion cleaning. The temperature of the cleaning agent in the ultrasonic cleaning machine is generally 35 ℃ ~ 85 ℃, cleaning time 2 ~ 5 minutes. For the usual cleaning agent can be used liquid phase cleaning. Vapor phase cleaning means that the machine constitutes at least three tanks, of which the first tank is thermally cleaned, the second tank is frozen and immersed, and the third tank is rinsed with boiling vapor. The third tank cleaning agent liquid is heated to produce a vapor, in the encounter frozen immersion after the cryogenic workpiece is cooled into a liquid drop tank, will get a fairly clean workpiece. So that circuit board in the clean cleaning fluid washed out after the surface will be relatively clean. Suitable for this equipment cleaning agent is mainly trichloroethylene and other non-flammable single or mixed liquids. This is for more demanding PCB circuit ultrasonic cleaning equipment.
The cleaning of printed circuit boards is an integral part of the production process. This is due to the fact that various chemicals, solvents and other processes are used during the manufacturing of circuit boards and these substances may remain on the surface or inside the board. These residues can lead to unstable board performance, such as short circuits, leakage, electrical adhesion and other problems, which in turn have a negative impact on overall quality. At the same time, cleaning circuit boards also effectively removes dust, dirt, oil and other impurities from the surface, thereby optimizing soldering results and enhancing the reliability and stability of the board.