Low cost PCB boards are printed circuit boards whose production and assembly costs have been reduced by optimizing the design and production process. Such PCBs still maintain relatively high standards of performance and reliability and are suitable for use in a variety of consumer electronics, industrial equipment and other applications. The realization of low cost depends not only on the choice of raw materials, but also on improvements in manufacturing processes and production scale.
The cost of pcb influences
- Material selection
PCB materials used have a significant impact on the cost. Different types of materials (such as FR-4, CEM-3, etc.) in the price and performance differences, and the thickness of the material and the thickness of copper will also affect the price. In terms of solder resist ink, the price difference between ordinary thermosetting oil and photographic green oil will also lead to changes in the overall cost. - PCB layers
The number of PCB layers is an important factor affecting the cost. Usually, under the same area, the more layers, the higher the production cost, because the complexity of the manufacturing process increases. Therefore, designers need to make a balance between signal quality and cost. - Production Process
Different production processes will directly affect the cost of PCB manufacturing, such as gold plating and tin spraying, milling and punching the board and other process choices will lead to different costs. At the same time, advanced processes may require more resources and time, thus increasing manufacturing costs. - Manufacturing Difficulty
PCB complexity and manufacturing difficulty is also a cost factor. If there are special design requirements on the circuit board, such as small apertures or fine line widths, higher processing costs are usually required. The higher the difficulty, the scrap rate may also increase, further increasing manufacturing costs. - Customer requirements
Customer requirements for a product can also affect costs. Demanding customers often require higher yields, which may require manufacturers to invest more time and resources to meet these expectations. For example, manufacturing to different standards can have a direct impact on costs. - Geographic location
The geographic location of PCB production also has a significant impact on costs. Labor costs, transportation costs and other factors in different regions can lead to price differences, usually in the south of the relatively low cost of production, while the northern region is higher. This also affects the price quoted by manufacturers in different regions.
Ways to reduce pcb cost:
- Optimize design
At the design stage, optimizing the PCB layout can effectively reduce the wiring length and number of layers, avoiding the use of unnecessary special processes, thereby reducing material and processing costs. The use of automated design tools for design rule checking (DRC) can also further improve design efficiency and reduce the error rate. - Material selection
Selection of cost-effective materials is an important part of PCB cost control. Under the premise of ensuring product quality, reasonable selection of materials such as substrates and copper foils can greatly reduce procurement costs. Accurate calculation of the size of the required materials to reduce the generation of scrap is also an effective way to reduce costs. - Improve production efficiency
By optimizing the production process, we can significantly improve production efficiency and reduce the rate of defective products. Reducing processing difficulty and increasing line width and spacing can improve productivity and reduce potential problems in production, thus reducing overall costs. - Reduce the number of layers and holes
Reasonable use of multilayer board design, in order to meet the functional requirements of the premise, as far as possible to reduce the number of layers and the number of holes in the PCB, which can reduce the amount of material used and processing difficulties. Simplify the circuit design, so that the complexity of the circuit board is reduced, is also an effective way to reduce costs. - Increase Volume Production
Spreading the fixed cost through mass production means that the unit cost will be lower.Mass production not only increases the efficiency of production, but also allows for more competitive pricing with material suppliers.By increasing the number of units produced,the overall economic efficiency can be effectively improved.
Low cost PCB boards typically have the following distinguishing features:
Standardized design: Using standard components and materials reduces material procurement costs and inventory pressures,thereby reducing overall production costs.
Automated Production:Increase production efficiency, reduce labor costs, and lower production error rates by automating production processes.
Scale production:Sharing fixed costs through mass production, resulting in a significant reduction in unit cost per PCB.
Adaptable:The design can be flexibly adapted to meet the needs of a wide range of products according to different application requirements.
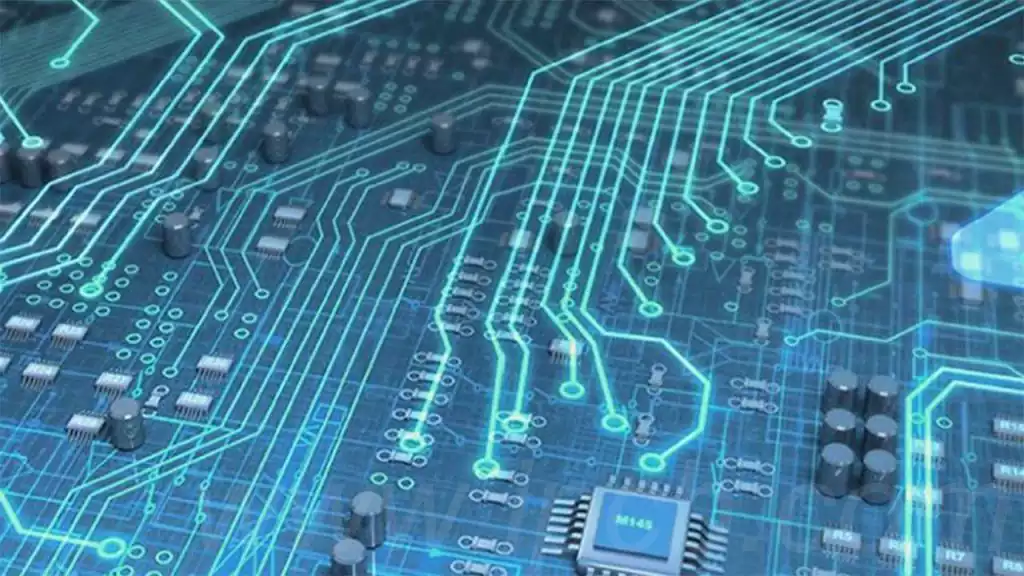
Low cost PCB boards usually have only one conductive layer, one side for component mounting and the other side is a copper foil layer. This design keeps the cost down and is mainly suitable for simple electronic products such as remote controls and LED lights. This type of PCB board is particularly suitable for simple circuits and low complexity application scenarios. They are widely used in consumer electronics due to their ability to fulfill everyday needs while ensuring reliability. The manufacturing process of low-cost PCBs is relatively simple, which helps to increase productivity. By reducing complexity, manufacturers are able to quickly produce boards that meet a large number of requirements, thereby reducing production time.
The most commonly used substrate materials in low cost PCB boards manufacturing are FR-4 and CEM-3.FR-4, which is based on a glass fiber reinforced resin, has good electrical properties and mechanical strength,and its cost is lower than most other options,making it well suited for most PCB types.CEM-3 has high thermal stability and mechanical strength, and it is also relatively low in cost, making it suitable for single,double-sided and multilayer circuit boards.
Low cost PCB boards are used in a wide range of applications and excel especially in cost-sensitive industries.Common application scenarios include:
Consumer electronics:such as cell phones,headphones,home appliances, etc., low-cost PCBs help companies to reduce the overall product price and enhance market competitiveness.
Automotive electronics: In automotive sensors and control systems, low cost PCB boards provide cost-effective solutions while ensuring the safety performance of vehicles.
Medical Devices: Low-cost PCBs enable many medical devices to be produced at a lower cost, thus enabling high-quality medical devices to be used by more people.
Industrial Controls: In industrial automation equipment, the use of low-cost PCBs helps to reduce the overall cost of system development and manufacturing.
The process of producing low cost PCB boards often involves multiple steps, and costs are reduced by optimizing these steps:
Design phase: Reduce design costs by using simplified designs as well as standardized components to reduce unnecessary complexity.
Material selection: Use cost-effective materials, such as FR-4 and other common PCB materials, to ensure functionality and control costs.
Automated production: Introduce automated production lines to improve production efficiency and reduce labor costs and error rates.
Scale production: Share fixed costs through mass production, making the production cost of a single PCB significantly reduced.
Development trend of low cost PCB boards
- Growing market demand
The market demand for low-cost PCBs (Printed Circuit Boards) is growing steadily, especially in areas such as consumer electronics, automation and the Internet of Things. With the popularity of smartphones, wearable devices, and home-intelligent products, the demand for cost-effective and reliable PCBs continues to climb. This makes low-cost PCBs an important choice for companies to realize economic benefits. - Application of advanced materials
With technological advances, low-cost PCB manufacturing will be more use of new environmentally friendly materials, such as lead-free materials and biodegradable materials. This not only meets the environmental requirements, but also reduces production costs and meets the global market demand for green manufacturing. For example, the use of low dielectric constant and low-loss materials can help improve PCB performance and reduce power consumption, enhancing the competitiveness of the product market. - Manufacturing process optimization
Future low cost PCB boards production process will be more optimized, traditional manufacturing methods will be combined with emerging technologies to form a new manufacturing model.Automation and refinement of production will be more common,companies will introduce efficient automation equipment and processes, such as automated testing, automatic drilling and copper plating technology.These improvements can reduce labor costs and increase productivity. - Simplification of design parameters
In order to effectively control costs, PCB design will tend to simplify. Under the premise of meeting functional requirements, designers will reduce the number of PCB layers, the number of components and wiring complexity. This design approach not only reduces manufacturing costs, but also accelerates the production cycle. - Popularization of mass production
The production of low cost PCB boards will rely more on mass production. Through standardized design and material selection, companies are able to share the fixed costs in mass production, thus significantly reducing the unit cost of each PCB. This model not only improves production efficiency, but also enhances market competitiveness. - Environmental protection and sustainability
Environmental protection and sustainability will play an increasingly important role in the production of low-cost PCBs. In the future, manufacturing companies will emphasize green manufacturing and adopt energy-saving and environmentally friendly production processes to reduce environmental impact and enhance social image. For example, maintaining good resource recycling and waste management strategies will become an important way of operation. - Personalization and Customization Demand
With the diversification of market demand, personalization and customization of low-cost PCBs will gradually increase. Manufacturing companies need to flexibly respond to market changes, according to different customer needs to provide customized solutions to enhance customer satisfaction and market responsiveness.
In today’s highly competitive electronics market, low cost PCB boards has become a popular choice for electronic product development due to its cost-effective advantages. It not only effectively reduces production costs,but also enhances product market competitiveness and development efficiency. With the continuous progress of technology,it will continue to promote innovation and popularization in the future, bringing more business opportunities to various industries.