SMD soldering paste is a kind of soldering material specially used in surface mount technology (SMT). In the SMT process, solder paste plays the role of adhering to components, promoting solder wetting, removing oxides and impurities, protecting the surface from re-oxidation, and forming a strong metallurgical bond. Solder paste printing is the first process of SMT, and its quality directly affects the subsequent placement, reflow soldering, cleaning, testing and other processes, and determines the reliability of the product.
SMT dedicated solder paste composition is generally divided into these two categories, namely, solder powder alloy and flux.
The combination of alloy powder material and role:
Solder powder alloy is the core combination of solder paste, accounting for at least 85% to 90% of the total quality of the paste. More common alloy combinations are the following categories: tin-lead alloy (Sn-Pb), tin-lead-silver (Sn-Pb-Ag) alloy, tin-copper alloy (Sn-Cu), tin-silver-copper alloy (Sn-Ag-Cu), tin-bismuth alloy (Sn-Bi), tin-bismuth-silver alloy (Sn-Bi-Ag) and so on.
Alloy powder material of the effective composition, ratio, particle size are oxidized layer relative to the solder paste in terms of direct impact.
When the alloy content is relatively high, can ease the collapse of the solder paste, conducive to promote the composition of full bright solder joints, and because the flux content with the alloy content continues to improve and change, so the post-solder residue is also reduced, you can effectively prevent the presence of tin beads, however, the disadvantage is that the printing and soldering process requirements related to the increasingly stringent requirements.
When the alloy content is relatively low, the printing performance will be very good, solder paste is not easy to stick to the scraper, good wettability, leakage board durable, production and processing will be easier, but the disadvantage is easy to collapse, easy to produce tin beads or bridging and other defects.
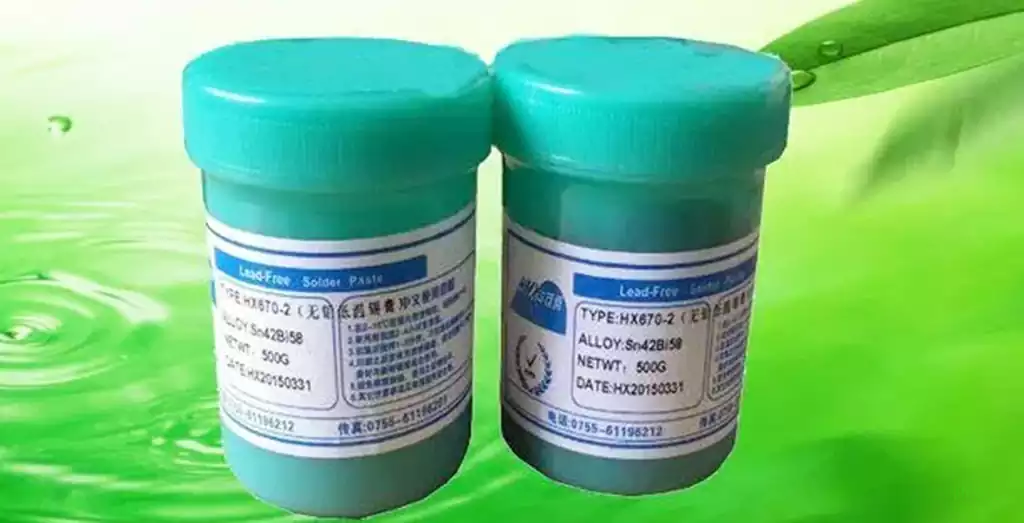
The use of soldering paste and storage
- Storage method
The storage of solder paste should be controlled at 1-10℃; the service life of solder paste is 6 months (unopened); it should not be placed in the sun. - Usage (before opening)
The temperature of the solder paste must be raised to the ambient temperature (25±2°C) before opening, and the temperature recovery time is about 3-4 hours. Prohibit the use of other heaters to instantly raise the temperature. Mix thoroughly after reaching the ambient temperature. Mixing time is 1-3 minutes, depending on the type of mixer. - Usage (after opening)
Add approximately 2/3 of the solder paste to the stencil and try to keep no more than 1 can on the stencil.
Depending on the production speed, solder paste on the stencil should be added in small quantities to maintain the quality of the paste.
The unused soldering paste of the day should not be kept with the unused solder paste but stored in a separate container. It is recommended that solder paste be used within 24 hours at room temperature after opening.
For the next day’s use, the newly opened solder paste should be used first, and then the unused solder paste and the new solder paste should be mixed at a ratio of 1:2, adding small amounts several times.
After the solder paste is printed on the substrate, it is recommended to finish soldering the parts in the reflow oven within 4-6 hours.
Please scrape off the solder paste on the steel plate first and put it into the solder paste tank before changing the wire for more than 1 hour.
Due to airborne dust and other contamination, please follow “Step 4” after 24 hours of continuous solder paste printing to ensure product quality.
To ensure print quality, it is recommended to manually wipe the openings on both sides of the steel plate every 4 hours.
Maintain the room temperature at 22-28℃ and humidity at RH30-60% for the best working environment.
To wipe the misprinted substrate, it is recommended to use industrial alcohol or industrial cleaner.
How to choose the right solder paste
Soldering material
First you need to determine the material to be soldered, such as metal, plastic, etc.. Different materials need to use different types of solder paste, otherwise the effect will be greatly reduced. For metal materials, you can choose silver-containing soldering paste or copper-containing soldering paste; while for plastic materials, you need to use specialized soldering flux.
Required temperature
Different types of solder pastes require different temperatures for optimal soldering results. Therefore, when selecting a solder paste, it is necessary to determine the required soldering temperature and select the corresponding solder paste product. At the same time, you also need to pay attention to temperature control when using the solder paste to avoid burning the solder material or causing safety accidents.
Environment
The environment in which the soldering takes place is also an important factor in the selection of solder paste. For example, if the air humidity in the soldering environment is large, you need to choose a solder paste with moisture resistance; if the soldering environment is more severe, you need to choose a better anti-corrosion performance of the solder paste.
SMD soldering paste, as a key material in the SMT process, its selection, use and storage are directly related to the quality and reliability of the product. Understanding the composition and characteristics of solder paste and its performance under different conditions is the key to ensure that the soldering process runs smoothly. At the same time, following the correct storage and use methods can effectively extend the service life of solder paste and reduce waste and failure in the production process.