In the electronics industry, flexible connection technology has always been a key link, FFC vs FPC as two common flexible connection solutions, each with unique advantages and application scenarios.
The difference between FFC vs FPC:
Structure: FFC (Flat Flexible Cable) is a flat flexible cable, usually composed of metal foil and insulation, through the conductive adhesive and conductive adhesive connection circuit, with a thin, flexible, bend-resistant, fast transmission speeds.FPC (Flexible Printed Circuit) is made of polyimide film made of flexible FPC (Flexible Printed Circuit) is a flexible circuit board made of polyimide film, whose circuit pattern is formed on the surface of polyimide film by etching technology, with good flexibility and foldability.
Performance Comparison
Due to their different structural characteristics, FFCs and FPCs exhibit their own unique performance characteristics.FFC stands out for their excellent flexibility and excellent folding resistance, making them easy to bend and fold in confined spaces, making them particularly suitable for complex and variable electronic devices. In addition, FFC’s large number of conductors and compact spacing give it a significant advantage in high-density circuit connections.
In contrast, FPC’s strengths lie in its multi-layer circuit design and complex circuit layout capabilities. This design allows FPC to realize higher circuit integration and more complex circuit functions. What’s more, by alternately stacking conductor layers and insulating layers, FPC effectively reduces electromagnetic interference (EMI) and crosstalk problems, thus significantly improving the quality of signal transmission.
Application Comparison
Due to the differences in performance and structure, FFC and FPC also show significant differences in application, FFC is mainly used to connect circuit boards between electronic devices, such as computers, communication equipment, medical equipment and industrial control equipment. Its excellent flexibility and folding resistance make it easy to cope with a variety of complex equipment layout and space constraints.
FPC, on the other hand, is more often used in the manufacture of flexible circuit boards in a variety of electronic devices, such as cell phones, tablet PCs and wearable devices. With its multi-layer circuitry and complex circuit layout capabilities, FPC is able to realize higher circuit integration and more complex circuit functions, bringing thinner, more efficient and multi-functional designs to electronic devices.
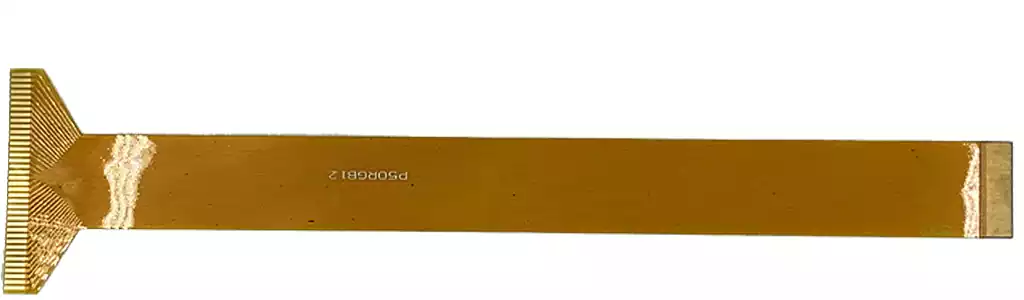
The connection between FFC vs FPC:
Material Characteristics: The substrates of FFC and FPC are both flexible, which allows them to be easily bent and folded to adapt to a variety of complex installation environments.
Conductivity: The conductors of FFC vs FPC is mainly composed of copper, tinned copper or gold-plated copper, which give them excellent conductivity and ensure stable and efficient current transmission.
Precision requirements: Both FFCs and FPCs are capable of accurately producing complex circuit patterns, so they excel in application scenarios that require high-density connections.
Performance Parameters: While the specific parameters and performance of FFCs and FPCs may vary from product to product and manufacturer to manufacturer, the following aspects are typically covered:
Thickness: The common thickness of FFCs and FPCs ranges from 0.1mm to 0.2mm, but can be customized to meet actual needs.
Number of wires: Both materials can be designed to meet demand, and the number of wires can vary from a handful to hundreds.
Electrical Characteristics: Electrical properties cover conductivity, insulation, impedance and many other aspects, the specific parameters need to be evaluated according to product needs and design requirements.
Operating temperature: FFCs and FPCs are usually able to operate normally within a temperature range of -40°C to +85°C, but some special products can also be adapted to a wider temperature range.
Reliability testing: To ensure that FFCs and FPCs do not break or break wires during use, they are usually subjected to reliability tests such as pressure, number of bends, and tensile strength.
With the continuous development of electronic technology, flexible connection technologies such as FFC vs FPC will continue to play an important role. In the future, we can expect more innovations and breakthroughs to meet the ever-changing needs of electronic devices and systems.