The choice of moulding process for flexible board directly affects product quality and production efficiency. According to the product demand, accuracy requirements and production volume, manufacturers need to reasonably select the moulding method. In this article, we will introduce in detail the characteristics and application scenarios of the three main moulding processes.
1.Die-punching moulding process
Die-punch moulding is the most commonly used moulding method in FPC mass production. The process uses precision moulds for punching and cutting, which has the characteristics of high efficiency and good consistency. The selection of moulds is mainly based on material, precision and production requirements.
Moulds are divided by material, there are steel moulds and knife moulds. Steel mould is made of steel, high precision, stamping times, not easy to deform, is commonly used moulds, because of its heavier weight, often need to move when the device, and higher costs, therefore, the steel mould is generally not manufactured too large, suitable for veneer size within 600mm flexible board punch shape; knife mould quality is light, low cost, made of wood and steel blade, precision is not high, generally only for the shape of the accuracy of the requirements of not strict products and accessories. Generally, it is only suitable for the products and auxiliary materials which do not require strict shape accuracy, such as reinforcement pieces, etc. (We will not discuss the knife mould again, and the said moulds refer to the hardware and steel moulds).
According to the precision points, there are fine mould, general mould, simple mould points, which involves three kinds of mould production methods, slow walking wire, in the walking wire, fast walking wire; through the slow walking wire made of moulds, for fine mould, its precision servitude ± 0.05mm, steel quality is good, not easy to deformation, but the price is high, the manufacture of time is longer, unless the customer on the shape of the precision of ± 0.05mm special requirements, generally do not use this kind of Mould; through the wire made of the mould, for the general mode, its precision servitude ± 0.10mm, precision can meet most of the needs, the price is moderate, stable function, for the usual selection of the open-mould varieties; through the wire made of the mould, i.e., the simple mode, precision in ± 0.2mm, the price of the general mode is slightly cheaper, the general requirements for the shape of the shape of the low servitude of the product is to select this method of opening the mould; steel mould by the upper mould and the lower mould composition, the lower mould for the shape of ± 0.05mm special requirements, generally do not choose this kind of mould; steel mould by the upper mould The steel mould is composed of upper mould and lower mould, the lower mould is the base and the upper mould is the punching and cutting mould. The mould will be installed to the punch press, the need to use the test plate on the mould of the stamping height adjustment, used to select the appropriate stamping strength, to ensure that the flexible board can be cut according to the shape of the planning diagram, together with no damage to the FPC other parts that do not need to be punched. According to the size of the FPC, the mould is often one out of many methods, that is, stamping once, forming a number of FPC, and then improve the production power. In the production process, under the premise of not changing the FPC shape planning, the mould only needs to be manufactured once, and then can be recycled, suitable for mass production, reducing the unit production cost.
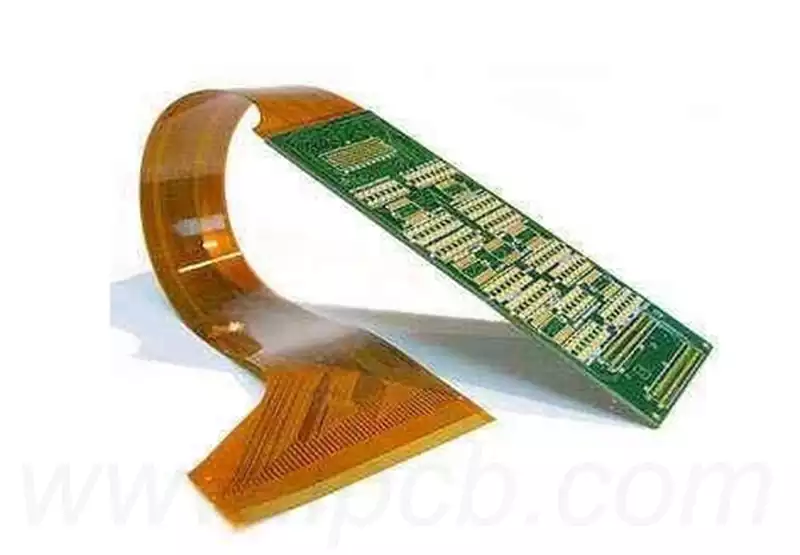
2.Cutting and moulding process
Cutting and moulding is mainly used for sample making and small batch production. The process includes CNC knife cutting and laser cutting in two ways, with strong flexibility and short preparation time.
CNC knife cutting uses mechanical tools for cutting, which has the problems of low precision and poor efficiency. Wear and tear of the tool will lead to an increase in burrs, affecting product quality. Currently the process has been gradually replaced by laser cutting.
Laser cutting uses a high-energy beam for processing, with an accuracy of ±0.05mm and a smooth and flat cutting surface. However, laser cutting may produce burn marks, which need to be followed by cleaning treatment. The process is suitable for sample production and rapid prototyping.
3.Hand forming process
Hand forming is the simplest way of forming, using scissors or knife and pen for manual cutting. The process is low cost, but the precision is poor and the consistency is difficult to ensure.
Hand moulding is only suitable for products with very low requirements on shape, or temporary processing of special shapes. Due to the difficulty of quality control, the process has been rarely used in regular production.
The choice of fpc moulding process needs to consider the product requirements, production volume and cost factors. Die punching moulding is suitable for mass production, cutting moulding is suitable for sample making, and hand moulding is only used for special occasions. As technology advances, new processes such as laser cutting are changing the way flexible board is moulded, providing more possibilities for flexible electronics manufacturing.