High Tg PCB significantly enhance their ability to withstand high temperature conditions by increasing their glass transition temperature (Tg). When the temperature rises close to or exceeds the Tg value of ordinary FR-4 materials, High Tg PCBs still maintain good rigidity and mechanical properties, ensuring that the circuit boards will not be softened or deformed by the heat generated during high-temperature processing or operation,thus maintaining stable electrical characteristics and long-term reliability.
High Tg printed circuit boards are characterized by the fact that when the ambient temperature rises to a specific threshold,the physical state of the substrate changes from a hard “glassy” state to a soft “rubbery” state,and the temperature at which this change occurs is defined as the glass transition temperature (Tg) of the board. The temperature at which this transition occurs is defined as the glass transition temperature (Tg) of the board.
In short, Tg is a measure of the maximum temperature (in degrees Celsius) at which a substrate material can maintain its structural rigidity.Conventional PCB substrate materials are susceptible to unfavorable phenomena such as softening, deformation and even melting under high temperature environments, accompanied by a significant decrease in mechanical strength and electrical properties, which will undoubtedly reduce the overall service life of the product. Generally speaking, sheets with a Tg value of 130°C or higher are considered to be of normal grade,while high Tg sheets generally have a Tg value of more than 170°C, and medium Tg is somewhere in between, about 150°C or higher.In particular,those PCB boards with Tg values at or above 170°C are explicitly categorized as high Tg printed circuit boards. As the Tg value of the substrate increases,the performance of the printed circuit board in terms of heat resistance, moisture resistance, chemical resistance and stability is significantly enhanced.Therefore,the Tg value is a direct reflection of the board’s ability to withstand high temperatures, especially in the lead-free manufacturing process, high Tg materials are more and more widely used. In short, high Tg means excellent heat resistance.
High TG pcb material are specialty PCB substrates with glass transition temperatures higher than traditional FR-4 sheets.According to different application requirements and manufacturing processes,common high TG sheets are mainly of the following types:
Halogen-free boards: These boards not only have a high TG value, but also do not contain halogen elements, in line with environmental requirements. In combustion will not produce toxic and harmful halogenated gases, which is conducive to environmental protection and resource recycling. Suitable for high-end electronic products with strict requirements for environmental performance.
Ceramic-filled sheet:By adding ceramic particles (such as alumino-silicate, aluminum nitride, etc.) to the resin matrix,the thermal conductivity and TG value of the sheet are significantly improved, while its mechanical strength and thermal shock resistance are enhanced. It is suitable for power devices, LED lighting, automotive electronics and other fields that require efficient heat dissipation.
Polyimide (PI) sheet: based on polyimide resin,it has a very high TG value (usually over 400°C) and excellent chemical resistance.Commonly used for high reliability circuits in extreme environments such as aerospace,military,and microwave communications.
PTFE (Polytetrafluoroethylene) Sheet:Known for its ultra-low dielectric constant and loss factor,as well as excellent high frequency performance.Despite its relatively low TG value (about 260°C),it is still considered a special type of high TG sheet for its unique electrical properties in areas such as RF,microwave,and millimeter wave communications.
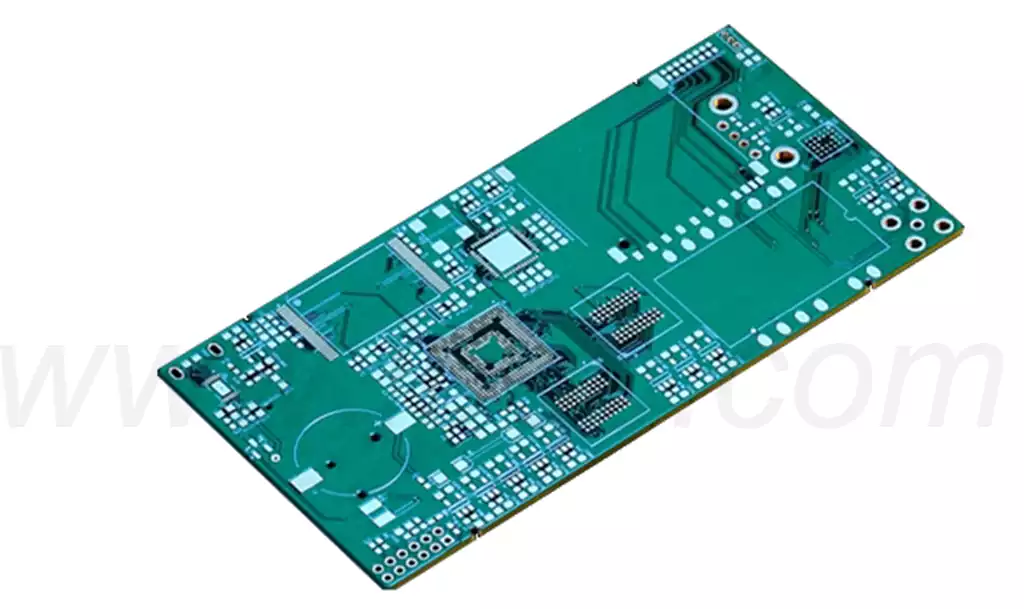
With a series of unique superiorities,High TG sheet stands out from the crowd in a wide range of applications,demonstrating extraordinary performance:
Extraordinary heat resistance:Compared with the traditional FR-4 sheet,the glass transition temperature of High TG sheet is significantly increased to over 170°C, and some of them can even exceed 400°C.This feature ensures that the sheet still maintains excellent thermal stability under high-intensity working environment,effectively resisting deformation and performance degradation,which lays a solid foundation for the long-term and stable operation of electronic equipment.
Excellent dimensional stability: even at high temperatures,it maintains a high degree of dimensional accuracy,which significantly reduces the risk of stress concentration in solder joints and interlayer peeling caused by differences in the coefficient of thermal expansion of the material,thus enhancing the overall assembly reliability and long-term durability of the circuit board.
Optimized Electrical Performance:In high temperature environments, the PCB exhibits excellent electrical characteristics with small resistivity fluctuations and highly stable dielectric constant and dielectric loss angle tangent, which helps to reduce the energy loss and delay phenomenon in the signal transmission process, and improves the high-frequency response speed of the circuit as well as the integrity and clarity of the signal transmission.
Excellent chemical resistance: Some high TG boards,such as polyimide-based boards,demonstrate excellent resistance to a wide range of acids, alkalis and organic solvents, maintaining stable electrical performance even in harsh chemical environments,which further extends the service life of PCBs and broadens their application areas.
Environmental protection and sustainability: With the increasing popularity of halogen-free high TG boards,this not only reflects the deep concern for environmental protection and human health, but also responds positively to the strict requirements of international RoHS,REACH and other environmental standards, contributing significantly to the green production and sustainable development of electronic products.
Why High Tg PCB
In order to achieve high Tg, manufacturers need to make more efforts, such as using high Tg resins, increasing glass fiber content, and implementing stricter manufacturing process controls. There is no doubt that these factors significantly increase the cost of PCB manufacturing. So why do we still use high Tg PCBs?
One obvious advantage is the improved heat resistance of the PCB. Conventional PCBs typically have Tg values between 130°C and 140°C.This means that under ideal conditions, PCBs can be operated below 140°C.However,in practice,we also need to consider the coefficient of thermal expansion,which refers to the expansion of the substrate due to temperature changes.Conventional PCBs typically have a coefficient of thermal expansion between 12 ppm/°C and 18 ppm/°C, which means that the actual operating temperature can be below 100°C.
In contrast, High Tg PCBs have a Tg value in excess of 170°C and a coefficient of thermal expansion between 5 ppm/°C and 8 ppm/°C. This means that High Tg PCBs can be used at temperatures in excess of 100°C and at temperatures in excess of 18 ppm/°C. This means that High Tg PCBs can operate at higher temperatures and are less affected by heat. This advantage makes high Tg PCB advantageous in high power density applications where there is a higher chance of heat generation. In standard PCB solutions, increasing board size is the way to improve heat dissipation and enhance thermal performance, but with High Tg PCB boards you can achieve the same performance without increasing size. This is in line with the miniaturization trend in the electronics industry. In addition, High Tg PCBs can be used to enhance the thermal performance of more compact and densely packaged circuits, such as multilayer PCBs and HDI PCBs.
High Tg PCB,with its excellent heat resistance,stability and environmental characteristics,has become a powerful driving force for innovation and development of the electronics industry, leading the future trend of technology.