What is a heat sink in PCB? A heat sink is a component made of a thermally conductive metal with a large surface area. It is usually connected to pcb components, including power transistors and switching devices. The function of this part is to absorb and dissipate heat.
PCB heat sinks work through the principle of conduction. According to this principle, heat is transferred from areas of high thermal resistance to areas of low thermal resistance and from areas of high heat to areas of low heat. Since it is made of aluminum or copper, both of which have excellent thermal conductivity and low thermal resistance, heat is naturally transferred from the PCB components to the heat sink.
The process works as follows:
The PCB component generates heat, which is naturally transferred from the component to the heat sink by the principle of conduction.
From there, the heat is dissipated over the large surface area of the heat spreader.
Heat is transferred through the surface area of the heat sink to the surrounding area. Many heat sinks have fins (rectangular pin-like features that extend perpendicular to the PCB surface) that help maximize the surface area and help transfer heat from the heat sink to the surrounding air.
keys to pcb thermal design
- Layout Design
Good PCB layout design can improve thermal performance. First, high power consumption components should be kept as far away as possible from poor heat dissipation areas, such as enclosed spaces or other heat sources. Secondly, the spacing between components should be reasonably planned so that the air flow is smooth. In addition, care should be taken to avoid overly dense wiring, which may hinder heat conduction and dissipation. - Heat Conduction
Since the resin in the board has poor thermal conductivity and the copper foil wires and holes are good heat conductors, the heat dissipation effect can be enhanced by increasing the residual heat rate of the copper foil and increasing the thermal conductivity. - Heat sink design
① Consider the size and shape of the heat spreader according to the power consumption and heat dissipation requirements of the PCB substrate.
② Material selection: aluminum or copper. Aluminum heat spreaders have better thermal performance and lightweight characteristics, while copper heat spreaders have higher thermal conductivity.
③ Installation location: It should be installed near the components on the circuit board that generate a large amount of heat, such as: power transistors, high-power resistors, integrated circuits (ICs) and so on. to ensure that the heat can be quickly transferred to the heat sink. At the same time, space limitations of the heat sink and interference with other components should be considered.
Other ways of heat dissipation
Reasonable use of heat sinks and through holes
Heat sinks use channels (via holes) through the PCB to conduct heat to the back to dissipate heat, and are generally configured directly below or as close as possible to the position of the heat generator.
In the case of a single-layer, double-sided PCB, it is necessary to connect the surface with the copper foil on the back side to increase the heat dissipation area and volume.
② In case of multi-layer PCB boards, heat dissipation can be accomplished by connecting other surfaces or partially connecting them.
③ Heat sink holes are located as close as possible to the heat source directly below the heating element. In the case where the heat source is not ideal, the heat vias can also be placed at the periphery of the component regardless of the component pad placement.
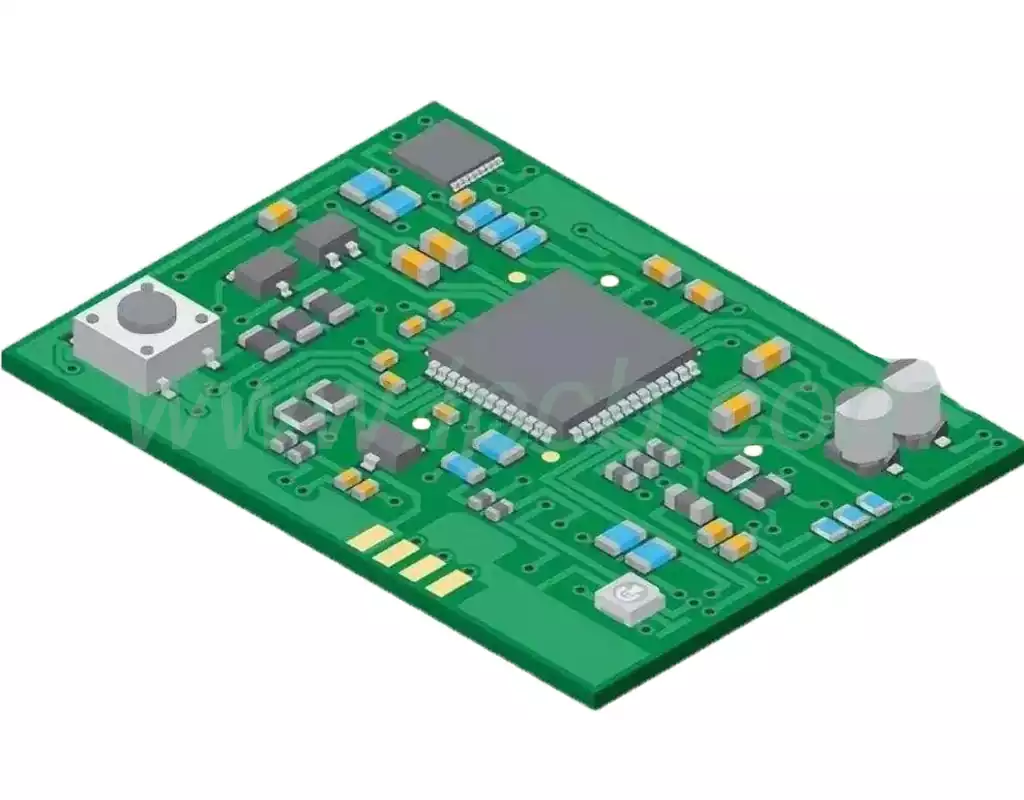
Benefits of Heat Sinks
These parts offer a wide range of benefits, including:
Thermal Management: The main benefit of heat spreader is their ability to improve thermal management in PCB design.These parts are ideally suited to solve numerous heat dissipation and cooling problems.
Long Lifespan: PCB heat spreaders have a long lifespan and do not need to be replaced after a long period of use. In addition, their use can help extend the life of the PCB through proper thermal management.
Low Cost: Most heat sinks are low cost, providing an economical solution for thermal management in PCB designs.
Lightweight: Many heat sinks are made of copper or aluminum, providing excellent thermal resistance without significantly increasing the weight of the board.
Heat Sink ChallengesWhile heat sinks offer a variety of advantages for PCB thermal management, they present significant challenges for PCB design. Some of the most prominent challenges facing PCB heat sinks include:
Mechanical connection difficulties: PCB heat spreader with mechanical connections, such as push pins and Z-clips, require anchors to be drilled into the board, which can cause damage if the design needs to be changed later.
Difficulties with non-mechanical connections: Adhesive or epoxy non-mechanical connections present a high risk of damage to the equipment due to mechanical stress during disassembly. In addition, the application of non-mechanical attachments is difficult due to the low flow characteristics of thermal adhesives and epoxies – these attachments must be perfect and free of air pockets for optimal thermal management, but achieving this requires stresses that can damage the board.
Removal Requirements: Another complication with PCB heat spreader is that the heat sink must be removable. If someone needs to service the board, they must be able to remove the heat sink without damaging the board.This is especially difficult with attachments that use adhesives.
Tips for Choosing the Right Heat Sink Attachment
Adding a heat spreader to a PCB can affect the design, especially the design’s ability to be reworked without damage. Consider the following factors when looking for the right heat spreader attachment for your PCB:Thermal Requirements: Before considering a heat sink, you need to know the thermal design profile (TDP) of the PCB component and its optimal operating temperature. This information will indicate the power consumption of the component and how much thermal management is required to keep it running.
Space requirements: Determine how much space is available in the design for the heat spreader. These components come in a variety of sizes and designs, so it is critical to understand the space available for heat sinks in the PCB design.heat spreader design: Once you understand the constraints and requirements of the PCB design, you should consider the different designs for the heat sink.These variables include material properties and dimensional characteristics such as the size of the heat sink, the number of fins on it, and the spacing between fins.
Mounting Techniques: Finally, consider how the heat spreader will be secured to the PCB. Depending on the specific heat spreader and design requirements, you may choose a mechanical or non-mechanical attachment technique. Either way, carefully consider the unique disadvantages of each connection technique.
The design and selection of PCB heat spreader is the key to ensuring stable performance and safe operation of electronic devices. In the pursuit of efficient heat dissipation, we also need to pay attention to the design challenges and installation problems it brings, in order to ensure the perfect integration of heat spreader and circuit boards.