Resin Plug Hole refers to the use of resin material to fill holes and defects in circuit boards to repair functional defects in circuits. Holes and defects in a circuit board may be created by processes such as drilling, plating, pressing, etc., or they may be designed to achieve specific electrical properties. For example, Via in pad (VIP) is a process in which through holes are set directly on the pads, which saves horizontal space and improves the density and interconnectivity of the circuit board, but it also leads to the outflow of resin in the through holes, which affects solder quality and reliability. Therefore, a resin plugging process is required to fill the through-hole with resin and then plating is performed to form a metal cap to ensure through-hole conduction and leveling.
Type:
Spraying method: Resin material is sprayed onto the circuit board to form a solid structure by drying and curing to fill holes and defects. This method is suitable for larger holes and smaller quantities, easy to operate and low cost, but less accurate and prone to bubbles and overflow.
Dip-coating method: The circuit board is immersed in resin material to form a resin film through adsorption and curing to fill holes and defects. This method is suitable for smaller holes and a larger number of holes, with higher precision and fewer bubbles, but the operation is complex and costly, requiring specialized equipment and processes.
In the resin hole plugging process, it is first necessary to pre-treat the through-holes on the circuit board, including cleaning, de-oxidizing and other steps to ensure that the resin can fully penetrate the hole wall. Subsequently, the pre-formulated resin material is filled into the through-hole by a specific process method and cured. The cured resin is tightly bonded to the hole wall, forming a strong insulating layer that improves the overall performance of the board.
Role of resin plugging holes:
It can improve the reliability and stability of pcb substrate.
In the traditional circuit board manufacturing process, due to the holes are not processed, easy to lead to the circuit board in the use of the process of welding corrosion, oxidation and other phenomena, thus affecting the circuit electrical performance. The use of resin plug hole process can effectively prevent these problems from occurring, to protect the long-term stability of the circuit board operation.
Can improve the moisture-proof performance of the circuit board.
In some special working environment, the circuit board is susceptible to humid air erosion, resulting in circuit board oxidation, corrosion and other problems. Through the use of resin plug hole process, can effectively isolate the humid air, prevent its erosion of the circuit board, improve the service life and reliability of the circuit board.
Can improve the insulation properties of printed circuit boards.
In the traditional circuit board manufacturing process, due to the holes are not dealt with, it is easy to lead to the gradual reduction of the line electrical spacing, and even short-circuit phenomenon. The resin plug hole process can effectively fill the holes and increase the insulation distance between the lines, thus improving the insulation performance of the circuit board and reducing the occurrence of short circuits.
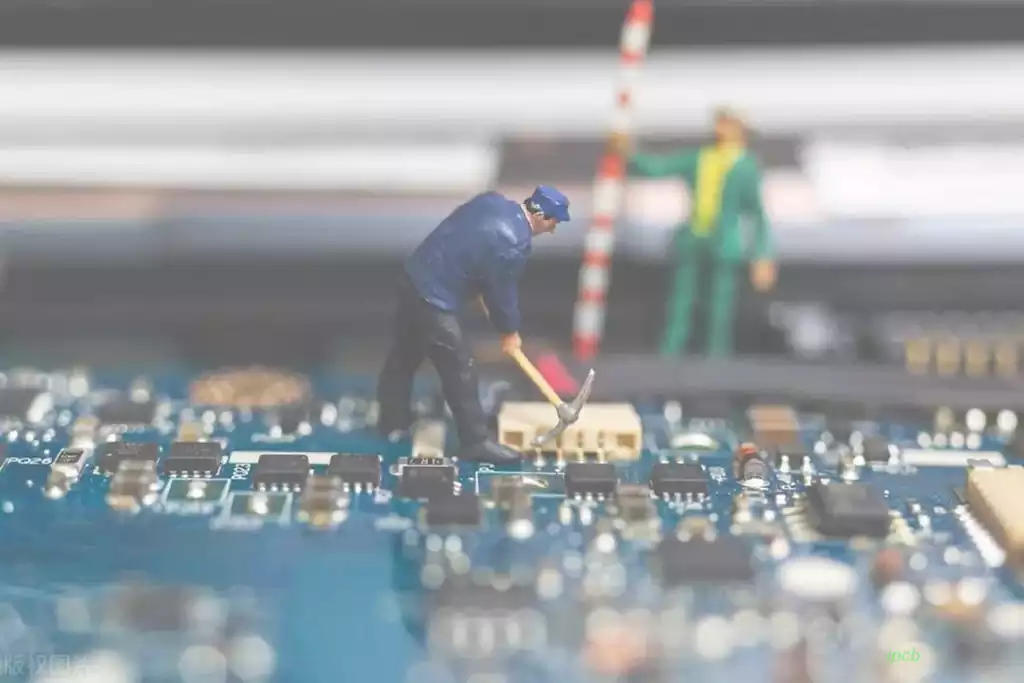
What is the difference between plating hole filling and resin hole plugging?
- The surface of plated hole filling and resin plugging is different.
Plating to fill holes is through the copper plating to fill the hole, the hole surface is full of metal, and resin plugging holes is through the hole wall copper plating and then filled with epoxy resin, and finally in the surface of the resin and then plated with copper, the effect is that the holes can be through, and the surface does not have indentation, does not affect the soldering. - Different processing procedures for plating hole filling and resin plugging holes
Electroplating hole filling is through the plating will be directly filled with holes, there is no gap, the benefits of welding, but the process requires high capacity, the general PCB manufacturers can not do. Resin plug holes is the hole wall after plating copper, filled with epoxy resin to fill the holes, and finally plated copper on the surface, the effect is similar to no holes, good for welding. - The price difference between plated hole filling and resin hole plugging
Plating hole filling has good oxidation resistance, but the technology requirement is high and the price is expensive. Resin plug holes have good insulation and are cheap.
In plating hole filling and resin hole plugging process is not popular before, PCB manufacturers generally use a relatively simple process of green oil hole plugging process, but the green oil hole plugging after curing will shrink, easy to air blowing problems, can not meet the user’s high saturation requirements. Electroplating hole filling and resin hole plugging technology will plug the buried holes of the inner HDI layer before pressing, which perfectly solves the disadvantages brought by green oil hole plugging and balances the conflict between the control of the thickness of the dielectric layer of pressing and the design of filling the buried holes of the inner HDI layer.
PCB resin hole plugging technology is a key step to improve the quality and reliability of circuit boards. Through the selection of suitable resin materials, optimization of process parameters and strict control of the production process, high-quality resin hole plugging effect can be achieved, providing a strong guarantee for the safe and stable operation of electronic equipment.