Porcelain ceramic substrate crown circuit boards are a special type of circuit boards that are usually made from high temperature ceramic materials. They are known for their excellent electrical insulation properties and high thermal conductivity characteristics, making them ideal for use in environments requiring high temperatures and high frequencies. These circuit boards are typically used in high-performance electronic devices in areas such as automotive electronics, aerospace and medical devices.
Porcelain ceramic substrate crown circuit board, which primarily utilize a metal core, cover a range of materials with similar physical properties and chemical structures. Aluminum nitride boards offer the highest thermal conductivity, but they are more costly.Comparatively, aluminum oxide boards are more economical, but their thermal conductivity is relatively low.Ceramic PCBs are significantly superior in thermal performance compared to traditional metal-core printed circuit boards because they do not require the addition of an electrically insulating layer between the core and the circuit alignment.
Manufacturers offer a variety of options for ceramic PCB metal substrates, including silicon nitride,silicon oxide and silicon carbide, and while copper and gold are also widely used, silver is a common material used for connecting the alignments at each layer.Using a layer-by-layer screen printing process, manufacturers place metal components or substrates layer by layer.
The bond between the ceramic material and the metal foil is high and the surface flatness is good.During the production process, the manufacturer uses a medium- or low-power CO2 laser with high precision, speed and efficiency to drill through-holes.Subsequently, photolithography is used to transfer the circuit pattern onto the metal foil, and the pattern is pre-plated with a tin-lead resist so that the unprotected portion can be removed by chemical etching. Removal of the tin-lead layer then requires cleaning using a nitric acid solution.
After the ceramic layers have been printed and stacked, the manufacturer fires the entire stack in an oven. ceramic boards are typically fired at temperatures below 1000°C. This lower firing temperature matches the sintering temperature of the metal traces, permitting the use of gold/silver as the metal traces in the low-temperature baking process on ceramic PCBs.
Unlike conventional circuit boards, ceramic PCBs do not utilize OSP, HASL or other common surface treatments. However, gold plating can be applied to exposed pads when there is a risk of silver corrosion.
- Categorized by Material
Crown porcelain ceramic substrate can be classified into various types according to the materials used, mainly including alumina (Al2O3), aluminum nitride (AlN), silicon nitride (Si3N4), and beryllium oxide (BeO) materials. Among them, alumina material is widely used because of its economy and good thermal shock resistance, but its thermal conductivity and thermal expansion can not fully meet the needs of high-power devices, while aluminum nitride and silicon nitride have more significant advantages in thermal conductivity and coefficient of expansion, which has become the future direction of development. - Categorized by process
Ceramic substrate crown circuit boards can also be categorized according to the different manufacturing processes, mainly including the following:
Direct Bonded Copper (DBC): This process produces composite substrates by directly sintering copper foil on the surface of the ceramic substrate through the hot melt method.
Low Temperature Co-fired Ceramics (LTCC): At a low temperature of about 850°C, circuits are formed by stacking and co-firing multiple layers of ceramic foils containing metal patterns, providing a good solution for the passive integration field.
High Temperature Co-fired Ceramics (HTCC): This process allows for sintering at temperatures up to 1600°C, making it suitable for small circuit boards and higher power applications.
Direct Plated Copper (DPC): A technology based on a membrane process where a metal layer is plated directly onto the surface of a ceramic substrate.
Active Metal Brazing (AMB): High-strength linkage between ceramics and metals is realized by solder containing active elements at high temperatures.
3.Categorized by the number of layers in the structure
According to the number of layers of the board, the crown porcelain ceramic substrate can be divided into:
Single-layer ceramic substrate: contains only one layer of circuitry and is suitable for simple applications.
Double-layer ceramic substrate: consists of two circuit layers, the structure is relatively simple.
Multi-layer ceramic substrates: usually with three or more layers of circuitry, suitable for complex circuit design, and support high-density connections
Properties of Porcelain ceramic substrate crown
- Thermal Conductivity
Porcelain ceramic substrate crown circuit boards are known for their excellent thermal conductivity, which can effectively dissipate the heat of the equipment in the process of operation. This high thermal conductivity not only improves the efficiency of the board, but also extends the life of electronic equipment, avoiding damage caused by overheating. - Low coefficient of thermal expansion
Ceramic materials have a low coefficient of thermal expansion (CTE), which allows the board to maintain good mechanical stability during temperature changes. This characteristic is particularly suitable for applications that require work in extreme temperature conditions. - Excellent electrical insulation properties
Porcelain ceramic substrate crown circuit board in the electrical insulation performance, can effectively prevent current leakage, to ensure the stability and reliability of the circuit. This makes ceramic circuit boards widely used in high-voltage and high-power electronic equipment. - High temperature and corrosion resistance
The high temperature resistance of ceramic materials makes it possible to work normally in high temperature environments without damage. In addition, ceramics have good chemical stability and corrosion resistance, and can be used in harsh environments for a long time. - Mechanical Strength
Porcelain ceramic substrate crown circuit board usually have high mechanical strength and are not easily deformed or broken, making them suitable for high-intensity and high-density circuit applications. This characteristic makes it excellent in aerospace, automotive electronics and other areas requiring high strength and performance. - Multilayer structure compatibility
Ceramics can be easily adapted to the structural design of multilayer circuit boards to support high-density circuit tracking layout, especially suitable for complex circuits and high-density multimedia interface applications. - Manufacturing Processes
Manufacturing processes for porcelain ceramic substrate crown circuit boards include low-temperature co-fired ceramics (LTCC) and high-temperature co-fired ceramics (HTCC), etc. Various processes are used to achieve specific performance requirements through different heat treatments and material combinations. This flexibility allows ceramic circuit boards to meet diverse market needs.
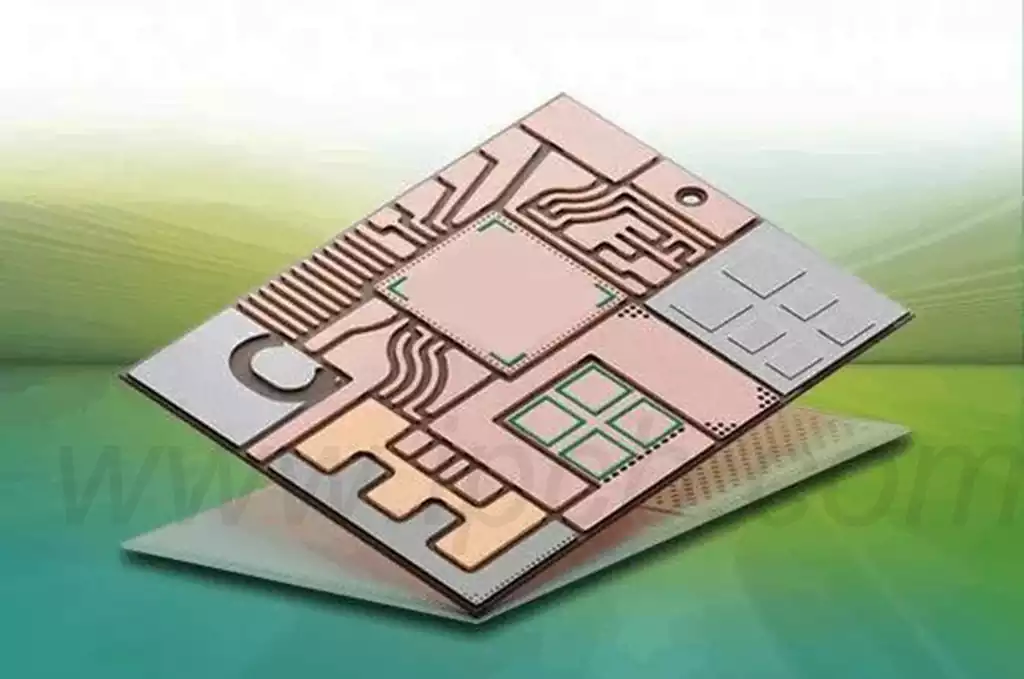
What are the mechanical properties of porcelain ceramic substrate crown circuit board versus FR-4 sheets?
Mechanical properties of ceramic circuit boards: Ceramic materials have high hardness and strength, but their relatively low fracture toughness means that ceramic circuit boards are more susceptible to brittle fracture under mechanical stress. Nevertheless, their hardness and strength are still sufficient for most electronic applications. Ceramic circuit boards are able to remain stable in high temperature and high pressure environments and are not easily deformed or aged, making them suitable for harsh operating conditions.
Mechanical Properties of FR-4 Sheet: FR4 sheet has good mechanical strength and toughness,and is able to withstand large mechanical stresses and impacts. This makes FR4 sheet excellent in applications that require mechanical strength and impact resistance.FR4 sheet has good flexibility and is not easy to break during installation and operation, making it suitable for equipment that requires frequent operation and adjustment.
In terms of mechanical properties, FR-4 sheets perform better in terms of impact and fracture resistance,while ceramic pcb require care to avoid excessive mechanical stress in applications.
Ceramic circuit boards and FR-4 sheets are suitable for different applications due to their different properties. Understanding their areas of application will help in choosing the right material.
Application areas for Porcelain ceramic substrate crown circuit boards:
High-power electronics: The high thermal conductivity of ceramic circuit boards makes them ideally suited for high-power electronic devices such as IGBT modules and power amplifiers.
LED lighting: In high power LED lighting, the heat dissipation capability of ceramic circuit boards significantly improves the life and efficiency of LEDs.
High-frequency communications: The low dielectric loss and high dielectric strength of porcelain ceramic substrate crown make them excellent in high-frequency communications equipment. Ceramic circuit boards are especially common in high-frequency applications such as satellite communications, radar and 5G base stations, ensuring efficient and stable signal transmission.
Application areas for FR-4 boards:
General electronics: FR-4 sheets are widely used in general electronics such as consumer electronics and medium power circuit boards.
Low-cost applications: Due to the low cost of FR-4 sheet, it is suitable for cost-sensitive electronic products, such as household appliances and small electronic devices.
Multilayer circuit boards: FR-4 sheet is easy to process and laminate and is widely used in the manufacture of multilayer circuit boards. FR-4 sheet excels in multilayer designs in computer motherboards, cell phones, and other consumer electronics, offering flexible design and processing advantages.
Porcelain ceramic substrate crown circuit boards show significant advantages in areas such as high-power electronics and high-frequency communications, thanks to their excellent thermal conductivity, electrical insulation and high-temperature resistance. Despite their relatively high cost, their reliable performance in harsh environments makes them an increasingly important part of future electronics. With the continuous progress of the manufacturing process, the application of ceramic PCB will have a broader future.