The Printed Circuit Board Heat Exchanger (PCB-HEX) is a highly efficient compact heat exchanger manufactured using printed circuit board technology, which is characterised by the fact that the metal wires and tubes are printed directly onto a thin-film substrate, and the structural design is similar to that of a traditional printed circuit board, hence the name.
The printed circuit board heat exchanger operates on a similar principle to a cold plate heat exchanger, but uses a printed circuit board as the heat transfer plate. Its main components include a heat sink, a plate heat transfer medium, and a heat source. During operation, the heat transfer medium flows within the heat-conducting layer on the printed circuit board, which effectively transfers heat from the heat source to the heat sink and thus exchanges heat. When designing printed circuit boards, in addition to considering the electrical conductivity of the circuit, special attention needs to be paid to the heat transfer performance of the printed medium, so as to achieve the optimal heat transfer effect through the reasonable selection and design of the printed medium.
Specifically, the workflow of a printed circuit board heat exchanger is as follows: the heat transfer medium flows from the heat source into the interior of the printed circuit board, flows along the path of the carefully designed thermal conductive layer, and transfers the heat carried to the heat sink. Subsequently, the heat sink radiates the heat to the surroundings through a heat sink such as a fan. Thermally conductive materials play a key role in this process, not only by efficiently conducting the heat from the heat transfer medium, but also by ensuring that the heat is dissipated effectively. As printed circuit boards are able to provide excellent heat transfer performance in a limited space, they have become a widely used thermal management solution in electronic products.
Printed Circuit Board Heat Exchanger Structure Design and Materials
Material Selection
In terms of material selection for printed circuit board heat exchanger ,consider using metal materials with better thermal conductivity such as aluminium and copper, which can improve the heat dissipation performance of the heat exchanger. In addition, the use of some thermal conductive materials with excellent thermal conductivity (such as silicone) is also a good choice.
Piping layout planning
When planning the piping layout of a printed circuit board heat exchanger ,it must closely match its actual application scenario.Usually,in order to maximise the heat dissipation area and enhance the heat dissipation efficiency,the piping should be arranged as densely as possible.At the same time,the diameter and length of the pipeline should be flexibly adjusted according to the specific heat transfer needs to achieve the best results.
Fluid parameter setting
In setting the fluid parameters of printed circuit board Heat Exchanger,different types of fluids need to be carefully selected for pressure, flow rate, temperature and other key parameters to ensure that its heat dissipation effect is maximised. For high-temperature fluids, consider direct heat dissipation or indirect heat dissipation with the help of heat exchangers to ensure that the heat dissipation efficiency is not affected.
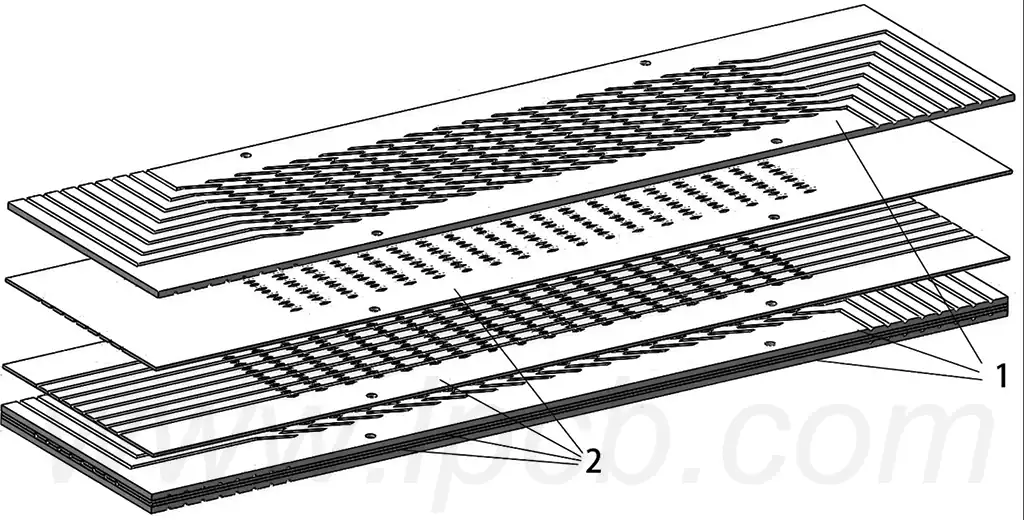
Heat transfer efficiency improvement strategy
In order to further improve the heat transfer efficiency of the PCB heat exchanger, a variety of optimization means can be taken, such as increasing the number of heat sinks, optimizing the arrangement of heat sinks, improving the fluid flow characteristics. In addition, combined with the actual application, fluid simulation analysis and experimental verification, to optimize the heat transfer efficiency and improve the stability of the same important significance.
Cost control programme
In terms of controlling the manufacturing cost of PCB heat exchangers, it can be achieved through reasonable design and selected materials. At the same time, the use of batch custom production mode can not only reduce costs, but also improve production efficiency and product quality, so as to achieve efficient heat dissipation at the same time, to ensure that the maximisation of economic benefits.
Advantages and disadvantages of printed circuit board heat exchanger
Advantages:
- Simple structure, low manufacturing cost.
- High heat transfer efficiency, to meet the heat dissipation needs of high-power electronic devices.
- Can achieve multi-channel heat exchange to meet the needs of a variety of application scenarios.
Disadvantages:
- The pressure and temperature range of PCB-HEX is limited due to the limitation of the manufacturing process of the pipeline.
- PCB-HEX has high maintenance and replacement costs.
Compared to conventional two-unit heat exchangers, printed circuit board heat exchangers (PCB-HEX) exhibit the following significant differences:
In terms of construction, the PCB-HEX’s thermal conduits are printed directly onto the circuit board, which is very different from the dual-unit heat exchanger’s thermal conduits that are connected by machining or soldering.
From the perspective of manufacturing costs, PCB-HEX is relatively inexpensive to produce, while dual-unit heat exchangers are relatively expensive to manufacture.
In terms of heat transfer efficiency, PCB-HEX demonstrates higher heat transfer performance, compared to dual-unit heat exchangers, which are slightly less efficient.
In terms of application, PCB-HEX is more suitable for the heat dissipation needs of high-power electronic devices, while dual-unit heat exchangers are more often used in industrial production and other broad areas.
Printed Circuit Board Heat Exchanger (PCB-HEX) has become an indispensable thermal management solution for modern electronic products due to its unique structural design, efficient heat transfer performance and wide range of applications. Compared with the traditional dual-unit heat exchanger, PCB-HEX not only has a significant advantage in manufacturing costs, but also in the heat transfer efficiency to achieve a significant improvement, perfectly adapted to the growing demand for heat dissipation of high-power electronic devices.