Welding paste is a homogeneous mixture, a paste with a certain viscosity and good thixotropy, which is a mixture of alloy solder powder, paste flux and some additives. It is a homogeneous and stable mixture. At room temperature, welding paste can initially stick electronic components to a given position. When the welding paste is heated to a certain temperature, as the solvent and some additives evaporate and the alloy powder melts, the welding paste reflows to interconnect the soldered components and pads, and forms a permanently connected solder joint after cooling.
Welding paste is a necessary material for the surface mount reflow process. It is a paste with a certain viscosity and good thixotropic properties, which is a mixture of alloy solder powder, paste flux (carrier) and some additives. Welding paste has many important uses in the production of surface mount components. Since it contains the flux required for effective welding, it is not necessary to add flux separately and control the activity and density of flux like plug-in components. Before reflow soldering, welding paste also plays a temporary fixing role during the placement and transmission of surface mount components. Welding paste is produced by professional manufacturers, and users should master the selection method.
With the application of reflow soldering technology, welding paste has become the most important process material in surface assembly technology and has achieved rapid development in recent years. In the reflow soldering process of surface mounting, welding paste is used to achieve the connection between the pins or terminals of surface mounted components and the pads. Welding paste coating is a key process in surface mounting technology, which will directly affect the welding quality and reliability of surface mounted components.
Welding paste is mainly composed of alloy solder powder and flux, which are mixed and stirred evenly to form a paste mixture. Among them, alloy solder powder accounts for 85% to 90% of the total weight, and flux accounts for 10% to 15%.
Alloy solder powder is made by spraying in an inert gas, and the particle size of the powder is determined by grading. The shape of tin powder is divided into spherical and amorphous, and the spherical shape is suitable for printing.
Commonly used alloy solder powders are lead and lead-free. Lead-containing solder powders include tin-lead (Sn-Pb), tin-lead-silver (Sn-Pb-Ag), tin-lead-bismuth (Sn-Pb-Bi), etc., among which the most commonly used alloy compositions are 63%Sn/37%Pb and 62%Sn/36%Pb/2%Ag; lead-free solder powders include tin-silver (Sn-Ag), tin-silver-copper (Sn-Ag-cu), etc., among which the most commonly used alloy compositions are 96.5%Sn/3.5%Ag and 93.6%Sn/4.7%Ag/1.7%Cu; with the improvement of environmental protection requirements, lead-free solder powders are increasingly widely used.
Flux
In welding paste, paste flux is the carrier of alloy powder. Its composition is basically the same as that of general flux. In order to improve printing effect and thixotropy, thixotropic agent and solvent are sometimes added. Through the action of the activator in the flux, the oxide film on the surface of the material to be welded and the alloy powder itself can be removed, so that the solder can quickly diffuse and adhere to the surface of the metal to be welded. The composition of the flux has a great influence on the spread, wettability, collapse, viscosity change, cleaning properties, solder bead splashing and storage life of the welding paste.
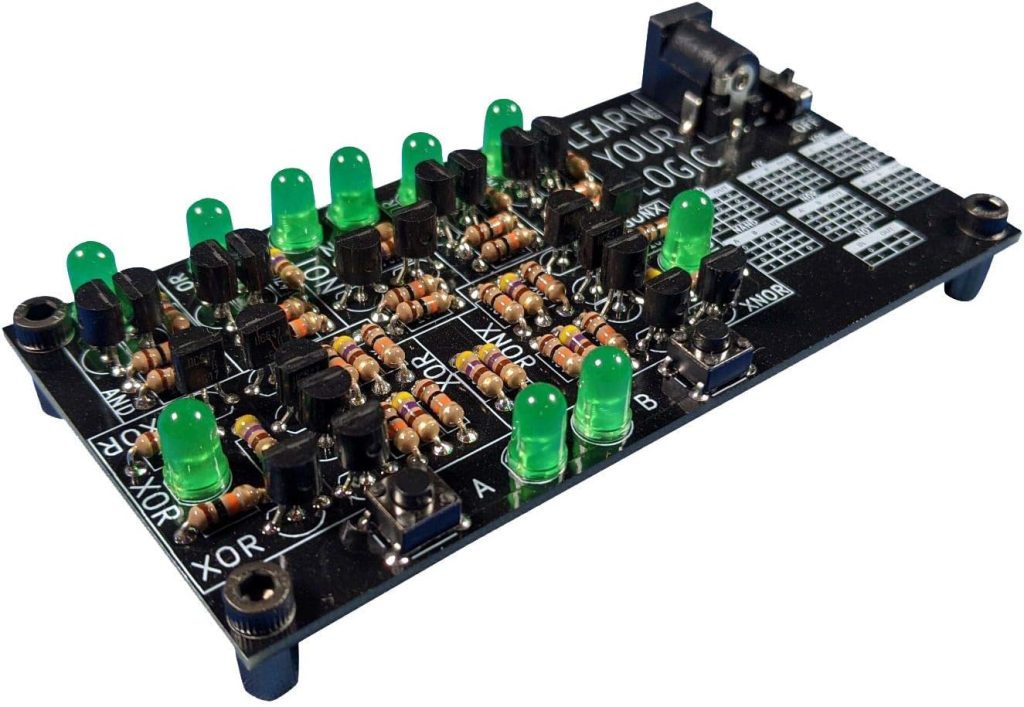
Selection of welding paste
Selection of flux activity
Flux is one of the main components of the welding paste carrier. Welding paste can use 3 different types of flux, namely R flux (resin flux), RMA flux (moderately activated resin flux) and RA flux (fully activated resin flux). The activator in the moderately activated resin flux and the fully activated resin flux can remove oxides and other surface contaminants on the metal surface, and promote the molten solder to infiltrate the surface mounted pads and component terminals or pins. According to the surface cleanliness of the surface mounted printed circuit board and the freshness of the components, medium activity can generally be selected, and high activity or non-active level, super active level can be selected when necessary.
Viscosity selection
The viscosity of welding paste is selected according to the coating method, and the viscosity of welding paste depends on the characteristics of the application process (such as screen aperture, scraper speed, etc.). For screen printing, the viscosity is usually selected to be 100-300Pa; for stencil printing, a high viscosity should be selected, ranging from 200-600Pa; for injection dispensing, the viscosity should be 100-200Pa.
Metal content selection
The metal content in the welding paste determines the size of the weld. The weld increases with the increase of metal percentage, but as the metal content of a given viscosity increases, a slight change in the metal content of the solder will have a great impact on the quality of the solder joint. For example, for the same welding paste thickness, a 10% change in metal content will cause the solder joint to go from excessive to insufficient. Generally, welding paste for surface mount components should be selected with a metal content of 88% to 90%.
Solder particle size selection
The shape of the solder particles determines the oxygen content of the powder and the printability of the welding paste. Spherical powder is better than elliptical powder. The smaller the sphere, the lower the oxidation ability.
In the electronics industry, I believe everyone has heard of electronic solders such as flux, welding paste, and welding paste. Flux, welding paste, and welding paste are all used in welding processes, and there are obvious differences between them.
- First of all, we can clearly see from the appearance that flux can be divided into solid, liquid and gas. The common and often mentioned flux in the soldering industry is liquid, while the so-called flux paste and welding paste are paste-like. The color of flux paste is transparent and yellowish, and the color of welding paste is gray or black.
- The main ingredients of flux and flux paste are rosin. The difference lies in the different production processes and the different proportions of solvents added to form different states. Flux is processed into a liquid by rosin, activator and some other additives, and is often used in conjunction with tin bar wave soldering process.
Welding paste is a paste flux material made from raw rosin and special chemicals. It plays an auxiliary welding role in the component welding process. It is a synthetic substance in the production process of welding paste. It is often used together with welding paste, or used with tin wire for post-welding and repair welding after the patch is completed.
Welding paste is a paste mixture formed by mixing solder powder, flux and other surfactants, thixotropic agents, etc. It is a new type of welding material that came into being with SMT. It is mainly used for welding electronic components such as PCB surface resistors, capacitors, and ICs in the SMT industry.
- Both flux and welding paste play an auxiliary welding role. In addition, they can remove surface oxides and prevent oxidation during welding operations; reduce the surface tension of the material, thereby improving the welding quality and significantly improving the wetting performance. Welding paste is like a medium between welding. Its main function is to weld electronic components. It can directly weld different components together, just like building a bridge.
Flux, welding paste, and welding paste are all indispensable materials in welding. The above are the differences between the three. Everyone must pay special attention when purchasing welding materials.
Almost all electronic devices are composed of printed circuit boards (PCBs), which are necessary for the operation of the equipment. Printed circuit boards have conductive copper tracks on which electronic components are soldered. The welding/soldering between these tracks and the components themselves is usually achieved through welding paste.
Welding paste is a mixture of metal in the form of alloy powder (about 90% by weight) and chemical components consisting of organic elements (about 10% by weight). The chemical part is usually called “flux” and is usually covered by trade secrets or patents. The purpose of the flux is to give the welding paste consistency and enable the parts to be properly soldered by eliminating oxides on its interface. In order to use welding paste under optimal conditions, it is important to understand the concepts described below.
In order to form a good solder joint, the metal surfaces to be soldered must be “cleaned” because they will oxidize when exposed to the environment and form compounds with oxygen, nitrogen, water and pollutants (such as sulfur) in the air. The degree of oxidation and the nature of the oxidizing chemical species determine the affinity between the metal atoms and these chemical species.
For example, 2 types of oxides form on the surface of copper. Copper oxides interact with carbon dioxide and moisture in the air to form carbonates. Iron behaves similarly to copper, while nickel produces a continuous oxide film. Silver reacts with trace amounts of hydrogen to form silver sulfide. Once these types of compounds form a layer on the metal surface, they can lead to passivation of the metal surface, resulting in poor wetting and, therefore, poor soldering.
In addition, soldering alloys also undergo surface oxidation, forming compounds with oxygen, water, and nitrogen on the surface that can also interfere with soldering. Therefore, good soldering requires the use of specific chemical compositions to “clean” the surface being soldered. A solder flux will perform this role and be able to counteract the effects of passivation, for example. In the case of electronic soldering, a solder flux must have the following properties 1.Remove the passivation layer to make the metal surface wettable by the solder alloy 2.Apply a layer of chemical, usually rosin, to the cleaned surface, which will act as an air barrier to protect before the molten solder is applied. 3.Provide the welding paste with the right rheology to ensure good printing of the welding paste and enable components to adhere, among other aspects. While the first function is primary, good results can only be achieved for PCB manufacturers if the flux also enables the other functions to be satisfactorily performed.
Welding paste must have properties that can meet the above requirements and be suitable for the manufacturing process of circuit boards with surface mount components. The properties to be considered are:
- Chemical activation
- Temperature or activation window
- Thermal stability
- Surface tension
- Wetting force
- Rheology
- Welding paste printing ability
- Toxicity
- Nature
- Amount of residues
With the improvement of material living standards, people’s environmental awareness is increasing. The toxicity of lead in solder is the most prominent, and some people have proposed to limit it. Although the amount of lead used in welding paste is less toxic than the amount of lead used in other occasions, it is also subject to restrictions, so how to choose and how to use it will be an important issue.