What is rigid flex PCB? Rigid Flex PCB is a type of printed circuit board that combines a rigid board with a flexible board. It has both the rigidity and stability of a rigid board and the bendability of a flex board. This unique structure allows rigid-flex PCBs to adapt to complex and changing assembly environments while realizing high-density wiring.
Rigid Flex PCB is significantly different from Flexible PCBs in several ways:
Structure and shape: hard flex PCBs are made of rigid substrates with good mechanical strength and stability, and can adapt to a certain degree of external deformation. Flexible pcb, on the other hand, are made entirely of flexible materials and can be bent freely, and are mainly used in applications that require frequent deformation, such as wearable devices and folding screen cell phones.
Application areas: hard flexible printed circuit boards are mainly used in the need to withstand greater pressure and complex deformation of the occasion, such as automotive electronics, aerospace, and other fields. Flexible circuit boards are mainly used in applications that require bending and deformation.
Performance characteristics: rigid flexible pcb with high-density wiring, high stability, high reliability, and other characteristics, can adapt to the complex and changing assembly environment. The flex pcb has good flexibility and foldability and can maintain stable performance in the bending process.
Manufacturing costs: Due to the manufacturing process of hard flexible circuit boards being more difficult, its manufacturing costs are relatively high. The manufacturing cost of flexible circuit board is relatively low because the manufacturing process is relatively simple.
Rigid Flex PCB is a printed circuit boards that combine the characteristics of rigid and flex PCBs with some unique advantages and disadvantages, as well as certain material requirements.
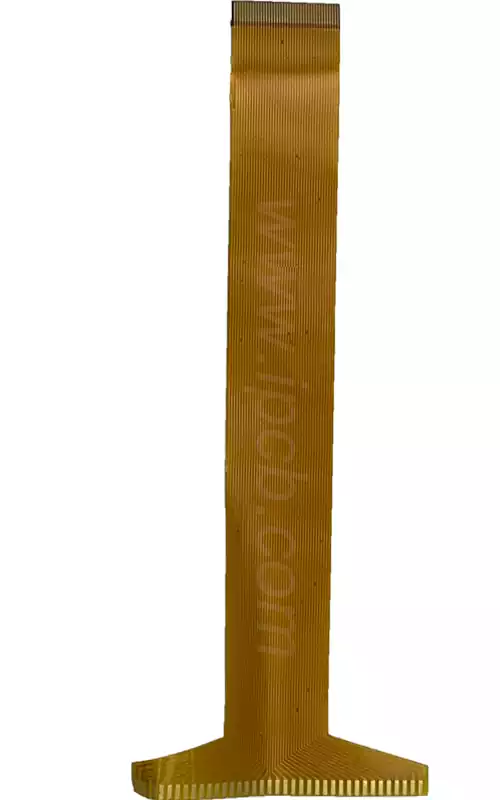
Advantages:
High performance: Rigid-flex PCBs combine the advantages of rigid and flex PCBs, featuring high-density wiring, high stability, high reliability, etc., and can adapt to complex and changing assembly environments.
Withstand greater pressure and deformation: Rigid-Flex PCB can withstand greater pressure and complex deformation and are therefore suitable for automotive electronics, aerospace, and other fields.
High efficiency: the manufacturing process is constantly advancing and improving, which can realize high-precision and high-efficiency production and reduce costs.
Disadvantages:
Difficulty in manufacturing: The manufacturing process of rigid flex PCB is difficult and requires high-precision equipment and specialized technicians for production.
High manufacturing cost: Due to the complexity of the manufacturing process of rigid-flex PCBs, the manufacturing cost is relatively high.
Thickness: The structure of rigid-flex PCBs is relatively thick, which is not conducive to miniaturization and lightweighting.
Requirements for materials:
Thickness: The thickness of hard flexible board is usually between 0.1mm and 0.5mm, so the thickness is an important indicator of the quality of flexible printed circuit boards. The thickness not only needs to meet the design requirements but also needs to maintain uniformity.
Conductivity: The conductivity of a flex circuit board is another important factor in the fabrication process. Since hard flex printed circuit boards need to realize high-density wiring, the conductivity requirements are higher.
Heat resistance: rigid flex pcb needs to be soldered and other heat treatment processes in the manufacturing process, so the heat resistance of the material has certain requirements.
Mechanical strength: rigid flex pcb needs to withstand greater pressure and deformation, so the mechanical strength of the material is high.
Environmental protection: With the improvement of environmental protection awareness, more and more companies are paying attention to the environmental protection of materials. When choosing materials, priority should be given to environmentally friendly materials to reduce pollution of the environment.
Rigid Flex PCB has a wide range of applications, mainly including the following areas:
Communication field: applied in connectors, camera modules, antennas, and other electronic components of smart terminals such as cell phones and tablet PCs.
Medical field: applied in a variety of medical equipment, such as electrocardiographs, monitors, and so on.
Automotive field: applied in automotive electronic control systems, such as instrument panels, air conditioning controllers, navigators, and so on.
Industrial control field: applied in various industrial control equipment, such as PLC, CNC machine tools, etc.
Consumer electronics: Because rigid-flex PCBs can be bent, they are ideal for manufacturing consumer electronics such as smartphones and tablets. These devices require frequent bending and twisting, and rigid-flex PCB can fulfill these needs.
As a kind of printed circuit board with cutting-edge technology and excellent quality, rigid-flex PCB has shown its unique advantages and application prospects in many fields. Despite some shortcomings and challenges, with the continuous progress of technology and market expansion, the development of rigid-flexible printed circuit boards is still very promising!