A pinner in the context of printed circuit board (PCB) fabrication is a key tool used during the assembly process to ensure precise and accurate positioning of components on the board. The primary role of a pinner is to securely hold electronic components in place on the PCB during the assembly stages, especially before soldering. This ensures that the components remain stable and do not move, which is critical for the integrity of the circuit and overall product performance. Pinners are employed to reduce misalignment, enhance production efficiency, and improve the overall quality of the assembled PCBs.
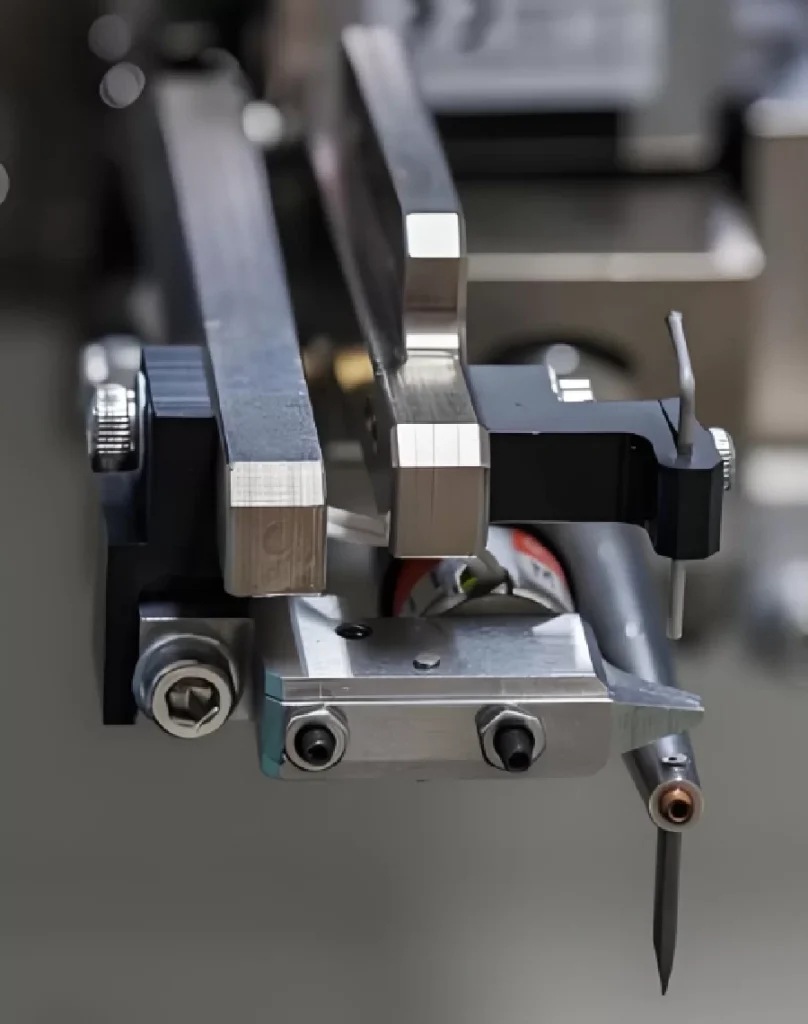
Importance of Pinners in PCB Assembly
In the intricate process of PCB assembly, ensuring that each component is accurately positioned is vital for the overall function of the device. A small misalignment or instability during the soldering process can lead to significant errors, malfunction, or even damage to the board and the components. Therefore, the use of a pinner has become integral to achieving higher accuracy and reducing assembly errors.
A pinner works by firmly holding components in place until the soldering process is complete. This allows manufacturers to produce high-quality PCBs that meet precise design specifications and standards, which is especially important in industries such as telecommunications, aerospace, and consumer electronics where PCB failure can result in costly product malfunctions.
How Does a PCB Pinner Work?
In simple terms, the pinner serves as a positioning tool. It operates by using mechanical pressure or air pressure (in pneumatic systems) to hold the component leads or surface-mount devices (SMDs) in position. The mechanism varies depending on the type of pinner in use and the specific assembly process (through-hole vs. surface mount technology).
Through-Hole Pinning Process: Through-hole technology (THT) involves inserting the leads of electronic components into holes drilled through the PCB. The pinner assists in aligning these leads precisely, ensuring that the components do not shift during the soldering process. This is critical as any movement can cause defective connections or electrical shorts.
Surface Mount Technology (SMT) Pinning Process: In surface-mount technology (SMT), components are placed directly onto the surface of the PCB without the use of leads. SMT pinning tools secure the components on the board surface while they are soldered. This technique is especially useful for handling smaller components, which require precision placement to avoid contact or misalignment issues.
Types of PCB Pinners
There are various types of pinners used in the PCB industry, each catering to different needs based on the assembly type and production scale.
- Manual Pinners: Manual pinners are simple tools operated by hand, ideal for small-scale production or specialized jobs where careful manual placement of components is required. These devices are often used in low-volume production environments or prototyping where high flexibility and operator control are needed.
- Automatic Pinners: Automatic pinners are commonly found in high-volume production lines. These machines can position and hold multiple components simultaneously with speed and precision, reducing assembly time and improving efficiency. Automatic pinners are often integrated into fully automated production lines, ensuring seamless PCB assembly and minimizing human error.
- Pneumatic Pinners: Pneumatic pinners use air pressure to secure components in place. They offer a stronger and more consistent hold compared to mechanical or manual pinners, making them suitable for complex and delicate components that require greater handling care. Pneumatic pinners are often used in advanced production environments where high precision and automation are critical.
The Advantages of Using a PCB Pinner
The use of pinners in PCB assembly offers several advantages that contribute to a more efficient and high-quality production process. Some of the primary benefits include:
- Increased Accuracy: Pinners help maintain the precise placement of components, reducing the risk of misalignment. Accurate placement is crucial for ensuring electrical connections function as intended and that the overall PCB operates effectively.
- Improved Production Efficiency: By automating or simplifying the task of holding components in place, pinners reduce the time required for assembly. This leads to faster production rates, especially when used in conjunction with automatic pinners on high-volume assembly lines.
- Reduced Assembly Errors: Pinners help minimize human error during the assembly process, as they secure components in the correct positions for soldering. This reduces the likelihood of issues such as poor solder joints or short circuits, improving the overall reliability of the final product.
- Enhanced Product Quality: Consistent and precise component placement ensures that each PCB meets the design and functional specifications, leading to higher-quality products. This is particularly important in industries where reliability and performance are critical, such as medical devices, automotive systems, and consumer electronics.
- Cost Savings: While the initial investment in pinner technology may be high, the long-term savings from reduced errors, rework, and defective boards can result in significant cost reductions. High-quality pinning helps ensure that products meet stringent quality control standards, reducing the risk of returns or warranty claims due to faulty products.
Challenges Associated with PCB Pinners
Despite their numerous advantages, pinners do have some challenges and limitations that must be addressed during the assembly process:
- Component Compatibility: Not all electronic components are compatible with every type of pinner. For example, certain surface-mount devices may require specialized pinning tools to handle their small size and delicate nature.
- Risk of Component Damage: Improper use of a pinner or applying too much pressure can damage sensitive components. Operators must be trained in the correct use of pinning tools to avoid accidental damage to the components or the PCB itself.
- High Initial Investment: The cost of purchasing and implementing automatic or pneumatic pinners can be substantial, which may be a barrier for smaller manufacturers. However, the long-term efficiency gains and quality improvements often justify the investment.
Future Trends of Pinner Technology
As the electronics industry continues to evolve rapidly, PCB manufacturing technologies are advancing in parallel, with Pinner technology playing a pivotal role. Here are several potential future trends for Pinner systems:
1. Smart Pinner with AI Integration
Future Pinner technology may incorporate artificial intelligence (AI) and machine learning (ML) to create a more automated and intelligent component securing process. By integrating sensors and AI algorithms into Pinner machines, the system could dynamically adjust the securing force, pressure, and angle based on the specific needs of each component, ensuring optimal positioning and precision.
For example, an AI-driven smart Pinner could detect the size, shape, and weight of components and automatically select the appropriate securing method, reducing the reliance on manual input. This automation will enhance the overall efficiency of production lines and reduce potential errors during the process.
2. Enhanced Real-Time Monitoring and Feedback Systems
As part of the shift toward smart factories, future Pinner systems may include real-time monitoring capabilities. By utilizing sensors that collect data on parameters like securing force, temperature, and pressure during the process, manufacturers can ensure each component is accurately secured in real time.
These feedback systems will allow immediate adjustments to fix potential issues before they become costly defects. Operators can remotely monitor the entire process and optimize settings based on the collected data, reducing the risk of human error and equipment failure.
3. Collaborative Pinner Robots (Cobots)
Collaborative robots (Cobots) are entering the PCB manufacturing field, and future Pinner systems may work alongside these robots. Cobots can assist in complex component assembly tasks while still allowing human workers to be involved. This combination enhances flexibility on the production line, particularly in environments where frequent component changes or small-batch production are necessary.
By collaborating with robots, Pinner technology can increase productivity while decreasing the workload on human operators, minimizing errors associated with manual operations.
4. Miniaturization and Precision Fixing
As electronic devices become more compact, the size of components on PCBs continues to shrink. Pinner technology will need to evolve towards greater miniaturization and precision fixing. By using finer tools and advanced robotic arms, future Pinner machines can handle micro-sized components with micron-level precision, securing them firmly on the PCB.
This level of precision will be especially crucial for emerging technologies such as flexible circuits and 3D integrated circuits, where even the slightest misalignment can lead to failures.
5. Environmental Sustainability
With growing global emphasis on sustainability, future Pinner technology may become more energy-efficient, reducing the energy consumption and material waste in the manufacturing process. Advanced Pinner machines might adopt green energy solutions, lower carbon emissions, and minimize the use of environmentally harmful materials.
Role of Pinner Technology in PCB Quality Control
In addition to enhancing efficiency in PCB component assembly, Pinner technology plays a critical role in ensuring product quality and consistency. Here’s how Pinner contributes to quality control in PCB manufacturing:
1. Precise Component Placement
Accurate component placement is fundamental to high-quality PCB production. Pinner technology securely fixes each component in place, ensuring they do not shift or deviate from the design location before soldering. Even in high-speed automated production lines, Pinner ensures uniform securing, preventing misalignment or angular deviation.
This precision is vital for maintaining circuit connectivity and performance, especially in multilayer PCBs and high-density interconnect (HDI) designs, where even minor misalignment can result in short circuits or functional failure.
2. Reduction of Soldering Defects
Soldering is a crucial step in PCB manufacturing, and any component movement or instability can lead to soldering defects. Pinner ensures that components remain stable during the soldering process, reducing common defects such as cold solder joints, dry joints, or short circuits. This improves solder reliability and reduces rework and scrap rates, ultimately increasing yield.
Using automated or pneumatic Pinner systems, production lines can more rapidly and accurately secure components, minimizing soldering issues caused by human error.
3. Enhanced Repeatability and Consistency
Manual operations often lead to inconsistencies, whereas automated Pinner systems offer a high level of repeatability. This consistency is crucial for mass production, ensuring that components are secured in the same position on every PCB, which contributes to consistent product quality.
By improving repeatability, production lines can pass quality control checks more quickly, reducing delays and costs associated with inconsistent quality.
4. Optimized Manufacturing Processes
By utilizing advanced Pinner systems, manufacturers can optimize their entire production workflow. For example, Pinner machines with built-in smart monitoring and feedback systems can automatically adjust securing parameters to match specific component or PCB types. This not only improves production efficiency but also minimizes production faults caused by inappropriate securing methods.
Optimized processes lead to higher throughput and lower defect rates, which is particularly important for manufacturers dealing with complex circuit designs.
5. Lower Defect and Rework Costs
Because Pinner technology significantly reduces component movement during and after the securing process, it minimizes the chances of defects in the manufacturing process. Fewer defects mean fewer instances of rework, thus lowering overall production costs. High-quality Pinner operations help manufacturers avoid common soldering and assembly errors, improving efficiency and economic performance.
Conclusion
In the realm of PCB manufacturing, the role of the pinner is crucial for ensuring accurate component placement, improving efficiency, and maintaining high-quality standards. Whether manual, automatic, or pneumatic, pinners are instrumental in reducing errors and enhancing the overall production process. As technology continues to advance, innovations such as smart pinners and collaborative robots are likely to shape the future of PCB assembly, offering new levels of precision and efficiency.
In summary, the importance of using a pinner in PCB assembly cannot be understated. By investing in pinning technology and understanding the nuances of its application, manufacturers can achieve greater product consistency, reduce defects, and improve overall operational efficiency.