In the pcba assembly process, welding is a key step in connecting various components together. In order to ensure the quality and effect of welding, pcba pre-soldering preheating becomes a link that cannot be ignored.
What is PCBA pre-soldering heat?
When technicians and practitioners hear the term ‘temperature profile’, smt reflow soldering comes to mind. Along the large soldering area, it is easy to see the 4 main temperature control zones that result in a perfect solder joint. At each stage, the technician uses his experience, trial and error, strict control and improvement, and each stage improves the quality of the solder joint and reduces defects. But other industrial soldering equipment may not have such precise temperature control, but they all have the preheating stage in common.
The flux burning pre-heating stage in selective wave soldering serves to steadily increase the temperature of the entire pcba assembly from room temperature to a holding temperature below the melting point of the solder paste, approximately 150°C.The flux burning pre-heating stage is used to control the temperature of the solder paste. The temperature change is adjusted so that the slope is maintained at a few degrees per second.The period of time following the pre-heating stage is the homogenising period, which will hold that temperature for a period of time to ensure that the board is heated evenly. The reflow stage is then entered to start solder joint formation. During the pre-heating and soaking process, the volatile solvents in the solder paste are burned off and the flux is activated.
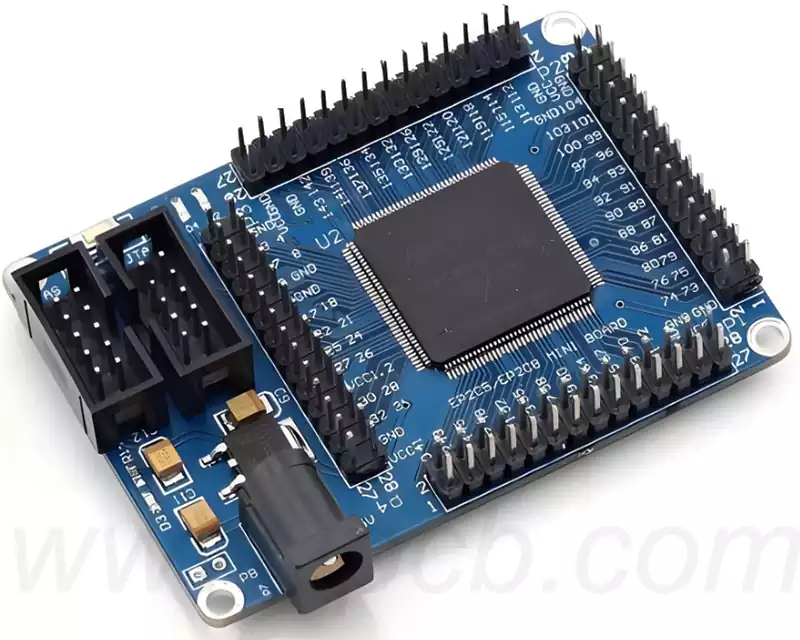
The importance of preheating before wave soldering:
1.In the PCBA welding processing flux plays an important role,and flux has a large number of rosin and active agents, these substances require a certain temperature to decompose and activate the reaction,so pre-heating the circuit board in advance can maximise the role of flux to effectively remove the surface oxides of the PCB board pads and components of the pins to ensure the quality of welding.
2.Before the welding process,stored in the air on the surface of the circuit board will inevitably absorb some moisture,become wet.If you do not preheat,direct welding,the circuit board in the water vapour encountered at high temperatures will rapidly evaporate into water vapour,water vapour contact with the solder paste will produce spattering,reasonable preheating can be avoided to avoid spattering brought about by the empty weld.Leakage.Holes and solder beads and other welding defects.
3.Due to the size of the components. Size.Thickness of different components, without taking into account these conditions directly for welding will lead to components of the rapid heating thermal stress damage to some of the components,so we need to determine the heat capacity of the components,pre-heating,before the formal welding so that the temperature of each component to achieve the same, to ensure the quality of welding.
Preheating method
Selection of welding preheating unit can be divided into bottom preheating and top preheating.
a.Bottom preheating method for short-wave infrared, characterised by fast preheating speed, less damage to the active ingredients of the flux.
b.The top preheating method is generally used in the form of hot air,so that the PCB and parts of the full preheating,especially for faster heat dissipation of the PCB and parts of the role of the particularly obvious —- for the OSP treatment process of PCB, such as unnecessary,can be closed to the hot air preheating method. Because after the flux removes the OSP of the PCB pad, the hot air is easy to make the pad exposed copper foil secondary oxidation,which is not conducive to solder infiltration.
Preheat parameter setting
In general,the preheating parameters are set based on the performance parameters of the flux,in the preheating is completed, the temperature of the PCBA solder joints should be in the flux activation temperature range (now on the market using alcohol-based flux,activation temperature range is generally 90-120C) —- If there are heat-sensitive components, preheating parameter settings need to take into account the temperature of the thermal components requirements.
If it is a faster heat dissipation PCBA,in order to achieve the requirements of the fill rate of the solder joints,sometimes need to appropriately increase the preheating temperature of the solder joints. In the case of flux performance parameters can not be taken into account,should be the main requirements of the solder fill rate.
PCBA preheating before welding is to ensure the quality of welding,avoid welding defects and improve the reliability of electronic products is an important part. By reasonably selecting the preheating method and accurately setting the preheating parameters,technicians are able to optimise the soldering process and provide a solid guarantee for the manufacture of electronic products.