In the electronics manufacturing industry,wave soldering, as an important connection technology, is widely used in the assembly process of circuit boards. However, in practice, excessive tin impurities and the generation of tin dross after wave soldering have been a problem for manufacturers. These problems not only affect the soldering quality, but also increase the production cost.
Wave soldering after tin impurities exceeded the standard and dross produced by the cause of analysis:
1.Tin impurities exceed the standard and the main reason for the generation of dross
Tin furnace in the copper and trace element content is too high: wave soldering process, due to the circuit board on the copper wire and electronic feet in the iron elements may enter the furnace, the long-term accumulation of copper and iron content exceeds the standard. When the copper content of more than 0.8%, iron content of more than 0.05%, will significantly increase the generation of slag, affecting the quality of welding.
Operating temperature is too high: wave furnace operating temperature is too high is also an important cause of slag generation. High-temperature environment, the solubility of copper, iron and other elements increase, it is easier to exceed the standard, thus accelerating the generation of tin slag.
Furnace cleaning is not timely: long-term not to clear the furnace operation, the impurity content in the furnace will gradually accumulate, which is also an important factor causing excessive tin slag.
Solution
Regularly test the composition of the furnace: Regularly test the tin in the wave furnace, once found that the copper content of more than 0.8%, iron content of more than 0.05%, should be replaced in a timely manner in the furnace tin. It is usually recommended to replace the tin in the wave furnace about once a month.
Control the operating temperature: Reasonable control of the operating temperature of the wave furnace (recommended between 260-275 degrees Celsius), and regularly test the accuracy of the temperature gauge. At the same time, choose better quality flux to ensure that the soldering process is carried out at the appropriate temperature.
Spot-check the quality of soldering materials: Spot-check the soldering materials, test their composition and impurity content, and avoid using low-quality soldering materials made from secondary recycled tin slag.
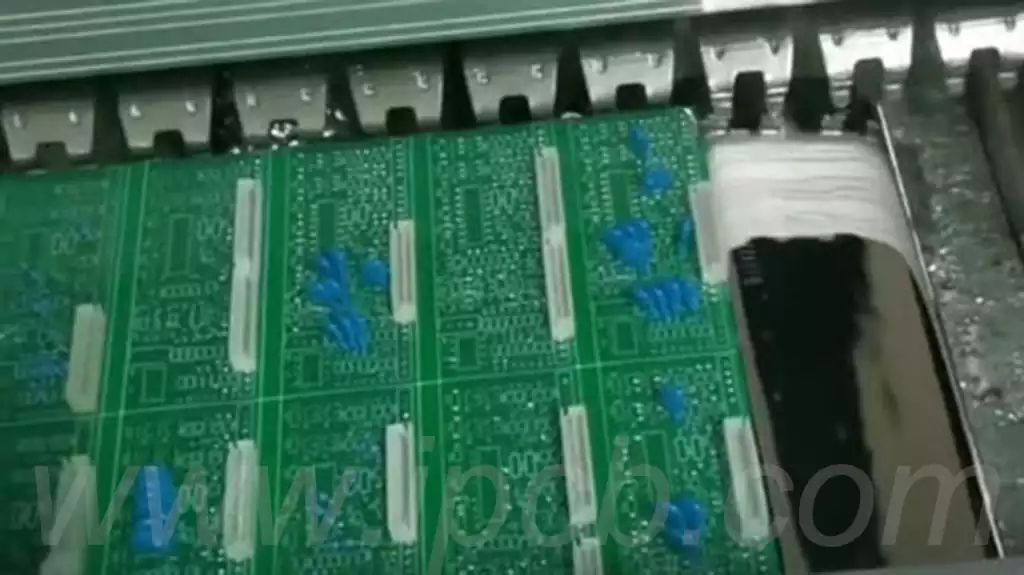
2.Reasons for the generation of semi-oxidised tin (tofu dregs)
Wave furnace design defects: some of the wave furnace design is unreasonable, such as the peak is too high, the peak platform is too wide, the distance between the dual wave furnace is too close, as well as the use of rotary pumps, etc., may lead to a decrease in temperature of the solder in the process of dropping, mixing air, which triggers the phenomenon of oxidation and semi-dissolution, increasing the generation of tin slag.
Improper temperature control: For lead-free SN-CU0.7 solder bars,the wave soldering temperature is usually controlled between 280 ℃ ± 5 ℃. If the temperature is low, the tin material can not achieve a good dissolution state,indirectly leading to excessive slag.
Large contact area between tin and air:the larger the contact area between molten tin and air, the easier it is to produce slag. Spray out of the molten tin if the direct fall into the furnace, easy to bring in the air,resulting in the generation of semi-oxidised tin.
Slag clearance is not timely: the failure to frequently clean up the slag, resulting in the peak of the fallen solder can not enter the furnace as soon as possible, but to stay on top of the slag, uneven heat, will also accelerate the generation of slag.
Solution:
Pre-treatment inspection of tin slag: Before starting the tin furnace for soldering operations, be sure to carefully check whether there is any residual tin slag, especially in the wave motor area and the wave runner opening and other critical areas. For the tin slag left after the last operation, it should be cleaned immediately and thoroughly to ensure that the furnace is in the best working condition.
Furnace tin level monitoring: It is vital to maintain the tin level in the furnace within the appropriate range, and it is recommended that the tin surface should be 0.5 to 1cm high near the furnace opening when the wave is stopped. Insufficient tin will result in a larger area of contact with air, increasing the risk of oxidation, while the drop of the wave waterfall and the impact of the liquid tin will increase accordingly, thus promoting the formation of slag. Therefore, once the amount of tin is found to be on the low side, tin bars should be replenished into the tin furnace immediately.
Furnace Temperature Adjustment: When the working temperature is low, hot tin is prone to form a hard-to-melt build-up in the process of refluxing from the spout to the furnace. In order to reduce such phenomenon, it is recommended to increase the working temperature of the tin furnace appropriately within the range that the product can bear.
Regular slagging operation:It is recommended that the operator implement a regular slagging system, which must be carried out before the end of each day. In the process of slagging,without soldering operations,the furnace temperature can be moderately increased by about 10 ℃ (subject to the actual temperature), and use a small amount of reducing powder to assist in slagging. Reduction powder can effectively accelerate the separation process of tin and dross, significantly reducing the amount of tin dross generated, thereby improving the quality and efficiency of welding.
Wave soldering connection after the tin impurity exceeds the standard and the generation of dross is the result of a combination of factors. In order to effectively solve these problems, manufacturers need to take comprehensive management measures. Only in this way can we ensure stable quality of wave soldering, improve productivity, reduce production costs, and provide a strong guarantee for the sustainable development of the electronics manufacturing industry.