In modern electronic devices, circuit card assembly are a core part that carries signal transmission, data processing and various control functions. Whether in smartphones, computers, or industrial automation equipment, circuit card components play an indispensable role. This article will explore the composition, functions, manufacturing processes and future development trends of circuit card components.
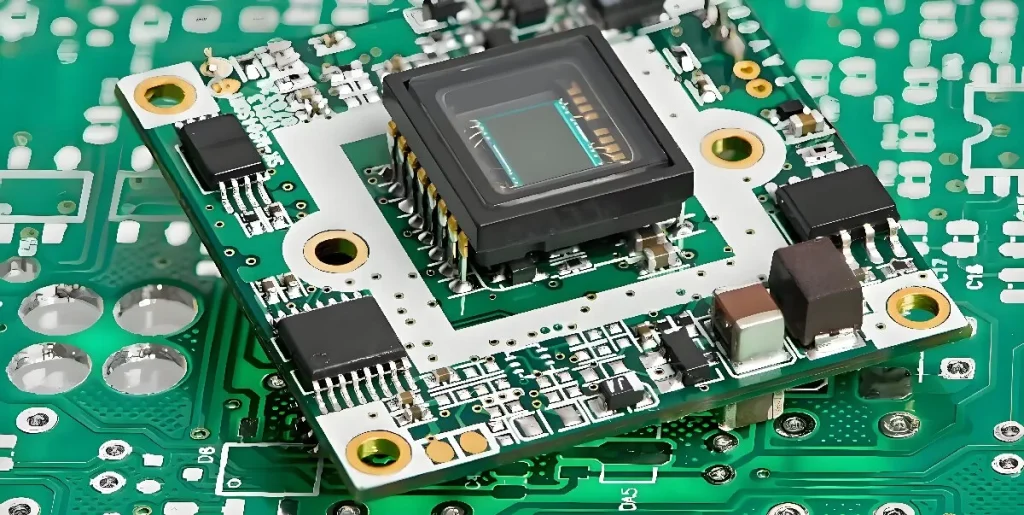
Definition and function of circuit card assemby
Circuit card components are modular systems formed by multiple electronic components connected by circuits, which are used to complete specific electronic functions. Its main functions include:
Signal transmission and processing
In electronic devices, circuit card components are responsible for receiving, transmitting and processing various signals. Whether it is audio, video, or data signals, they need to be processed and distributed through circuit card components.
Control function
Circuit card components are often used to control the operating status of equipment. For example, in smart home appliances, circuit card components can control parameters such as temperature and speed.
Data storage and calculation
Some complex circuit card components have built-in storage and computing capabilities, which can store data and quickly calculate, providing support for the intelligence of equipment.
Components of circuit card components
Electronic components
The core components of circuit card components are various electronic components, such as resistors, capacitors, transistors, integrated circuits, etc. These components realize specific circuit functions through reasonable layout and connection.
Printed Circuit Board (PCB)
PCB is the carrier of the circuit card assembly, which is used to support electronic components and provide electrical connections. It consists of multiple layers of conductive copper foil and insulating materials, and its design is complex and precise.
Interfaces and Connectors
Circuit card assemblies are usually equipped with a variety of interfaces and connectors for communication and signal transmission with external devices.
Housing and heat dissipation system
High-performance circuit card assemblies need to have good heat dissipation performance, so they are usually equipped with metal housings and heat sinks.
Manufacturing process of circuit card assemblies
Design stage
The design of circuit card assemblies is the starting point of the manufacturing process. Designers need to draw circuit schematics according to functional requirements and generate PCB layout diagrams through EDA tools.
PCB manufacturing
PCB manufacturing includes multiple steps such as cutting, pattern transfer, etching, drilling, and electroplating of copper clad boards. This process requires high-precision equipment and strict quality control.
Component mounting and welding
After the PCB manufacturing is completed, the electronic components need to be mounted on the PCB and soldered by reflow soldering or wave soldering process. The installation methods of patch components and plug-in components are different, using SMT and THT technology respectively.
Testing and debugging
After manufacturing, the circuit card components need to undergo rigorous testing and debugging, including functional testing, performance testing, reliability testing, etc., to ensure that they meet the design requirements.
Assembly and packaging
The tested circuit card components will be assembled into the final device and packaged for transportation and use.
Application areas of circuit card components
Consumer electronics
In consumer electronic products such as smartphones, tablets, and TVs, circuit card components implement core functions such as signal processing, image display, and data storage.
Industrial automation
Circuit card components are widely used in industrial automation equipment, such as PLCs (programmable logic controllers), inverters, and sensors, providing reliable control and monitoring capabilities for industrial production.
Automotive electronics
With the increasing degree of automotive electronics, circuit card components are increasingly used in automobiles. For example, engine control units (ECUs) and ADAS (advanced driver assistance systems) are inseparable from circuit card components.
Medical equipment
Many medical devices are equipped with high-precision circuit card components for data acquisition, signal processing and control functions, such as CT scanners and electrocardiographs.
Communication equipment
In base stations, routers and fiber-optic communication equipment, circuit card components are responsible for signal transmission and data processing, and are the basis of communication networks.
Development trend of circuit card components
High-density integration
As the functions of electronic products become increasingly complex, higher requirements are placed on the integration of circuit card components. In the future, the size of components will be smaller, while the functions will be richer.
High performance
High performance is an important direction for the development of circuit card components. For example, in the fields of 5G and artificial intelligence, there are extremely high requirements for the computing power and data processing capabilities of components.
Environmental protection and low power consumption
Modern electronic products pursue environmental protection and energy saving. Circuit card components need to adopt low-power design and use recyclable environmentally friendly materials.
Intelligent manufacturing
Intelligent manufacturing technology is gradually being applied to the production of circuit card components. For example, the use of artificial intelligence and big data technology can achieve optimization of production processes and improvement of quality.
Reliability and safety
With the expansion of application areas, circuit card components need to have higher reliability and safety. For example, in the aerospace and military fields, component failure may lead to serious consequences.
Optimized design of components in circuit card assemblies
In the design process of circuit card assemblies, the selection and optimal configuration of components are crucial. Designers need to select appropriate electronic components according to circuit requirements, such as using low ESR capacitors to reduce power consumption and selecting high temperature resistant resistors to cope with harsh working environments. In addition, the layout between components needs to be considered to optimize the signal transmission path, reduce signal interference, and improve the overall performance of the circuit.
Heat dissipation management of circuit card assemblies
With the continuous improvement of circuit card assembly performance, heat dissipation management has become an important challenge. Traditional passive heat dissipation methods, such as heat sinks and fans, have gradually transitioned to active heat dissipation methods, such as liquid cooling systems and thermoelectric cooling modules. In order to further improve the heat dissipation efficiency, a thermal conductive material layer can also be added to the PCB design, and the heat dissipation path can be optimized through finite element analysis.
Reliability verification of circuit card assemblies
In actual applications, the reliability of circuit card assemblies is directly related to the stability of the equipment. Reliability verification includes temperature cycle testing, vibration testing, and wet heat environment testing. Through these tests, potential design defects can be discovered and improved, thereby improving the service life and performance of components.
Co-optimization of circuit card components and software
Modern circuit card components require not only hardware optimization, but also seamless collaboration with software. For example, in automotive ECUs, software can reduce hardware resource usage by optimizing algorithms, thereby reducing system costs. In addition, with the development of FPGA technology, software can adjust hardware functions by dynamically loading configuration files, making circuit card components more flexible.
Quality traceability system for circuit card components
In order to ensure the quality of each circuit card component, many manufacturers have introduced a quality traceability system. From raw material procurement to production, testing, and finished product shipment, every link is recorded and archived. This not only helps to identify problems and improve processes, but also quickly trace the root cause when components fail.
Case analysis: Application of circuit card components in smart homes
Take smart door locks as an example. The core is the built-in circuit card component. This component needs to achieve low power design to extend battery life, and also needs to have wireless communication capabilities to connect with other smart home devices. By optimizing PCB wiring and selecting efficient power management chips, the circuit card components of smart door locks achieve stable and efficient performance.
Material innovation of circuit card components
Traditional circuit card components usually use FR4 as the PCB substrate, but in high-frequency applications, the dielectric properties of FR4 may not be ideal. Therefore, modern circuit card components have begun to adopt high-performance materials, such as PTFE substrates, to meet the needs of high-speed signal transmission. In addition, metal substrates with good thermal conductivity are also widely used in LED driver circuit card components to improve heat dissipation performance.
How to choose high-quality circuit card components
Performance indicators
When selecting circuit card components, you need to pay attention to their performance indicators, such as operating frequency, power range, and data processing capabilities, to ensure that they meet application requirements.
Compatibility
The compatibility of circuit card components directly affects the stability and user experience of the device. High-quality circuit card components need to support multiple communication protocols (such as I2C, SPI, and CAN bus) and seamlessly connect with other devices. For example, in industrial control systems, multiple circuit card components need to work together to transmit precise data and instructions. To ensure compatibility, components must be designed in accordance with international standards and undergo rigorous protocol testing during the manufacturing process.
Security design of circuit card components
With the popularity of IoT devices, the security of circuit card components has become a critical issue. Malicious attacks may invade devices through circuit card components, causing data leakage or even device loss of control. To improve security, modern circuit card components usually integrate hardware encryption modules (such as TPM chips) and support secure boot functions to prevent illegal access from the hardware level. In addition, optimizing PCB design and reducing electromagnetic leakage paths are also important means to improve component security.
Intelligent development of circuit card components in the future
Self-diagnosis and repair Future circuit card components may have self-diagnosis and repair functions. When the component detects an abnormality in the internal circuit, it can switch to a backup circuit through a built-in algorithm, or rebuild the damaged part through a programmable logic module.
Modularity and customizability With the diversification of customer needs, modular design is becoming a trend. Users can flexibly combine different functional modules according to their needs, thereby reducing development cycles and costs. For example, some manufacturers have begun to launch stackable circuit card components, with each layer implementing different functions for easy expansion.
Combined with artificial intelligence The introduction of artificial intelligence technology makes the functions of circuit card components more intelligent. For example, real-time analysis of sensor data through AI algorithms can achieve more accurate environmental perception and control. This has broad application prospects in areas such as unmanned driving and smart homes.
Application of circuit card components in extreme environments
In extreme environments such as aerospace and deep-sea exploration, circuit card components need to have higher radiation resistance, high temperature resistance and shock resistance. For example, circuit card components in spacecraft usually use radiation-resistant component materials and improve reliability through triple redundancy design. In addition, in order to adapt to the high pressure of the deep-sea environment, the component housing usually uses high-strength titanium alloy and uses sealing strips for waterproofing.
Sustainable development of circuit card components
With increasingly stringent environmental regulations, the sustainability of circuit card components has become a focus of attention for manufacturers. Green circuit card components reduce the use of harmful materials (such as lead and halogens) in design and reduce power consumption by optimizing circuit design. In addition, the recycling and reuse of discarded circuit card components is also gradually being promoted. For example, some high-value metals (such as gold, silver and copper) can be extracted from waste components and used to make new products.
Conclusion
As the core of modern electronic devices, circuit card assembly play a vital role in consumer electronics, industrial automation, communication equipment and other fields. With the rapid advancement of technology, the integration, performance and reliability of circuit card components will continue to improve. At the same time, the trend of environmental protection and intelligent manufacturing will also lead its future development direction. Through continuous optimization of design, material innovation and manufacturing process, circuit card components will surely provide a solid foundation for the intelligent and green development of electronic equipment.